Fuel depots are under a lot of pressure for innovation these days. The dense market and difficult situation because of the pandemic does not allow the same margins the mineral oil industry is used to anymore. Furthermore harsh requirements for accuracy due to state regulations must be considered while malpractice has to be prevented. The ultimate goal is to eliminate the room for human error as much as possible while having a flexible, integrated system. This goal is achieved by state of the art technology and IoT applications.
The powerful flow computer family of the MFX_4 series is living up to the highest standards for flexible and reliable processes like measuring, blending and controlling of loading processes and custody transfer especially for petrols. This fourth generation of M+F controllers combines the experience of 30 years and 18.000 installations with state of the art technology and communication standards. Because of these standards, the MFX_4 computers can be configured very easily, integrated into any network environment and be maintained remotely. A decentralized architecture of central controllers but decentral operating units further expands the bandwidth of applications.
The Compact Pro device is combining the capabilities of a flow computer with the functionalities of a state of the art human-machine-interface integrated in a zone 1 explosion proof housing in accordance to ATEX. It is controlling your fluid processes, while all viable data will be transmitted with one of the various field communication methods.
The flow computer can simultaneously operate 2 duty meters or 1 duty meter + 1 blending process while also controlling up to 10 additives at once. Furthermore it can process measurements of temperature, density and pressure. Various analogue and digital inputs and outputs provide the computer with great flexibility for any application. This makes our computer the one-device solution for your loading platform, no additional controllers needed.
The communication with other devices in the field or higher systems like SCADA and terminal management systems is realized via CANopen, MODBUS TCP or OPC. The Loading data will be transferred to an original documents computer via Ethernet instantly to meet state regulations.
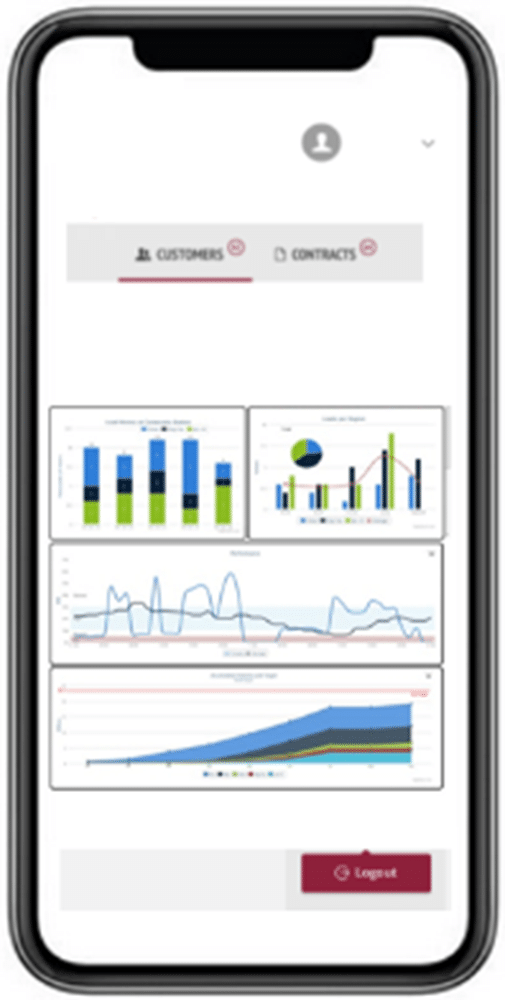
The Compact Pro flow computer comes with a 10,4´´ color-display and an alphanumeric keyboard so all operation and configuration can be done on spot. An additional RFID-reader prevents unauthorized operation and guarantees the correct assignment of customers or operators to minimize human factors in loading processes. The current loading data can be related to a customer or individual company employee so the data is fed into the ERP system at run time.
Optional tools are available to transmit the loading data straight to a mobile device. The Terminal can be considered the entry point to our split architecture system and can visualize and operate up to 6 measurements meaning 6 duty meters or 6 blending processes including 10 additives each.
The various functions make the MFX_4 Compact Pro an ideal solution for single or multi product operation with automated temperature and pressure compensation with or without blending.