The traditional actuator’s tower design usually works well with slurry knife gate valves. But only as long as the valve is small enough. The bigger the DN, the higher will be the valve. Let us say we need a valve DN 1200. Using the tower design, it means the valve would be extremely high in open position: 5,60 meters! Extreme heights also mean a higher centre of gravity. This makes the knife gate valve more difficult to handle, less stable during assembly and harder to access for maintenance. In other words, less safe.
Knife Gate Valve Actuator Cylinders Repositioned to the Side
Flowrox Slurry Knife Gate valves use a different approach for sizes from DN 900 to impressive DN 1500. The innovation brought by Flowrox eliminates the knife gate valve’s cylinder tower and instead repositions two actuator cylinders to each side of the valve. According to the example above, Flowrox DN 1200 knife gate valve now measures 3,60 meters in a fully open position – 2 meters less (see Figure 1).
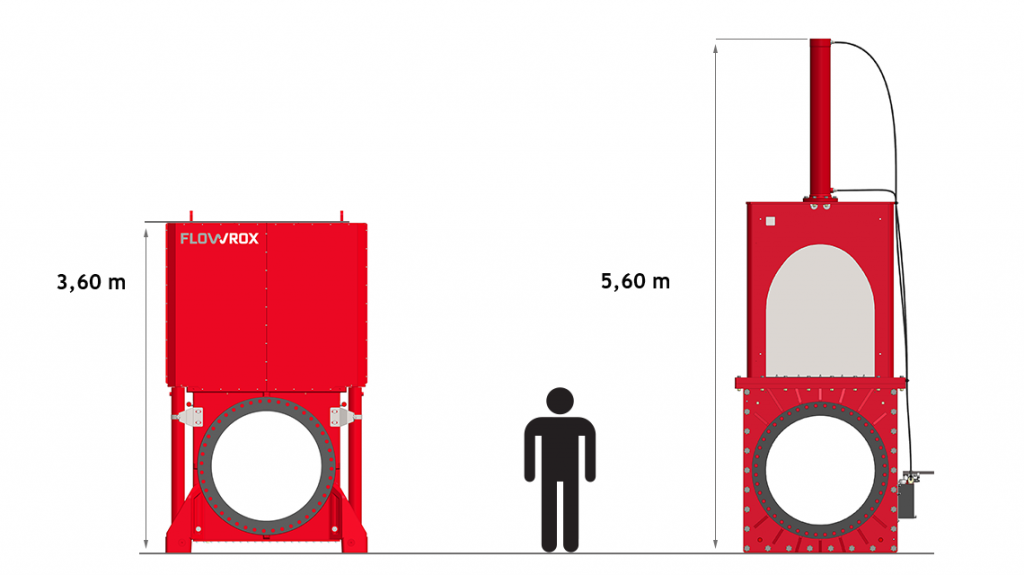
Benefits of Eliminating the Tower Design
Heavily reduced height of the valve means the centre of gravity is positioned lower. Therefore, the knife gate valve is more stable and safer. It is not only easier to install, but also requires much less empty room above the valve. All maintenance access points are situated below 2 meters from the ground making them easily accessible. Similarly, all other connections can be done on or from the ground instead of high in the air. In the case of tower design, the service work typically needs to be done 3-4 meters above the ground, causing a safety risk, requiring additional safety procedures and consuming more time.
Entire Valve Body Cast in One Piece
Another change lies in the knife gate valve’s body. Conventionally, the valve body is made from two pieces and bolted together. Which means more chances for leaking and lots of bolting work during maintenance. Flowrox Slurry Knife Gate valve body is now entirely cast in one piece. This means there are no risks for leaking through the body. The new valve construction is simpler and more robust. Less parts mean savings in spare part inventory and maintenance time.
Choose Correct Slurry Knife Gate Valve Design for Your Application
From now on, when big slurry knife gate valves are needed (over DN 900), it would be worth to reconsider the design. The tower design results in extremely high valves which are more difficult to handle and out of reach for easy and safe maintenance. The design brought by Flowrox which eliminates the cylinder tower and repositions the actuator cylinders to the side significantly reduces the knife gate valve’s height.
Flowrox Slurry Knife Gate valves are more compact, easier to install and much more accessible for maintenance. These valves DN 900 – DN 1500 can handle pressures from 10 and down to 4 bar, depending on the size. Actuator can be either hydraulic or electric. There are flange drilling options, contact Flowrox for more information.