Given the rugged and hazardous conditions in these facilities, you need to determine how MFCs are designed in order to specifically meet (or exceed) applicable standards and classification approvals. Factors to consider include how well it can withstand environmental conditions and how much wear and tear it can take while still retaining precise, stable flow control over its life cycle.
Zones and Classifications
To assess whether an MFC can be safely used in a hazardous environment, it’s necessary to understand key classification standards and labeling to check if the device is right for your needs.
The Zone system, currently used in Europe, Asia and other locations worldwide, has two parts. The Zone specifies the nature of the hazardous material (gas or dust) and the probability of that material’s presence in ignitable concentrations. Zone 0 covers long periods of time, Zone 1 covers materials produced under normal operating conditions and Zone 2 covers gases that are rare and only present for short durations.
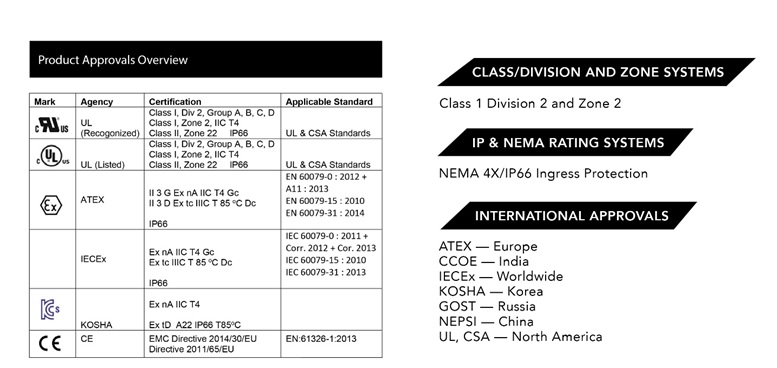
The Zone system also has Groups; these define the type of hazardous material that could be present and (partially) the location: Group I is for mines, Group II covers explosive gas and Group III covers explosive dust. Make sure to specify an MFC engineered for safe operation with Group II explosive gases.
Enclosure Ratings
One critical test assesses the potential for autoignition of volatiles that could result from the heat generated by the MFC’s electronics. Since there are different autoignition temperatures for different gasses, a Class 1 rating for an MFC will include additional information specifying which volatiles the MFC has been tested for.
MFCs for hazardous areas also typically receive IP and NEMA ratings. The IP rating identifies the level of ingress protection provided by an enclosure or housing from both dust and liquids. The NEMA rating, primarily used in the United States, defines the enclosure’s ability to withstand various environmental conditions. For MFC products, the most common classifications are NEMA 4/4x, IP65, IP66 and IP67. For example, IP66-rated MFC housings are dust-tight and protected against heavy water jet spray, which could degrade the housings and potentially allow ingress of explosive gasses or dust that could ignite.
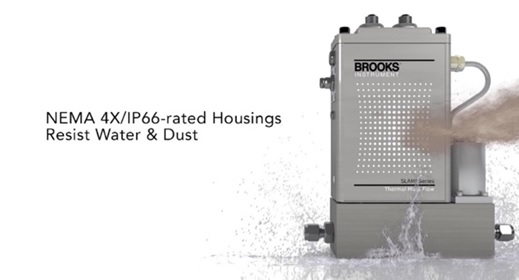
In addition, MFCs with IP66-rated housings are much more rugged and provide longer operating life cycles, even if exposed to wash-down conditions or weather. That makes IP66-rated MFCs reliable devices for use in outdoor process equipment.
Value of Secure Connectors
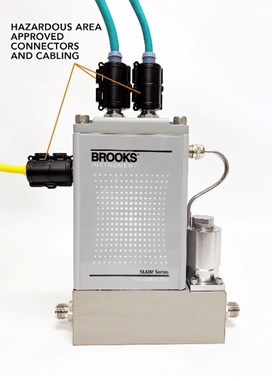
Another critical safety area to consider is the MFC’s electrical and communications connectors. To prevent a momentary electrical discharge that can cause a spark, they should be designed so they cannot be easily or accidentally disconnected.
Brooks Instrument uses special connectors for hazardous-area MFCs that feature simple locking mechanisms to ensure the connections open only when there are no gasses or dust concentrations present. In addition, it’s important to use communications and power cabling that are certified for hazardous areas.
MFC Stability: Consistency and Accuracy Are Key
A common practice is to remove and test/recalibrate MFCs during maintenance intervals or when the process gas is changed. However, these efforts take time and can sideline a system if there are no spare MFC replacements.
Choosing MFCs with long-term stability, or low drift, can help avoid this. Brooks Instrument makes MFCs specially built to operate in the harshest environments with an IP66 enclosure rating and a long-term certified flow accuracy of ±0.6% of SP.
An additional useful feature to help eliminate unnecessary recalibration is a zero-drift diagnostic. This is a test users can access to confirm the device measurement has not drifted outside of specification, even though the device may have been in use for one or two years.
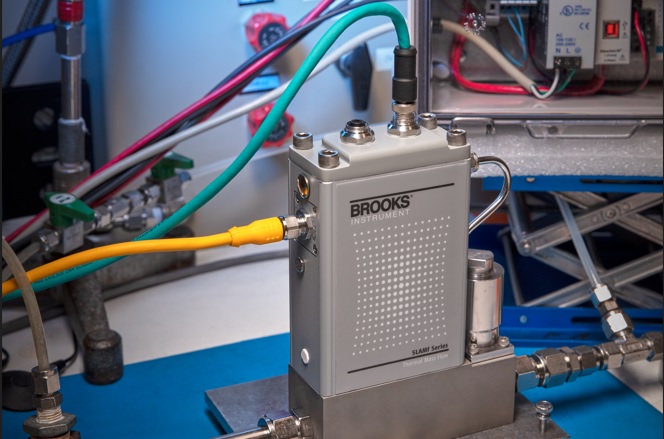
Diagnostics and Digital Communication
MFCs with high-speed digital communication protocols such as EtherNet/IP and PROFINET make it easier to collect critical real-time performance data like flow rate, device temperature, valve position and sensor condition.
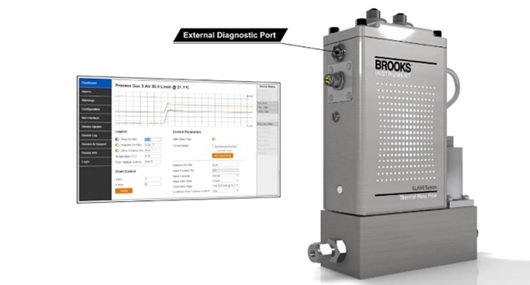
MFCs with high-speed digital communication protocols such as EtherNet/IP and PROFINET make it easier to collect critical real-time performance data like flow rate, device temperature, valve position and sensor condition.
Look for a full suite of diagnostics, supported with browser-based software packages embedded in the MFC and accessible via high-speed communications interfaces. This makes it convenient to access and manage these capabilities from a laptop, even while the device is running.
The Final Selection
When selecting the right MFC for hazardous-area chemical and petrochemical plant operations, working with technology suppliers like Brooks Instrument that have extensive knowledge of these regulatory requirements and standards can help ensure you choose the best device for your application.
To better understand approvals and certifications, visit the dedicated resource page from Brooks Instrument.