Importance of Level Measurement for Liquid Management
In liquid processing, precise level measurement plays a key role. It ensures optimal utilisation of tanks, prevents overfilling or dry running, and enhances process safety. From aggressive chemicals and foaming liquids to interface layers, measurement technology must meet diverse requirements, demanding robust and highly accurate sensors. Inaccurate measurements can lead to production downtime, material losses, and high costs.
Precision for Liquid Applications
UWT offers specialised solutions for point and continuous level measurement, as well as interface detection in liquids. The sensors are designed to meet a wide range of requirements and provide reliable results, even in challenging applications.
Point and Limit Level Measurement
Capanivo® sensors from UWT provide highly precise limit level detection in liquids. These capacitive sensors are ideal for detecting minimum and maximum levels in tanks and containers, even in foaming or viscous media. Their robust design and IP68 protection rating ensure long service life and reliability.
The newly developed Vibranivo® vibration liquid fork provides a compact and reliable solution for point and limit level measurement in liquids. Its robust 316L stainless steel housing with IP69 makes it ideal for hygiene-sensitive applications. Resistant to build-up, flow, and air bubbles, it delivers precise measurement results. Its bright, colour-selectable signal LED ensures clear status indication.
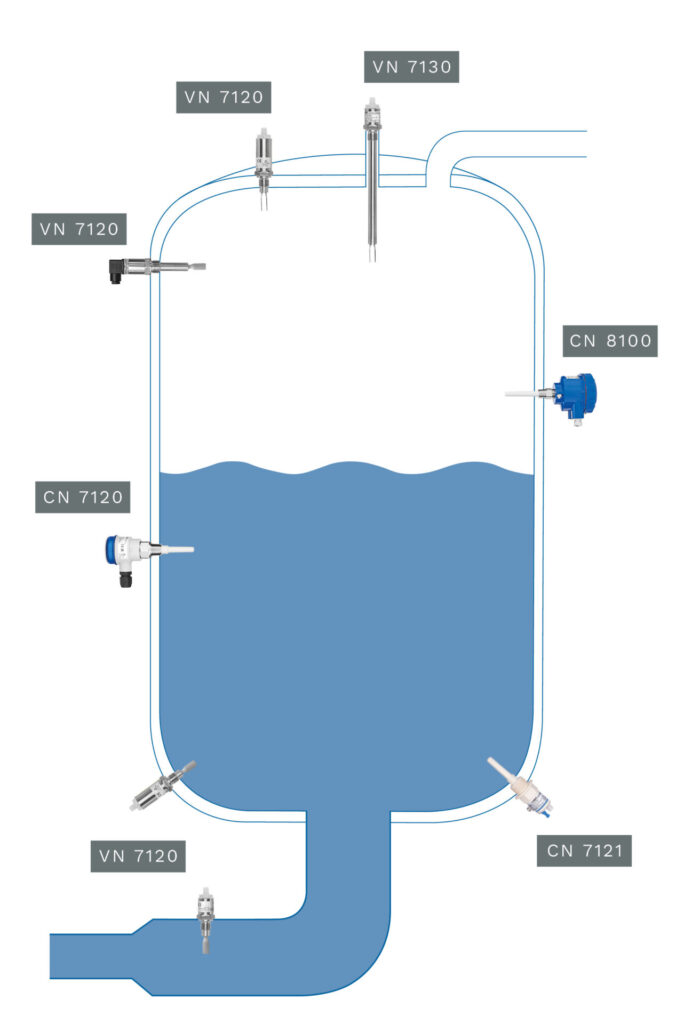
Continuous Level Measurement
For the continuous monitoring of liquids, UWT relies on radar and guided microwave technology. The sensors from the NivoRadar® and NivoGuide® series provide precise measurement of liquid levels in tanks – regardless of steam, density changes, or temperature fluctuations. This ensures reliable process control, even in challenging environments.
Interface Measurement
The measurement of interface layers plays a crucial role in the chemical, petrochemical, and water industries, as well as in many other sectors with diverse applications. Specialised sensors such as the Capanivo® CN7, the NivoCapa® series, and the RFnivo® can accurately detect phase separations in tanks, enhancing process efficiency and safety. UWT provides high-sensitivity and precision solutions that deliver stable measurements, even under extreme conditions.
Success Story: Optimised Level and Foam Detection in the Pulp Industry
An application example from the primary pulp industry demonstrates the efficiency of UWT sensors. A large pulp and paper mill required a reliable solution to detect foam in the discharge area of a pulp processing operation. Foam formation was caused by movement and the chemical composition of the pulp. At the same time, the water from the spray system of a 10-metre-high tank needed to be disregarded.
