When pumps fail, production stops, cooling systems are interrupted, and machines must be stopped. That is why effective pump protection is a crucial task for both plant engineers and technicians. It is particularly important to detect unwanted gas inclusions in fluid media at an early stage. This is remedied with a novel sensor technology detecting gas bubbles before they damage pumps.
Pumps are a key component to ensure consistent process flow where fluids are involved. They can be found virtually everywhere and are used to keep industrial processes moving forward, heat homes, and supply machines with lubricant. To ensure a process runs smoothly, pumps must be prevented from running dry and any cavitation must be identified, as both can lead to damage or failure.
Dry running describes the situation that occurs when gas bubbles get into a pump and cannot be released. This means that there is too little or no fluid in the pump housing. One reason for this may be the improper commissioning of systems with, for example, an empty tank or closed suction pipe. Another may be the improper installation of pumps – if plant engineers do not pay sufficient attention to differences in height, this can lead to pump suction problems in the future.
Possible damage caused by dry running
So what happens when pumps run dry? Depending on how quickly gas is detected in the pipes and on the volume of the gas inclusions, the effects may be more or less severe. At best, components are temporarily overloaded; in the worst-case scenario, the pump is destroyed. Dry running can cause, among other things, the following pump damage:
- Considerable overheating of the bearings
- Leakage due to destroyed sealing
- Loss of performance, pressure loss, increased noise levels
- Stiffness
- Increased energy consumption and labor-intensive maintenance work
- Complete destruction of the pump
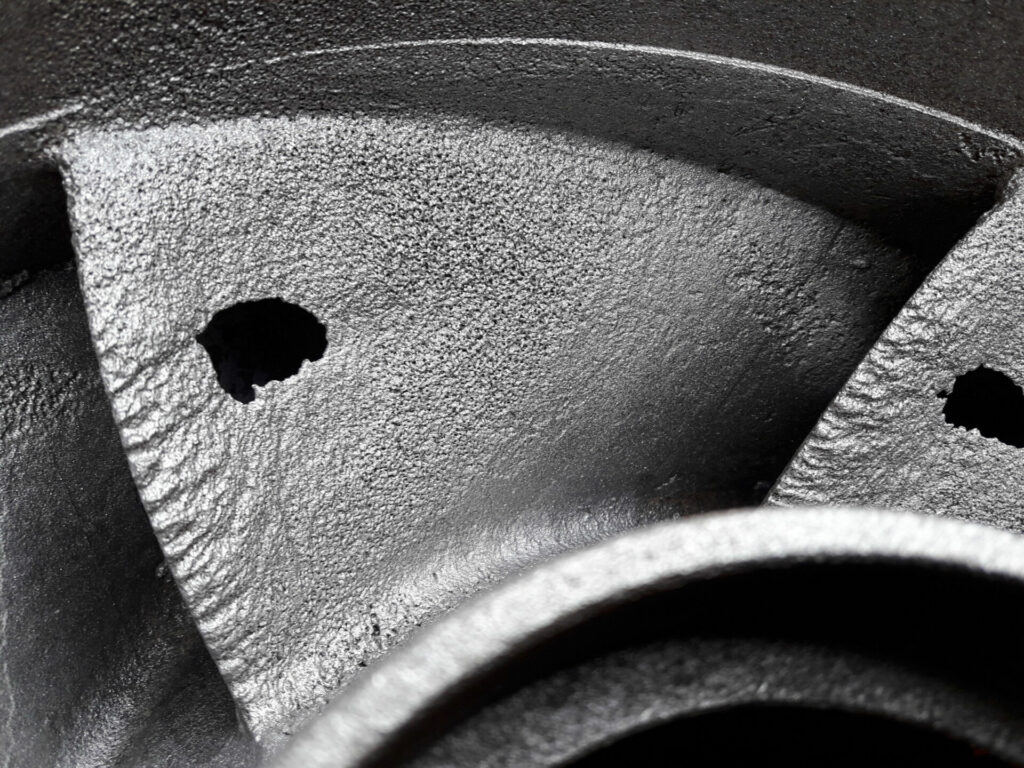
The more complex the system, the greater the likelihood of gas getting into pipes and pumps. Given the damage often associated with downtime and high maintenance costs, it would be ideal to detect gas in the system at an early stage. Reliable gas bubble detection provides the following benefits:
- Increased service life of pumps
- Less maintenance and downtime
- Increased system availability
- Process safety
- Higher product quality
- System effectiveness and process efficiency
- Cost reduction
- Food safety in hygienic applications
How have plant operators protected their pumps from harmful gas bubbles to date? In closed systems not allowing for visual inspection, operators can only guess at the presence of gas bubbles. Pump protection is therefore mostly based on acoustic monitoring – in other words, when an attentive technician hears something unusual.
