Water injection pump recycle valves
These valves can pose several challenges and result in multiple issues if not properly specified. They are used to recycle or re-circulate the flow from the water injection pump during startup or when there is no forward demand to maintain the minimum flow required by the pump to prevent overheating. They dissipate the pressure generated by the pump and recirculate low-pressure flow either back to the inlet or, in some cases, dump the water overboard.
The obvious application challenge these valves face is the high-pressure drop, along with ensuring cavitation is eliminated under all operating conditions. Through its Blakeborough Control and Choke Valves with X-Stream trim, Trillium offers an ideal solution for this application, providing up to 30 stages of pressure drop to fully eliminate cavitation and ensure the trim exit velocity is maintained to acceptable levels to avoid associated issues such as vibration or erosion.
The material of the X-Stream trim would generally be Inconel 718, which is suitable for clean water, but on occasion, the injection water can contain sand. This brings with it additional challenges in terms of erosion and potential blockage. Trillium has developed a variant of the X-Stream disc stack for such situations manufactured in solid Tungsten Carbide to prevent erosion and features enlarged flow passages, which provide the ideal solution in conjunction with the X-Stream’s natural anti-clogging flow path.
Another critical function of the water injection pump recycle valve is to ensure tight shut-off. As the valve will spend most of its operational life closed against the full head of pressure from the pump discharge with atmospheric pressure downstream, any leakage past the plug and seat will be erosive. Also, leakage is wasted energy as the pump must make up for this flow. Blakeborough offers this type of valve in both globe and angle configurations, in cast and forged materials compliant with ASME B16.34 or API6A design specifications.
Overboard dump valves
As the name suggests, overboard dump valves are typically used to control the flow of water being dumped overboard on offshore installations. Process conditions that would be innocuous on standard applications become severe when applied to overboard dump valves. Often, users fail to realize the criticality of the application, which results in valves being incorrectly specified, ultimately leading to vibration, erosion, and failure. Historically, many overboard dump valves would have been specified as butterfly valves, sometimes with an additional baffle plate, on relatively low-pressure systems; however, due to the unique set of conditions experienced on overboard dump applications, the use of butterfly valves has proved problematic, largely due to the onset of cavitation in the valves.
One of the main issues with sizing and selecting the right valve for the application is having the right process conditions from the project’s outset. When sizing an overboard dump valve, invariably, there will be a high-pressure condition upstream of the valve, sometimes more than 200 bar. When selecting the valve trim, the all-important condition is the valve outlet pressure. Process engineers do not expect to have a vacuum at the valve outlet, but often, as the water is dumped overboard, a vacuum is generated at the valve outlet, causing the valve outlet pressure to be lower than expected. This, in turn, is likely to generate cavitation. If the correct process conditions are specified, Trillium Flow Technologies can help customers install the correct valves to eliminate this cavitation risk; the x-stream trim, for example, is designed for these severe service conditions.
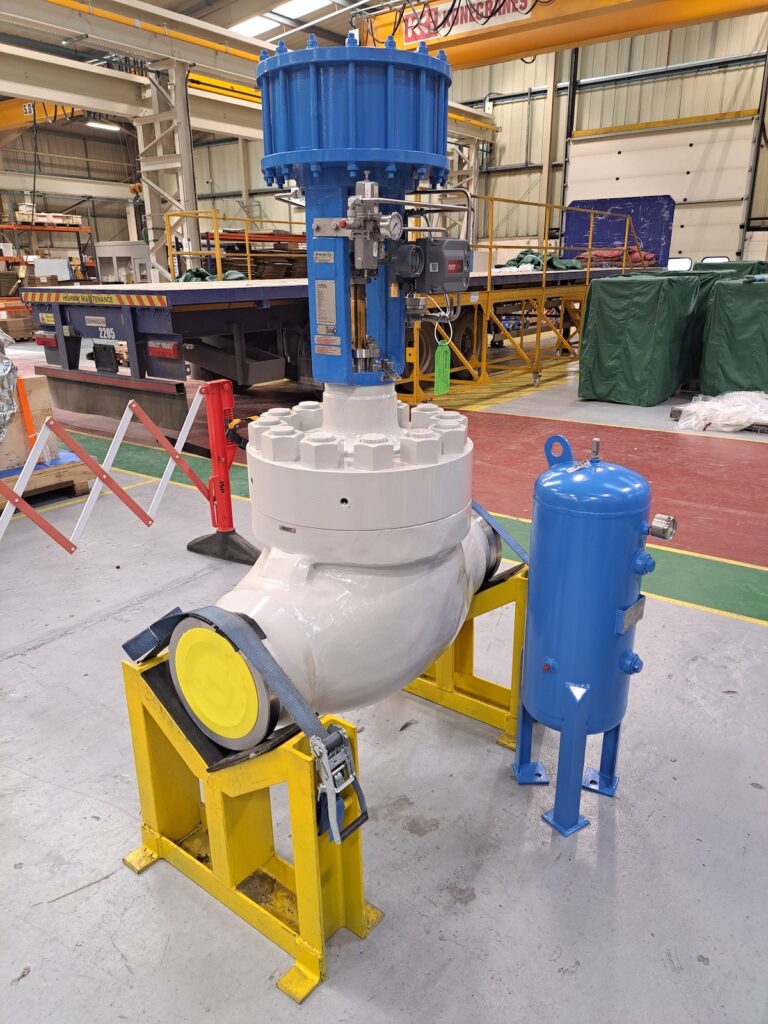
Product Range
Aside from its Blakeborough control and choke valve range, Trillium offers a range of non-commodity and fast-track delivery solutions for offshore applications through its Red Point brand. They include ball, gate, globe, check, double block, and bleed valves with compact designs for tight spaces or the API 6A monogram for wellhead and other applications. For a customer who was looking for a 3-way ball valve to divert an incoming flow of 120m³ evenly between two outlets for an FPSO project, Red Point showcased its expertise by proposing a 3-way globe valve instead for a more accurate flow diversion, also designing an adjustable lock on the stem to accommodate for possible changes in flow conditions. The valve was developed via CFD software and underwent physical flow tests to demonstrate its functionality and efficiency before installation.
Thanks to its flow control expertise, Trillium Flow Technologies can offer guidance on specifying the correct valve for your water injection pump recycle application.