You’re sure to be familiar with the headlines pitting ultrasonic level measurement devices against open air radar transmitters in a whole host of environmental applications.
We all love a good instrumentation showdown: are you Team Radar or Team Ultrasonics?
But for process technicians day in and day out, a one-technology-fits-all approach is simply unrealistic. Both technologies are absolutely stellar in some applications and not-so-great in others: the wise are the ones who know when to use which technology without getting lost in the hype.
Managing outdoor conditions
Wastewater treatment instrumentation deals with the realities of the outdoors, year after year.
Some cite wind and rain as conditions that give ultrasonics a hard time—in the case of wind, reducing the amplitude of the return echo signal by a small amount. Which is true, to a certain extent: radar frequencies being what they are, the technology is unaffected by wind.
But that’s not the full story. In fact, rain will actually have a similar effect on both ultrasonics and radar—however, this effect is insignificant over the short distances involved in environmental applications like open channels.
The same is true on very windy days— the speed of sound will change insignificantly, but for these water and wastewater applications, ultrasonic technology has significantly more signal than what is required for typical ranges found in the environment applications.
In fact, in the UK, where both wind and rain are a regular reality, Siemens ultrasonic systems have been certified to meet the highest accuracy class for open channel measurement (OCM). To date, these are the only products to meet these accuracy standards.
Consideration of distances
With measuring ranges up to 100 meters, high-frequency radar transmitters can outpace ultrasonics in tall silos.
Tall silos which, well, don’t really exist in most environmental applications. With most wastewater facilities’ tanks maxing out at around 10 to 15 meters, radar’s distance prowess is simply not needed.
In fact, for applications like wet wells, the problem isn’t likely to be that water is too far away from the measurement device, but too close.
With storm events dumping major amounts of rain in a short period of time, flooding is a reality for many wastewater treatment plants. When water submerges a radar device, it typically will show a loss of echo or high level, leaving plant technicians to guess whether the device itself is malfunctioning or if the problem is being caused by flooding conditions.
The SITRANS LR100 series radar transmitters for level measurement will measure right to the sensor’s face—and, if submerged, will lock on to a reading near the 100 percent level reading.
