In the chemical industry, it is common to build pilot plants to minimise risks in the final plant, especially in advanced chemicals. In this ‘step-in-between’ it is essential to measure the critical fluids very accurately to draw the right conclusions in time. Very often, pumps used in pilot plants to control the liquid flows, whereas accurate dosing of the liquids and efficient data processing are key to success.
Accurate, fast and efficient data is a must for pilot plants
When measuring critical fluids, the amount of highly accurate data – which is needed to make the right decisions for the final plant – need to be collected accurate, fast and efficient. If fluids cannot be measured accurately enough, tests must run for a very long time to finally collect the required data to build decisions on. Pilot plant tests usually cost a large amount of money, especially when a long testing time is involved. However, when the system is equipped with accurate instrumentation, the test duration can be shortened dramatically.
Dosing pumps
There are several solutions to choose from when dosing fluids in your process. Many users choose a volume-based dosing pump. A dosing pump is a typical solution to dose a certain amount of fluid into a process. This volume-based approach is good enough for non-critical processes. But if the process is critical, the operator needs to be sure that the dosing pump is dosing the correct amount. At this point, an accurate flow meter is the missing link.
Pump control
By integrating a flow meter in the process, the flow created by a (dosing) pump can be measured and corrected. The flow meter measures the mass flow and the measured value is used to correct the pump directly (‘pump control’). A flow meter with (external or internal) controller functionality converts the dosing pump into an advanced closed-loop dosing system, thus constituting an accurate dosing solution.
Mass flow meter
A dosing pump operates volumetrically and dosing results are therefore subject to variations in temperature or internal leakage due to wear. For more accurate and reliable dosing, a mass flow meter would be the preferred choice as it compensates for the weaknesses of the dosing pump. A Coriolis mass flow meter measures accurately and independently of fluid properties and creates a very reliable and accurate dosing system when used in the combination with a dosing pump.
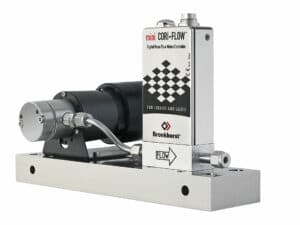
Accuracy, dimensions and robustness of the flow meter
Many types of Coriolis mass flow meters are available on the market, but can all of these become a perfect fit? In many cases, the application is special in one way or another. As previously mentioned, in pilot plants several things come together. That is why the following three specifications are particularly important when you select your Coriolis mass flow meter:
- In laboratory applications, the flow meter should perform very accurate to enable scientists to find the real truth. Specifications from manufacturers are sometimes difficult to achieve in practice, which is why it is recommended to perform a practical test to measure the practical performance of such a flow meter (not the theoretical value).
- At industrial applications, reliability and robustness are usually the most important assets. But this can come at the expense of other specifications, such as accuracy. In an industrial pilot plant, however, truth-finding by accurate measurement prevails, as in the lab.
- The third point to consider is the dimensions of the components in a pilot plant. Size matters, especially concerning the compactly built pilot plants. Most typical industrial Coriolis flow meters bring a serious amount of space and weight into the equation. Therefore, the skid or entire system must be scaled up significantly, which introduces the necessary costs and system inertia.
Dosing solutions for pilot plants
So, we can conclude that two worlds come together in a pilot plant: lab and industry. Dedicated instrumentation offers the best pilot plant performance. An accurate dosing pump is a good solution for non-critical processes. However, for critical processes in a pilot plant, process engineers should select the right Coriolis mass flow meter, where practical accuracy is relevant, but compactness and robustness must also be of sufficient value.
About the Author
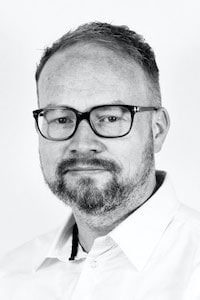
As a product manager liquid flow-technologies at Bronkhorst High-Tech BV in Ruurlo (NL), Ferdinand Luimes mainly focuses on the intersection of sales, technology and marketing.
On a typical day he deals with a wide range of activities from collecting and analysing market data till supporting sales. But if you’ve lost Ferdinand, check out the M for marketing.