Laser level measurement provides an easy way to get precise, reliable silo level measurement. Why use laser level measurement? Because of the simplicity of its use, which translates into low cost of operations. Laser beams move through space with very little divergence. They remain tightly focused even at long distances. Since the laser beam doesn’t interact with the surrounding environment, there is no need to cancel false echoes. Only the liquid or solid surface is detected, and therefore commissioning is simpler. Also, changes in the environment do not require changes in sensor parameters. Material accumulation on the side of a vessel will change over time, requiring a remapping of false echoes. The same would happen if the sensor is moved. This is not required with laser level measurement. Therefore, it leads to more reliability and more up-time during use.
Laser beams also bounce back from surfaces very differently from ultrasonic or radar waves, which can be advantageous in several applications. Plastics, polymers, and low density materials are easily detected by laser sensors, as opposed to radar sensors. Also, there is no limitation on the angle of incidence for measuring solids with lasers, which simplifies installation.
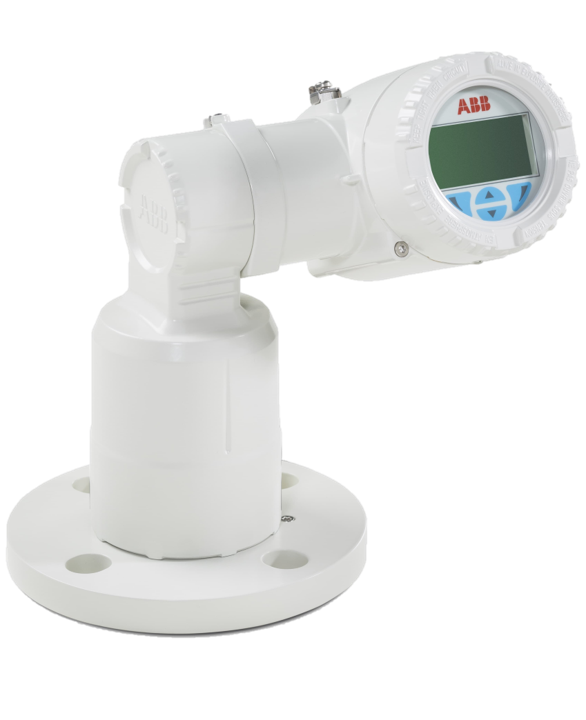
Being very narrow, the laser beam can also be used in tight spaces. The LLT100 laser beam will grow to 2” after traveling a distance of 20’. This allows the measurement to be made in several difficult applications such as measuring through pipes and valves, grids, and also in the presentce of agitators and mixers, where the laser beam can be sent between the edge of the agitator and the vessel side to measure without interference.
Laser level measurement is used in many types of silo level measurement applications. For instance in agriculture it performs well on many types of grains such as corn or wheat. For wood products, the ability to measure in the presence of wall buildup greatly reduces maintenance cost, as the measurement is insensitive to buildup. For plastic pellets, widely used for making plastic objects, laser level provides an easy solution since it can measure plastics which is difficult for radar-based sensors. Lasers are also used in several aggregate materials silo level applications.
In conclusion, lasers will change the way you see level measurement. It will simplify operations and allow non-contact measurement in applications where non-contact was not possible up to now. By using new technology applied to industrial level measurement, laser level makes measurement easy.