We don’t recommend submerging any sensor, though, and suggest optional submergence/anti-fouling shields. Over time, submerging sensors will cause a buildup of debris, thereby decreasing a device’s signal strength. Use of this inexpensive submergence/anti-fouling shield, even when the transducer or radar device is submerged, will keep pumps running and ensure the sensor face does not build up with debris.
For radar, setting the pumping set points below the shield level will ensure the pumps are activated and continue operating in submerged conditions while the sensor face is protected from debris buildup.
Knowing an installation’s full requirements
Compared to a rather simple ultrasonic transducer, sure—that radar transmitter has a lot going on under its housing. All radar transmitters depend on sensitive electronics, whereas ultrasonic transducers are electro-mechanical with no sensitive electronics.
In harsh mechanical and environmental applications, though, do you necessarily want those sophisticated electronics exposed to nasty process conditions?
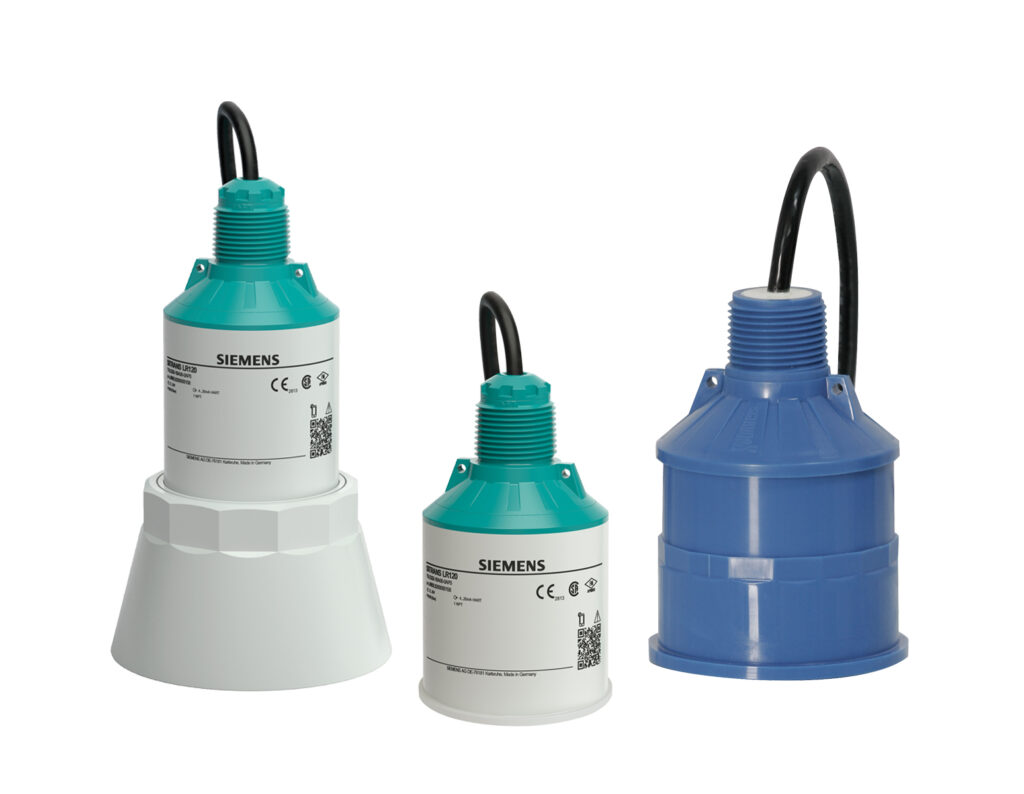
Ultrasonic transducers, as well as the new SITRANS LR100 series radar transmitters, are fully sealed, isolating their electronics from vapor and ingress. And in the case of the ultrasonic systems, the highly intelligent controller can be installed away from the dirty, confined space of a wet well, for example, in a controlled and easily accessible area, leaving the robust transducer to deal with the harsh environment.
Talking about sophistication, however: in the UK, devices are classified within MCERTS to different levels —Class 1 being able to manage the highest accuracy. Siemens is one of the few instrumentation companies that has a Class 1-rated level device, and it is an ultrasonic system. No radar to date has achieved Class 1.
Why the difference in accuracy? The reason is due to changing ambient temperatures within which the devices must operate. Siemens transducers don’t have electronics in the ambient environment that are affected by temperature changes common in OCM applications: an external temperature sensor compensate the change in the speed of sound caused by temperature fluctuations.
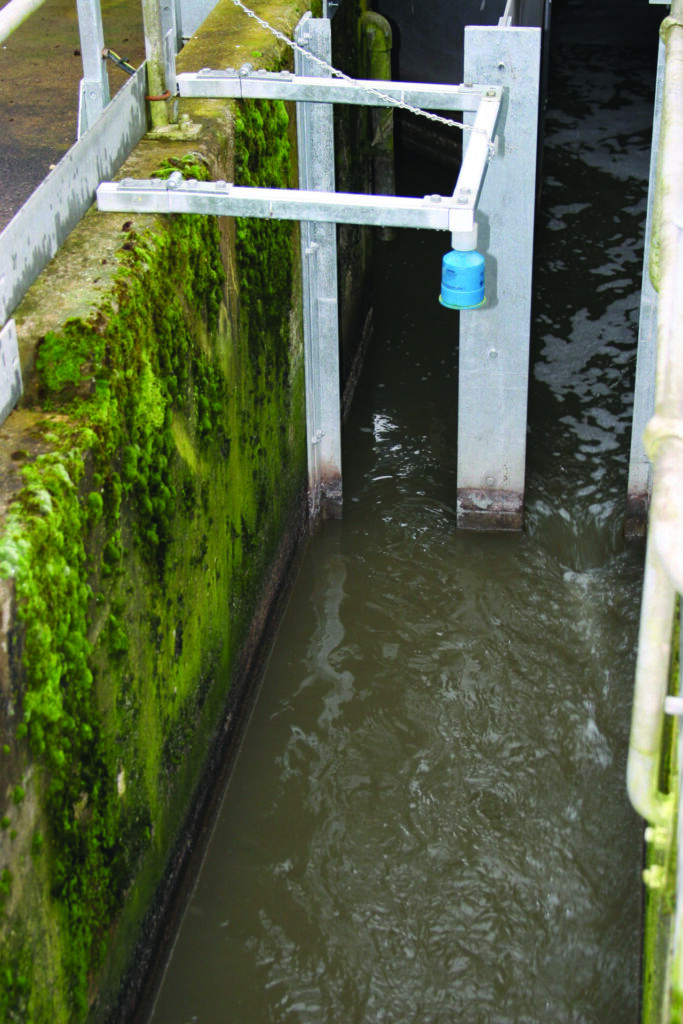
Radar, on the other hand, depends completely on electronics in the environment—and their characteristics change based on the ambient temperature. So, while the measuring media temperature does not impact the reading, accuracy will depend on how stable the environmental temperature is. This characteristic has and will continue to challenge radar in its quest to meet the high accuracy requirements of MCERTS Class 1.
