Background
Gas Chromatography (GC) is a laboratory process that separates a gas mixture into component parts that can be analyzed and measured. Analytical laboratories have relied on GC for many decades. Today, the process is used by diverse industries to gain important information such as product quality and purity.
In many GC setups, the effluent from a flow-through chemical reactor is sent to a GC column for analysis at programmed intervals over a period of time. In this situation, it is important to have stable and consistent GC flow control to ensure accuracy.
As shown in the schematic below, reactants are delivered in a continuous flow chemistry format to a reactor where the inlet flow rate is controlled by a mass flow controller (MFC). The reactor may be a packed bed reactor, for example. At the outlet of the reactor, a back pressure regulator (BPR) is installed to maintain a steady pressure on the reactor so that the effluent flow rate is equal to the inlet flow rate set by the MFC.
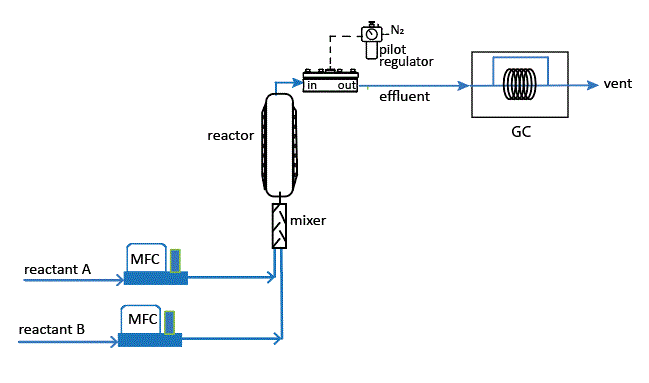
Challenges
Research scientists using a traditional BPR for this type of system sometimes find that the device’s setpoint will fluctuate, delivering an effluent flow rate that is either much higher than inlet flow rate (when pressure has built up above the setpoint) or essentially zero (as pressure is building up to the setpoint). As a result, GC data may not reflect a time-resolved picture of the effluent gas composition due to the high degree of fluctuation caused by the BPR. This can occur even when sampling the effluent at fixed intervals.
Alternative Design
In many GC applications, using a dome-loaded multi-orifice BPR instead of traditional spring-loaded devices offers much improved accuracy. Unlike traditional back pressure regulators, these BPRs use a novel design in which a diaphragm covers a field of parallel orifices located in the body of the regulator. As fluids flow through the unit, the diaphragm lifts off the orifices to release pressure. When flow is minimal, only a portion of one orifice opens to release the pressure. When flow is high, the diaphragm is pushed up to engage all the orifices. This design responds immediately to changing conditions and setpoints; therefore, it is able to maintain a steady pressure at the outlet of the chemical reactor, resulting in excellent flow control to the GC.
Dome-loaded, multi-orifice BPRs such as those offered by Equilibar can be made from an almost infinite combination of materials for extreme process conditions. They are easily automated, can handle a wide flow rate range, and require little maintenance.