As retrofitting sensors in existing concrete tanks is challenging, a solution was developed that allowed for top-mounted sensor installation. For safety reasons, the customer decided not to use the full capacity of the tank. Two sensors with cable extensions were installed from the tank ceiling: one measuring at a 7-metre fill level and another at 5 metres. Due to the chemical reagents used in the paper production process, the Capanivo® CN7 was chosen, as its probe is chemically resistant.
The CN7 features inverse frequency shift technology, enabling the reliable detection of foam layers – even when active media jets are used for foam reduction. Additionally, the sensor is WHG-certified, meeting the requirements for overfill protection.
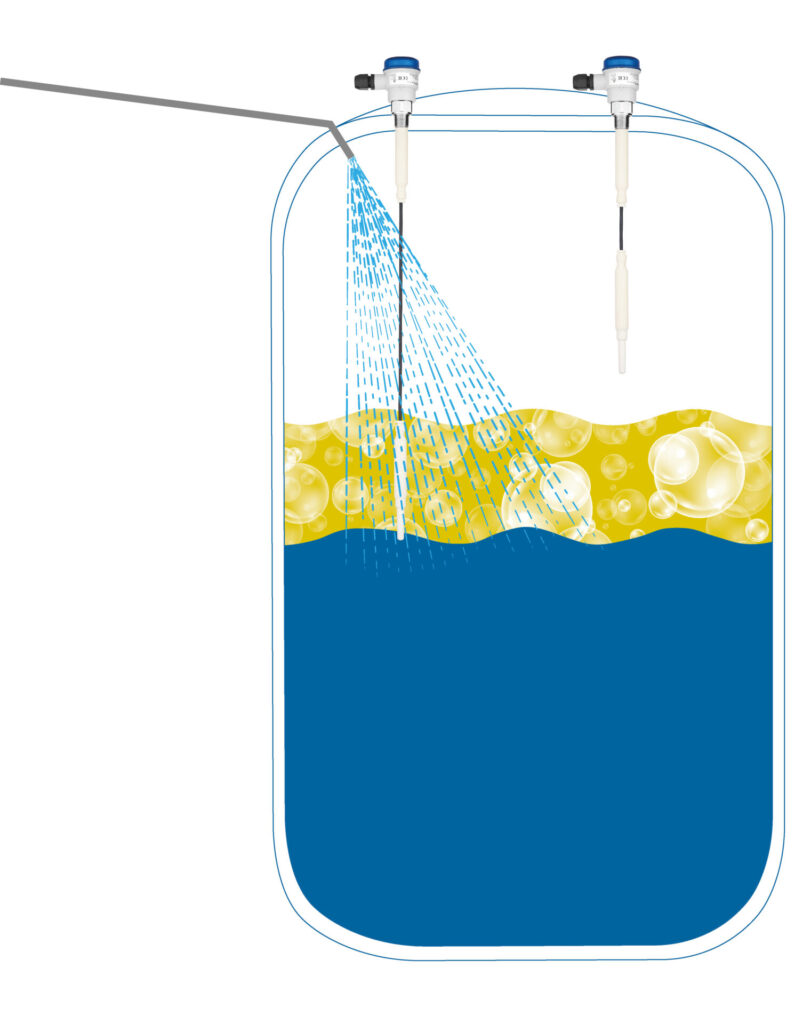
Technological Advantages of the UWT Capanivo®
High measurement accuracy: Precise detection of liquid levels and foams, even in materials with low dielectric constants.
Process safety: Prevention of overfilling, material losses, and production downtime.
Robust design: Suitable for extreme temperatures, pressure, and aggressive media.
Easy integration: Plug & Play solutions, compatible with existing automation systems.
User-friendly sensitivity adjustment: Quick and precise sensor sensitivity calibration – directly on the device via potentiometer.
Industry 4.0: Smart sensors for integration into digital networks and cloud systems.
Future Viability and Sustainability
UWT sensors deliver precise measurements and promote sustainable resource utilisation by minimising material losses and optimising process efficiency. Accurate level control reduces material waste and energy consumption, ensuring smooth and efficient operations. Thanks to their low-maintenance design, process downtimes are minimal, leading to enhanced plant availability. Additionally, the durable sensors help to reduce the environmental footprint of facilities.