Total cost of ownership
With the introduction of radar transmitters built for the purpose of the environmental and general industries, the cost gap to ultrasonic solutions has closed significantly. In general, though, radar is still slightly more expensive compared to ultrasonic solutions for similar applications.
Of course, low purchase price is not the full answer: total cost of ownership is. Diagnostics, communications, self-cleaning, and robustness over a device’s lifetime all come into play and should all be considered when choosing instrumentation.
Challenges from buildup and foam
In dirty outdoor applications in the pre-treatment stages of a wastewater facility—or anywhere buildup is an issue—ultrasonic transducers shine with their self-cleaning faces, which literally shake themselves clean of dirt and buildup in your application.
Combined with intelligent echo processing software, ultrasonic level devices ensure that dirty process conditions don’t affect measurement performance.
SITRANS LR100 series radar can also deal with significant buildup thanks to its incredibly sensitive radar chip—better than any previous radar in its class. As discussed previously, we recommend for long-term performance that radar not be subjected to submergence to prevent buildup, which will ultimately affect signal strength.
And with foam, radar is neither better nor worse—while wet foam will reflect signals, dry foam will absorb both ultrasonic and radar signals.
Level measurement freedom of choice
Ultrasonic
- High accuracy OCM
- Traditional environmental applications
- Areas with severe mechanical conditions such as vibrations or impact.
- Self-cleaning sensor
- Transmitter with logging
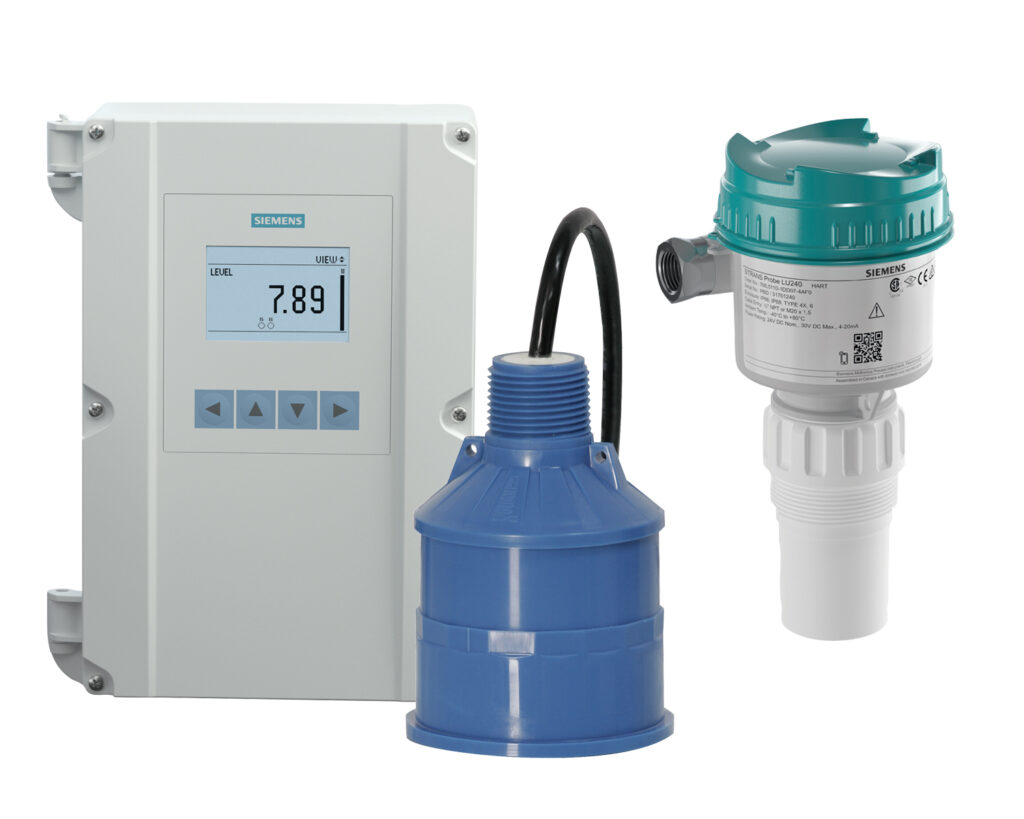
Compact radar
- Remote battery operations
- Measuring solids to 30 m
- Non-intrusive measurement on plastic tanks
- Strong vaporous liquids
- Applications with vacuum conditions
- CO2 environments
- Compact transmitters with Modbus RTU
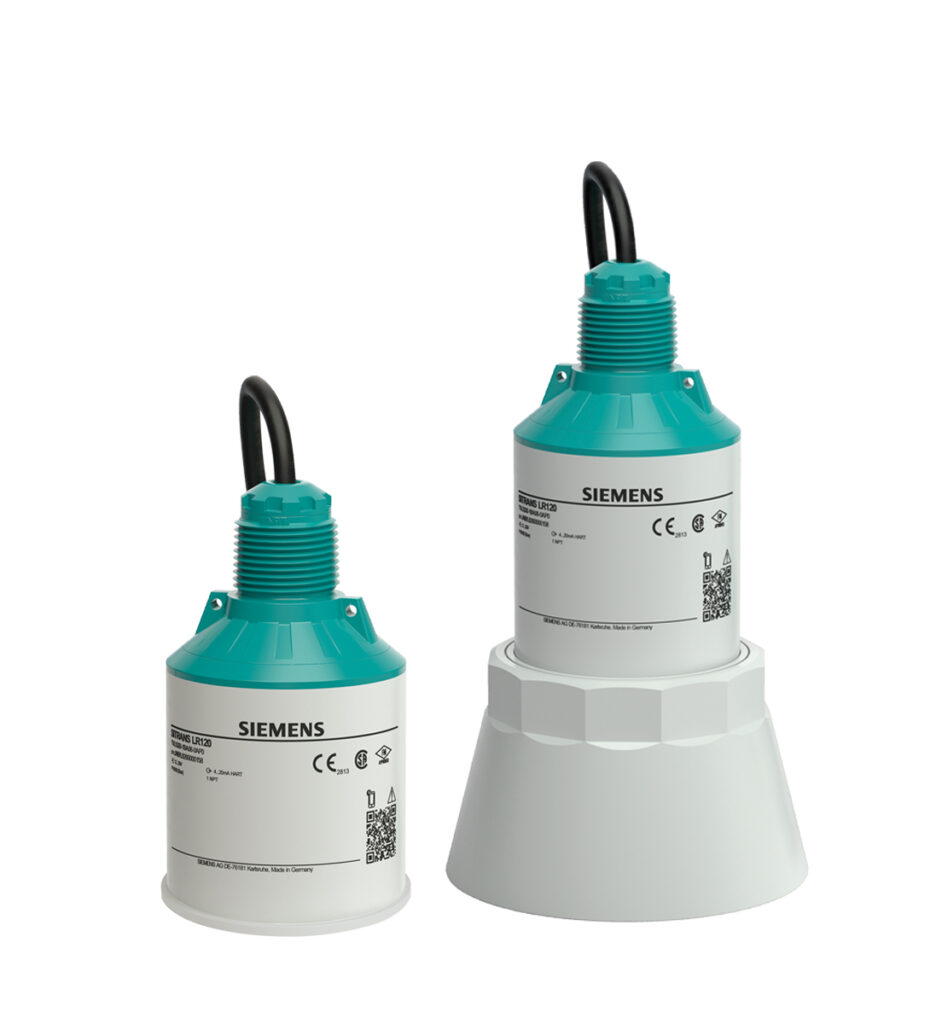
From power usage to challenging conditions
In remote areas when battery life is critical, some radar devices will conserve power usage much more effectively than ultrasonic technology. With a start-up of fewer than ten seconds at 3.6 mA, SITRANS LR100 series radar transmitters are able to maximize remote battery life. The result? This lower start-up power consumption means more than twice the efficiency of both ultrasonic transmitters and other radar devices currently on the market.
And in challenging process conditions, radar is rarely impacted. Vapor, temperature gradients in a vessel, dust, and vacuum conditions—radar is likely the best choice: for example, with digesters where the atmosphere is CO2. Or in lime silos where filling will cause significant dust—again, radar’s 80 GHz frequency is the answer.