Novel Baumer sensor detects even the smallest of gas bubbles
To ensure effective pump protection, gas bubbles must be reliably detected before they enter the pump interior. No sensor was able to do this to date. Enter the Baumer PAD20 analysis sensor, which reliably detects even the smallest gas and air bubbles in the medium. Thanks to the smart sensor principle, it will immediately report any individually adjustable limit for gas inclusions being exceeded. The sensor measuring principle is dc-value based detection (dc = dielectric constant) of air and gas bubbles in fluids with a minimum conductivity of dc > 1.5. Thanks to sophisticated algorithms, PAD20 will recognize very precisely any presence of gas and fluid in the flow. The sensor measures independently of the medium, providing maximum flexibility. The “Gas bubbles in the medium” signal can be used to shut down the pump or report an alarm warning.
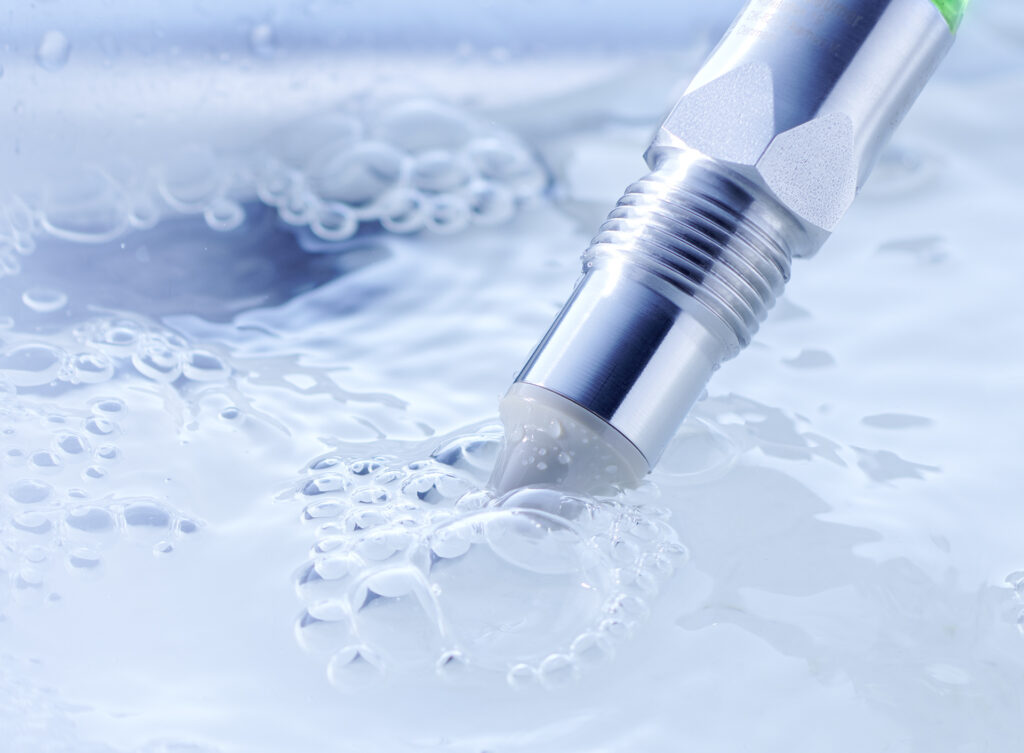
Ideal for heating and cooling systems and the food industry
Wherever fluids are moved in closed systems, the PAD20 can protect pumps from air and gas: in industrial applications, food production, building technology, or water supply. More target applications include monitoring cooling circuits and dry run prevention, process monitoring and ensuring process safety in terms of pump protection. The application is particularly beneficial for the food industry and in heating/cooling systems. In heating systems, a similar phenomenon happens right at home. When there is air in the system, household radiators do not properly heat up and energy is wasted. This is even more true for industrial heating and cooling systems. Gas bubble detection therefore ensures both resource-efficient operation and system effectiveness. Process safety and pump service life are increased, while the maintenance effort is reduced. In industrial applications, functioning pumps are all the more important because downstream processes can also be jeopardized if a failure occurs.
