Problem:
Frequent clogging — caused by fats, oils, greases (FOG), and synthetic wipes—led to regular pump failures and significant downtime, resulting in maintenance costs, exceeding $3,000 per month. This was primarily due to repairs and the need for chemical injections to address FOG buildup.
The consequences of these failures extended beyond financial strain. Risk of sewer overflow into the kitchen areas posed serious health hazards, while repeated incidents created unpleasant odors & hazardous gases, necessitating the evacuation of facilities for maintenance.
These challenges highlighted the inefficiencies of the existing system, prompting the university to upgrade to the OverWatch® Direct In-Line Pumpto effectively resolve these ongoing problems.
OverWatch® Direct In-Line Pump System by Industrial Flow Solutions is a breakthrough technology designed to lift influent from the point of entry, eliminating the wet well. Influent is contained, eliminating odors, and reducing maintenance. The stainless-steel body is designed to withstand the effects of corrosion from harsh materials and solutions, making OverWatch® an ideal solution for the Municipal, Industrial and Commercial industries.
Solution:
To address the persistent issues with the wastewater management system, the university implemented the OverWatch® Direct In-Line Pump System. This upgrade was executed swiftly, with installation completed in a single day to minimize system downtime and disruption.
The new system effectively contained effluent waste within the piping for improved safety and comfort reducing hazards, odors, & harmful gases. Enhanced monitoring capabilities for motor function allowed for proactive detection of clogs, leading to a substantial decrease in pump failures. As a result, the need for chemical injections to manage FOG buildup was entirely eliminated, streamlining maintenance efforts.
Furthermore, grease trap maintenance was relocated outside the building, preventing the accumulation of solidified grease at the pump station. This comprehensive solution significantly improved operational efficiency of the university’s facilities.
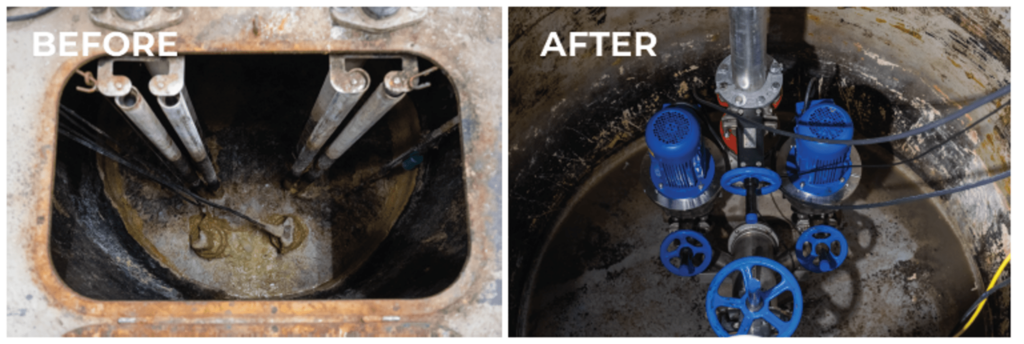