Can this be detrimental to the plant’s process? You bet!
Let’s take a closer look at how vibration affects a valve. Today’s digital valve positioners use an electro-mechanical device called a potentiometer or “pot” to detect movement in the valve assembly. This potentiometer, while being electronic, has mechanical components inside called wipers. These wipers move with the valve, while contacting a resistive material. Over time, the “pot” components can be adversely affected by the extreme and repeated vibrations experienced in the valve assembly. The vibration will travel through the potentiometer and prematurely wear these mechanical components. Once this essential component is damaged, you won’t be able to maintain quality electrical contact with the element and you’ll start to experience poor resolution in your valve positioner. This in turn correlates to poor positioning and unpredictable valve control.
How can you maintain high resolution in your valve positioner?
It’s possible to avoid premature potentiometer wear in high vibration applications by removing this component from the valve assembly. Instead, use a non-contact position detection solution like, a magnetic non-contacting sensor (NCS), with your valve positioner. Not only can these magnetic sensors address vibration issues, but they also have the ability to move other essential positioner components away from the valve assembly – this is called remote detection. By moving the electronics away from the valve you can address other issues like unsafe valve locations and temperature concerns.
A non-contact, remote detection application would typically consist of a valve assembly with positioner, cable and magnetic sensor assembly. The magnetic sensor assembly (sensor and magnet) is installed on the valve and connects to the remotely mounted valve positioner (on a pipe or wall) with a cable. The sensor and magnet work together to detect the current valve position and relay the information to the valve positioner. To better explain this giant magnetoresistance (GMR) sensor technology, the magnetic sensor changes its electrical resistance in response to the immediate presence of a magnet. The installed magnet moves with the valve (installed on the actuator stem) allowing the magnetic sensor to detect movement and change its resistance.
Another option is strictly non-contact position detection (not remote). The valve positioner is installed on the valve assembly in a traditional manner; however the potentiometer has been replaced with an internal magnetic sensor assembly. Again, the GMR sensor operates by changing its electrical resistance in response to the presence of the magnet (installed on the actuator stem).
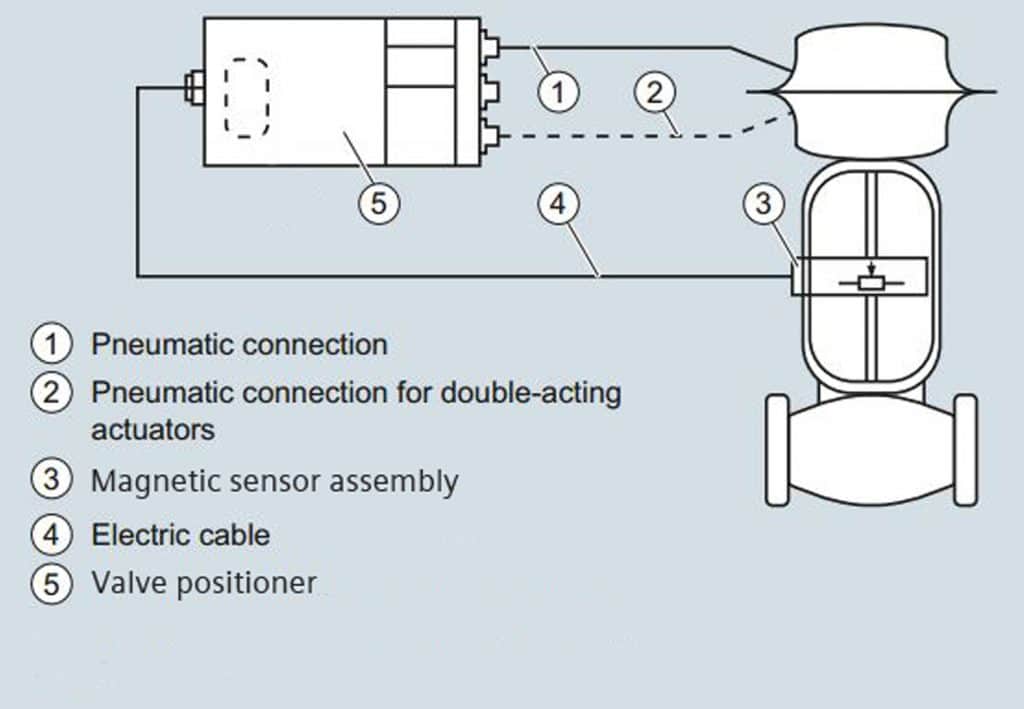
Are there differences between technologies?
It’s important to note not all magnet sensor solutions are the same. Many solutions rely on a physical connection to the actuator stem via a coupler or lever arm. This traditional linkage connection has the potential to drive down the overall cost of maintenance as well as providing a simpler retrofit solution versus the spare parts/assemblies needed for each “linkage-less” style valve positioner. Additionally, there are defined advantages to newer sensor technologies. The Hall Effect sensor is very popular within the valve industry. However, compared to newer technology, like GMR sensors, it has a much lower signal to noise ratio. GMR technology has a high signal-to-noise ratio, meaning it is uniquely suited for these types of valve control applications. GMR sensors have high resolution/sensitivity and temperature stability while having a small footprint and lower power consumption.
In closing, both the non-contact position detection features as well as the remote detection feature address the extreme vibration applications where we see a negative effect on positioner control and its potentiometer. The NCS allows the valve assembly to continue to experience the high vibration that is sometimes unavoidable while maintaining the high resolution and precise control that is desired.
Written By: Sean McNutt, Siemens Product Marketing Manager