What is a control valve?
A control valve is a mechanical device used to regulate the flow of fluids, whether liquids, gases, or steam, within a piping system. These valves allow adjustment of the flow rate, pressure, and temperature of the fluid, ensuring precise process control. Their operation is based on modifying the opening of the fluid passage using a movable element, which can be a disc, a ball, a diaphragm, among others.
Control valves are essential in applications where a quick and precise response to changes in system conditions is required, such as in chemical plants, refineries, and heating and cooling systems.
Main types of control valves: most common models today
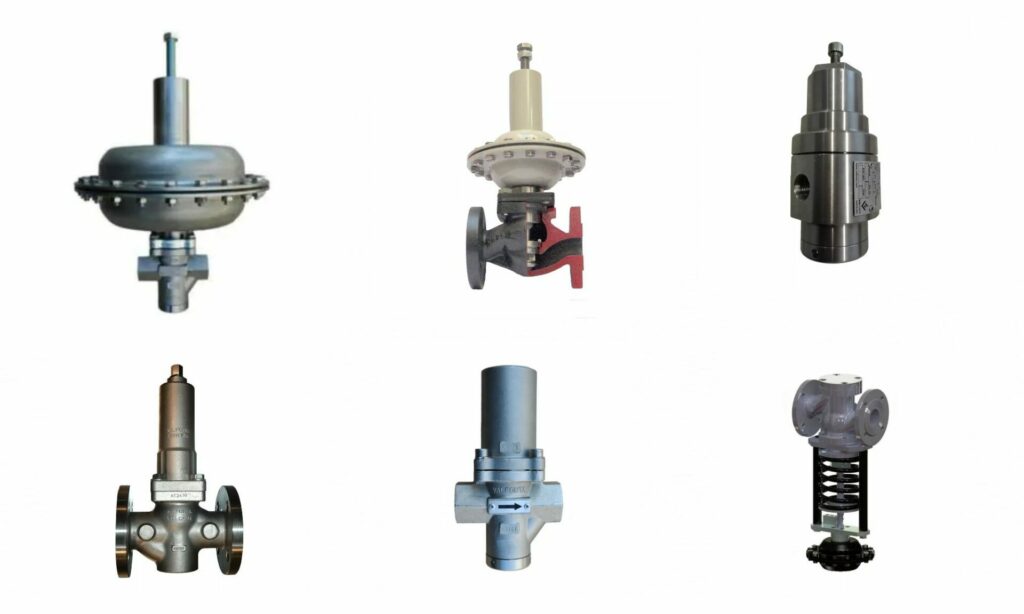
- Globe control valves
Globe control valves are a popular choice due to their simple design and ability to provide precise flow control.
These valves feature a movable disc that sits on a fixed orifice, allowing for the adjustment of the amount of fluid passing through the valve. They are ideal for high-pressure and high-temperature applications and are common in the oil and gas industry, as well as in steam systems. - Butterfly control valves
Butterfly valves are known for their compact design and ease of operation. They use a disc that rotates on a central axis within the valve body to regulate flow.
This type of valve is ideal for applications where quick and frequent flow control is required, and is commonly used in HVAC systems and water treatment. - Ball control valves
Ball control valves are known for their ability to provide tight sealing and ease of operation. They use a perforated ball that rotates within the valve body to control flow.
They are suitable for applications requiring low-pressure drop and precise flow control, and are often found in high-pressure and high-temperature systems, as well as in oil and gas applications. - Diaphragm control valves
These valves use a flexible diaphragm to regulate flow and are ideal for applications requiring precise and leak-free control.
They are particularly useful in systems handling corrosive or high-purity fluids, such as in the pharmaceutical and food industries. Their design allows for easy maintenance and long service life. - Needle control valves
Needle valves are known for their ability to provide very precise flow control due to their thin stem design. They are ideal for low-flow, high-precision applications, such as in laboratories and dosing systems.
These valves allow for fine adjustments in flow rate, making them suitable for applications requiring meticulous control. - Three-way control valves
Three-way valves allow flow control in two different directions and are commonly used in blending or diverting applications.
They are ideal for systems that require flexibility in flow direction, such as in heating and cooling systems, where it’s necessary to divert or blend fluids to maintain optimal operating conditions.
Recommendations for selecting control valves
- Evaluate the specific application
Selecting the right control valve largely depends on the specific application. It’s essential to understand the fluid characteristics (liquid, gas, or steam) and the operating conditions of the system, such as pressure, temperature, and flow rate. This ensures that the chosen valve can effectively handle the fluid and process conditions. - Consider operating conditions
It is essential to evaluate the operating conditions of the system, including maximum pressure, temperature, and the potential corrosives of the fluid. Valfonta offers valves designed to operate safely and efficiently under a wide range of conditions, ensuring optimal performance and long service life. - Opting for automatic actuators for greater precision
For applications requiring dynamic and precise control, using valves with automatic actuators is recommended. These devices allow adjusting the valve position in response to control signals, enhancing system precision and efficiency.
Valfonta offers various automatic actuators that can be easily integrated into existing control systems. - Maintenance and ease of operation
Control valves should be easy to maintain to minimize downtime and operational expenses.
Valfonta designs valves that are not only efficient in operation, but also easy to maintain and repair. This is crucial to ensure continuous performance and minimize impact on production.
To finish with, I want to be clear. Control valves are essential components in fluid system’s management, and choosing the right type is crucial to ensure efficiency and safety in these systems.
Nowadays, the market offers a wide range of high-quality solutions, including our pneumatic actuator control valve, which combines precision, reliability, and ease of maintenance.
By considering key factors in control valve selection, users can ensure optimal performance and extend the lifespan of their systems.