The TorqSense transducers have a 250% overrange reading capacity, allowing sudden spikes in torque to be measured and recorded accurately. The design also compensates for any extraneous forces, such as bending moments, inadvertently applied to the sensor, improves sensitivity and has a wide temperature tolerance. Sensor Technology has specialised in real time torque measurement for over 40 years, pioneering the use of contactless solutions based on radio frequency pick-ups that do away with the need for hard-wiring and unreliable slip rings.
Manchester University’s School of Chemical Engineering is leading energy efficiency developments in the process industries by incorporating TorqSense transducers into a test rig for analysing losses in in-line mixers. The energy consumption involved in in-tank mixing is well understood, but with in-line rotor-stator mixers the flow is often controlled independently of the rotor speed and collecting sufficient data to accurately model the process requires a large number of experiments. Now researcher Dr Mike Cooke has developed a method for obtaining the necessary information using torque measurement.
Dr Cooke explains that high shear rotor-stator mixers are widely used in process industries, providing a delivery of energy, power and shear to accelerate physical processes such as mixing, dissolution, emulsification and deagglomeration. “To scale-up from laboratory to industrial we need to understand the relationship between rotor speed, flow rate and the energy dissipated,” he says. “The first step is to link the energy dissipation rate to desired process results.” Sensor Technology’s TorqSense in-line torque meter measured the torque. TorqSense uses a strain gauge Wheatstone bridge, where four strain gauges are glued onto the transducer shaft in a square formation set at 45deg to the axis of rotation. Thus, when torque is applied to the shaft two gauges are stretched into tension and two go into compression. A rotor mounted ultra-miniature microcontroller, powered by an inductive coil, measures the differential values in each strain gauge and transmits them back to the stator digitally, via the same coil. TorqSense transducers then use modern strain gauge signal conditioning techniques to provide a high bandwidth, low-cost torque measuring solution with high overrange and overload capabilities.