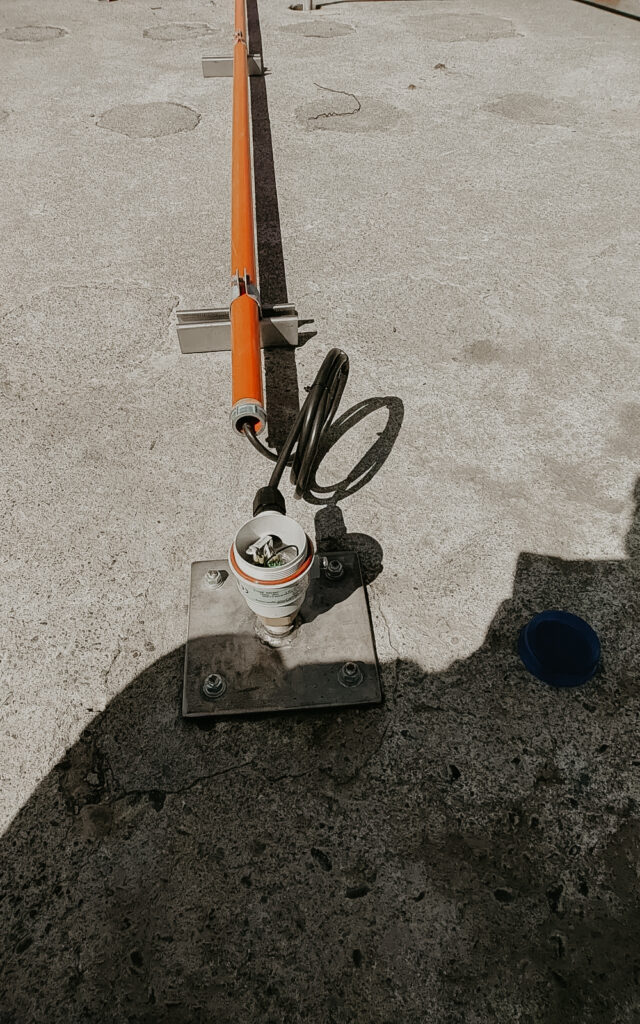
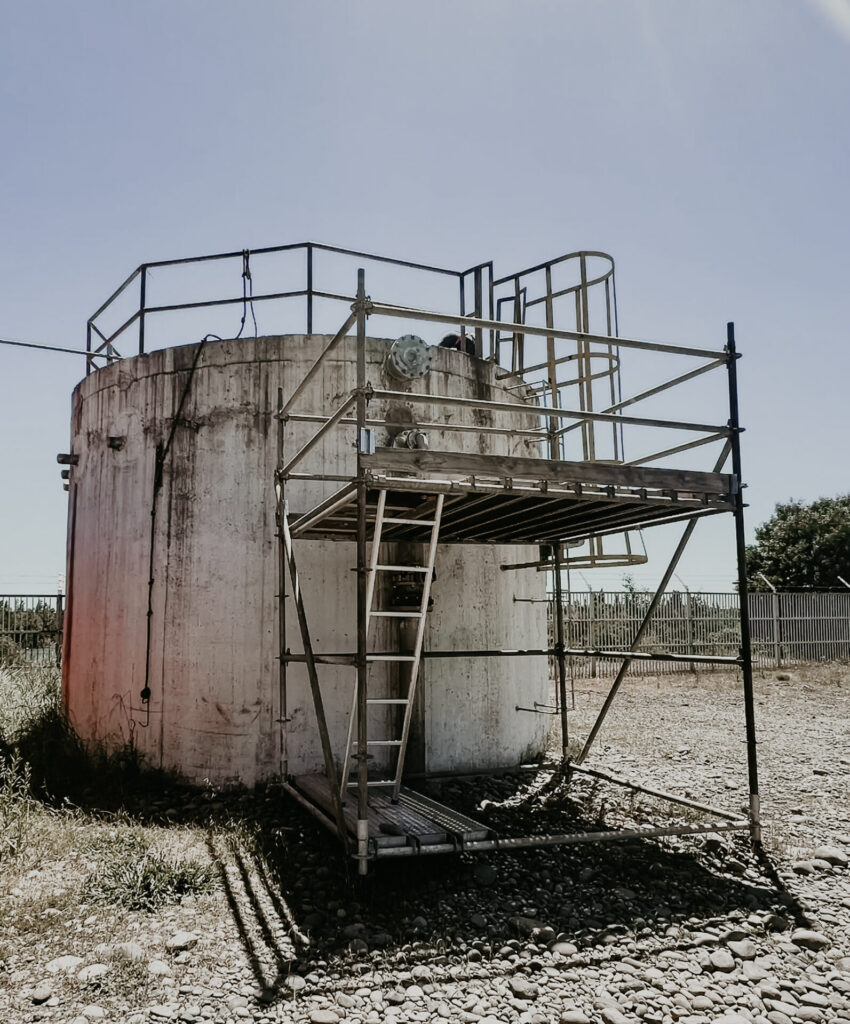
UWT as a Strong Partner for the Process Industry
With over 45 years of experience, extensive industry knowledge, and a global network, UWT provides innovative and reliable solutions for level measurement in the process industry. In addition to proven standard solutions, UWT is also known for customised special solutions, where specifically designed sensors are individually tailored to specialised applications. Furthermore, UWT offers bespoke solutions for the detection and monitoring of bulk solids, meeting the specific requirements of a wide range of industries. Only with this expertise is it possible to select the most suitable sensors for each unique application. Our sensors deliver precise results and ensure safe process control – even under the most demanding conditions.