Radar devices can also monitor through plastics, which means accurate, non-intrusive level measurement of aggressive chemicals in plastic vessels.
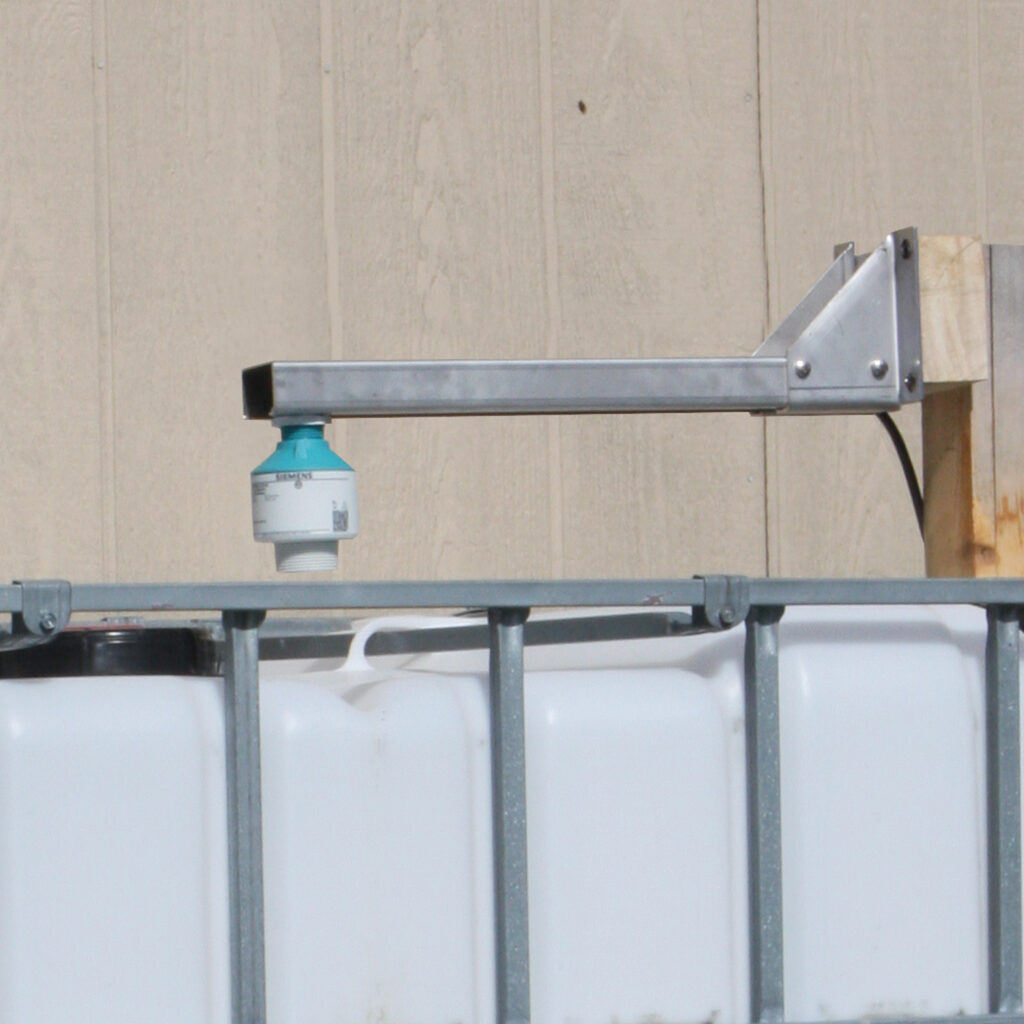
Seeing through the hype
At the end of the day, a one-device suits-all approach to level measurement is simply not a wise idea in any industry.
Whether it’s a result of an instrumentation company’s limited portfolio or hyped-up marketing for a shiny new device, a single technology approach is confusing to customers and a source of misinformation in the industry.
Ultrasonic level has been a critical partner in the environmental industry for the past 40 years—for all of the reasons described above. And these devices are still going strong across the globe, decades after installation.
That being said, ultrasonics may not be the perfect choice in every application. So why not choose a purpose-built radar transmitter like the SITRANS LR100 series, rather than radar originally designed for process industries that is now being shoehorned into environmental applications?
It is here that a supplier’s complete level portfolio is essential.
At the end of the day, you want a provider with leading technology solutions for a wide range of level— including radar, ultrasonics, pressure, and more—to ensure you are given the choice of selecting the best instrument for your application.