Manchester University is a major user of TorqSense SGR510/520 transducers, having many installed on permanent teaching aids and various research rigs. “The students like the readout displays, which look no more complicated than a car’s dashboard,” says Dr Cooke. “For us researchers, the ease with which they can be mounted and removed is a God-send in experiments where you are constantly reconfiguring the rig.” The conclusion from Dr Cooke’s experiments is that the performance characteristics of in-line mixers can be easily modelled. This lets industrial users calculate their optimum energy consumption and tune their mixer drives accordingly. Cost savings will accrue during the whole production period, making a valuable contribution to the company’s bottom line and green credentials.
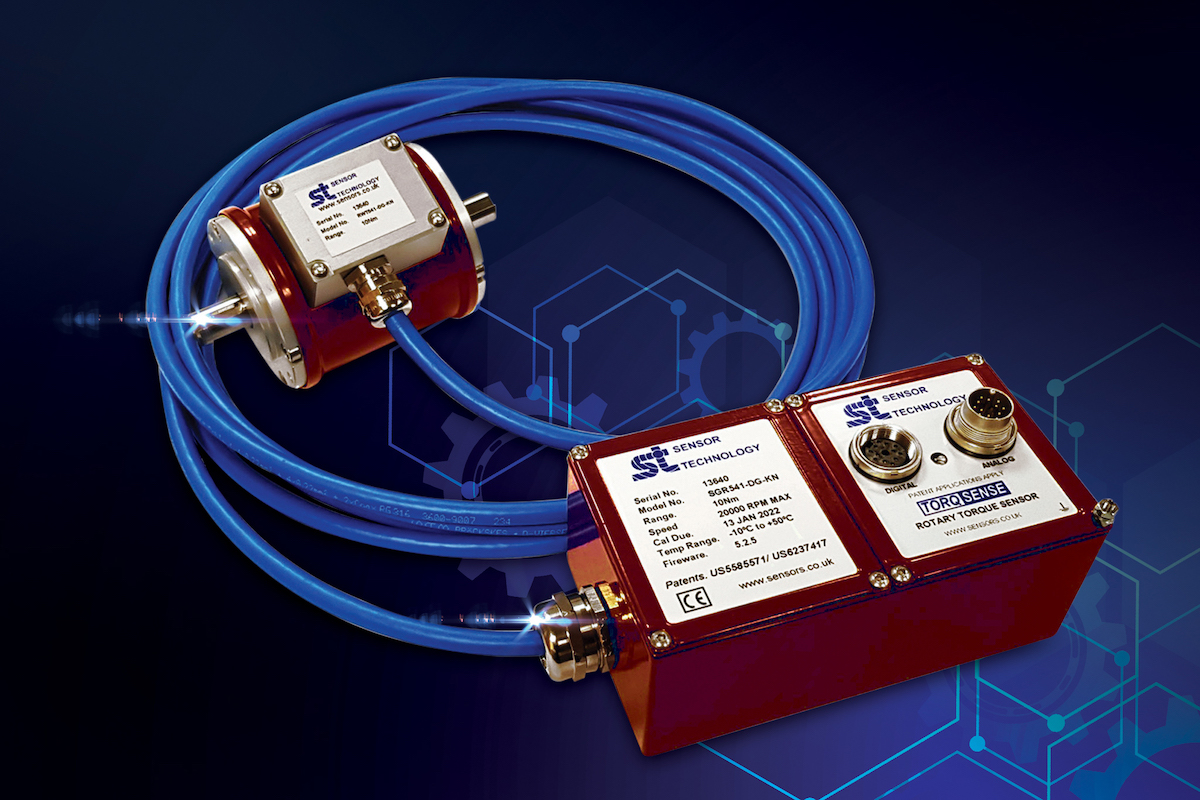
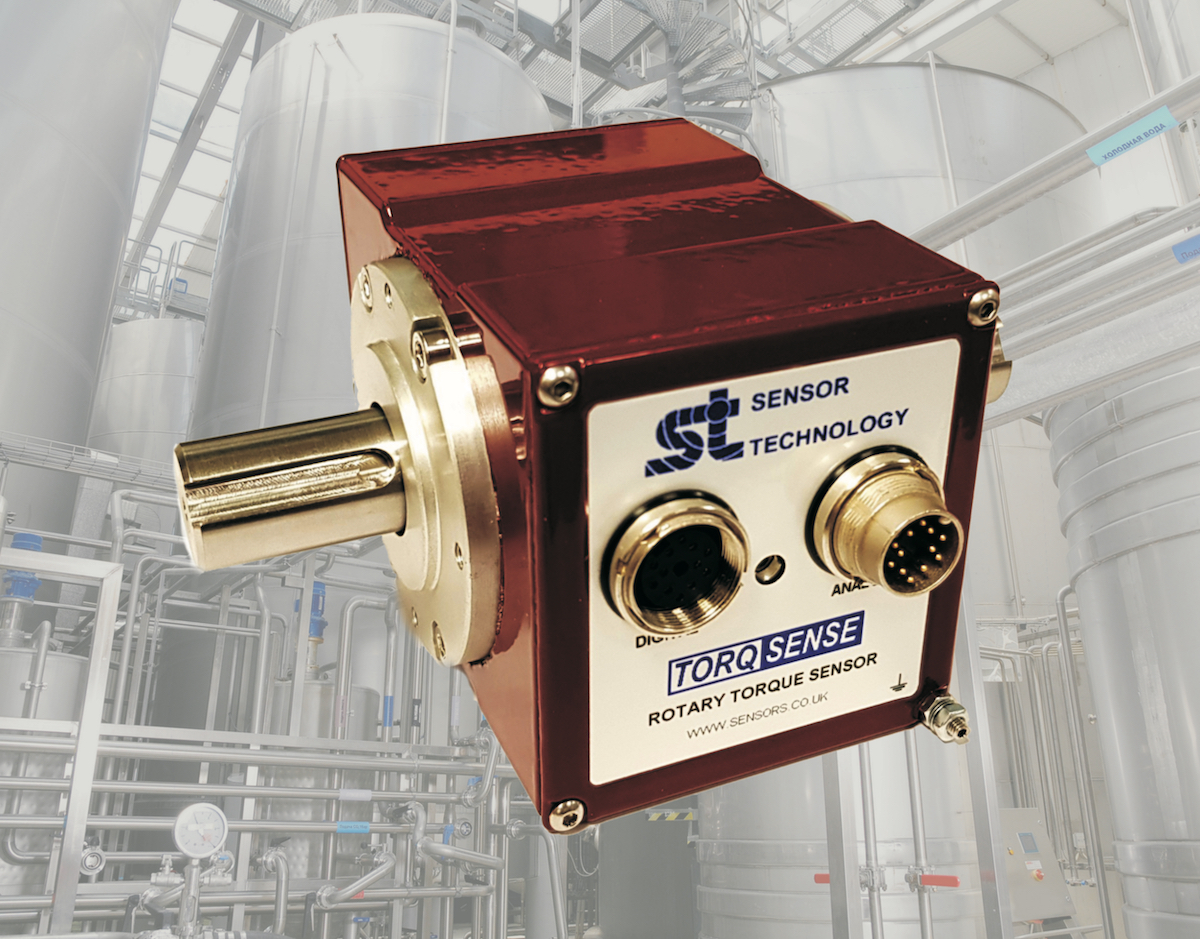
Over the years Sensor Technology has worked with many OEMs to develop high precision, high speed machines for use in pharmaceutical plants and a range of other applications. One of these, Cap Coder, has for over 10 years incorporated TorqSense units into its capping machines. Strict international rules apply to the manufacture and packaging of pharmaceutical products and require that the correct environment is maintained within the bottle or other packaging following capping. To this end, Regulation USP 671 provides a guide to the torque range to be used for screw type containers with varying closure diameters. By ensuring that bottle caps are successfully applied to the bottles within the required torque tolerances, the integrity of the product can be maintained.
Bottle capping is nearly always performed at very high speed, so that production targets are met. A major advantage of TorqSense is that it does not need to physically contact either the bottle caps or shaft of the torque head it is monitoring, instead using an inductive coil. “All you have to do is set up a TorqSense transducer in the capping machine and turn it on.” explains Mark Ingham of Sensor Technology. “Our SGR530/540 TorqSense units are working for long hours at high speed on the capping machines, where they are required to be 100% reliable and consistently accurate.”
Fast and accurate torque measurement is becoming more and more important as all sectors of manufacturing automate their physical processes while also needing to improve the recording of production performance data. TorqSense is used in many industries from automotive to materials handling, test and measurement, FMCG (fast moving consumer goods) production, power generation etc. Sensor Technology is working with user-partners in many sectors to assess the new TorqSense units in a range of working environments.