In food production, unwanted gas bubbles in the system are particularly problematic because they can endanger not only the pumps but also food safety. This is because contact with air or gas during processing, filling, or packaging can have a direct impact on the quality of the food produced. In this scenario, early gas detection can reduce waste and increase system efficiency.
PAD20 is particularly suited to protecting centrifugal pumps, gear pumps, and piston pumps.
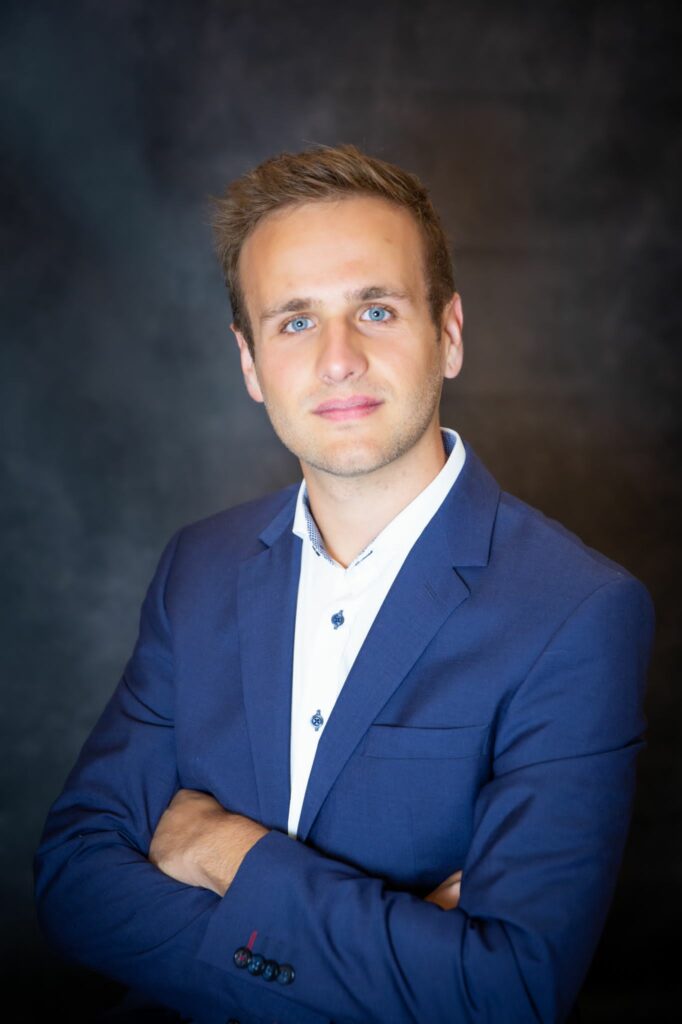
Author:
Julian Budde, Product Manager at Baumer
Baumer GmbH
Pfingstweide 28
61169 Friedberg
Germany