This facility is also one of the first in Europe to benefit from IMI Insyt, a prescriptive engineering service that analyses operational data to improve efficiency. Having already been successfully deployed across North America, IMI Insyt recently conducted an in-depth study at Riverside 1, uncovering key insights to enhance performance.
Tackling Water Hammer Issues
IMI Insyt enables site managers to identify and address operational inefficiencies by analysing existing operating data rather than using invasive monitoring tools. At Riverside 1, Assistant Operations Manager Alan Neeson, in collaboration with IMI’s UK and Ireland Business Partner GPEC Ltd., sought a solution for water hammer—a damaging phenomenon affecting electricity production.
Water hammer, caused by sudden pressure changes, was forcing Riverside 1 to keep its drain valves permanently open. While this prevented further damage, it also resulted in significant steam loss, reducing efficiency and affecting power generation. Recognising the financial and operational impact, Cory Group commissioned IMI Insytto investigate.
Identifying the Root Causes
IMI’s engineers conducted a year-long, physics-based analysis of Riverside 1’s drainage system, valve operation, and plant logic. Their findings confirmed that excessiveflow velocities and abrupt pressure and temperature shifts were creating excessive condensate. This was due to the bypass station remaining in standby mode, allowing upstream pipes to cool down. When the station was reactivated, hot steam passed through the cold piping, generating more condensate and triggering water hammer.
Additionally, the shut-off valve upstream caused pressure shocks, while thermal shocks occurred when hot steam entered a cold system. IMI Insyt identified these three main issues and proposed targeted solutions.
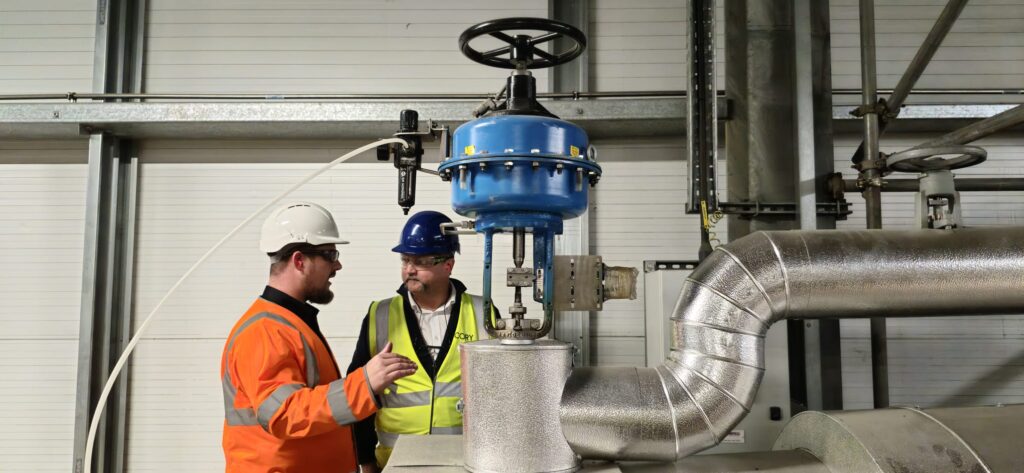
Small Interventions, Big Results
IMI recommended pre-heating the system to prevent condensate formation during standby mode. This was achieved by bypassing the control valve—one of the simplest and most effective preheating methods.
They also advised keeping the high-pressure/low-pressure bypass system (HPLP-SOV) permanently open, closing it only in emergencies. This adjustmenteliminated rapid temperature and pressure fluctuations. In addition, steam temperature control and injection were optimised, improving steam quality and system stability.
Measurable Performance Improvements
Alan Neeson’s team implemented these recommendations in April 2024, leading to remarkable results:
- No further water hammer events
- Improved control and system stability
- No additional equipment damage
- Reduced losses and enhanced efficiency
These changes resulted in a 1.5% increase in net efficiency, with electricity exports per tonne of waste improving by 0.45 MWs. Electricity generation increased by 4-6 MWs per hour, and the cost of implementation was recouped within a month. By the end of 2024, Cory Group had generated 30,000 additional MWhs, achieving operational targets while improving efficiency.
Eliminating water hammer also allowed the generator to reach its maximum designed electrical output, something it had not achieved for years. The success of this project is now influencing the design of Riverside 2, an expansion currently under construction.
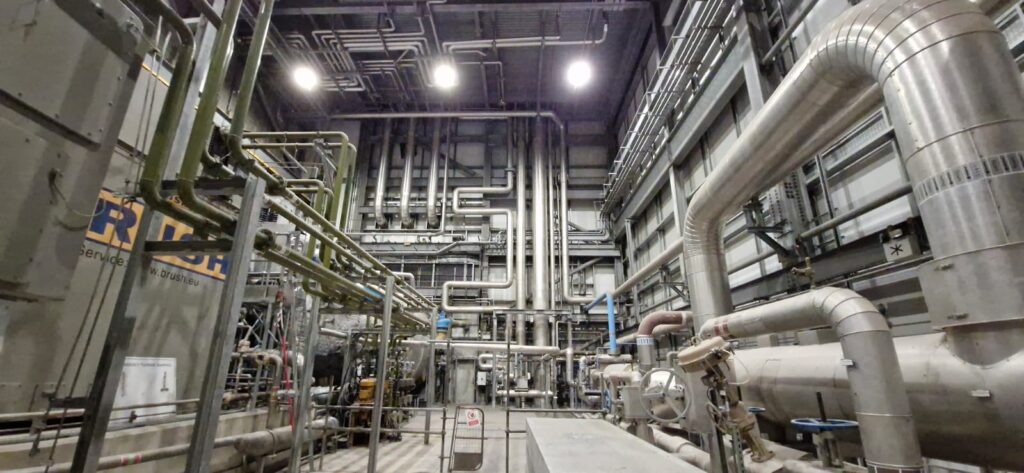
The Value of IMI Insyt
Beyond financial benefits, IMI Insyt provides data-driven insights to support critical operational decisions. With the power generation sector facing challenges in recruiting engineers skilled in diagnosing flow control issues, IMI Insyt is proving to be an invaluable resource.
Alan Neeson praised the collaborative approach of IMI and GPEC Ltd., highlighting their responsiveness and problem-solving expertise. He noted that their proactive support played a key role in the project’s success.