It is often thought that reducing the OPEX will be at the detriment of an increase in the CAPEX, or vice versa. So far installation of vapour recovery units (VRU) in terminals, have been no exception.
The prevailing method of VOC vapour recovery globally is, and has been for decades, adsorption of the VOCs onto activated carbon. Following adsorption, the activated carbon is regenerated by applying vacuum to these, the so-called pressure swing adsorption principle.
Traditionally the vacuum for regeneration is provided by a vacuum pump. Originally liquid ring pumps were used, later around the millennium, other vacuum pumps like the rotary vane and screw types appeared in VRUs.
A very high proportion of the OPEX of a pressure swing adsorption VRU, is energy costs to operate the vacuum pumps. For the last 15 years, no development of standard VRUs for normal oil terminal operation have been introduced, with focus on significant reduction of the vacuum pumps energy consumption.
With the emergence of a new generation of VRUs, the energy consumption of vacuum pumps in standard VRUs, has been brought to the top of the agenda. The innovative group of VOCZero, with its many decades of experience in the vapour recovery industry, has brought the distribution terminal line (DTL) of VRUs to the market, which has superior energy efficiency.
The DTL is a pre-engineered range of VRUs, covering the vapour recovery needs in terminals from one to fourteen loading racks or nominal VOC vapour capacities from 100 to 6,000 m3/h, in one module. The DTL VRUs are based on VOC adsorption onto activated carbon, and pressure swing regenerated by vacuum.
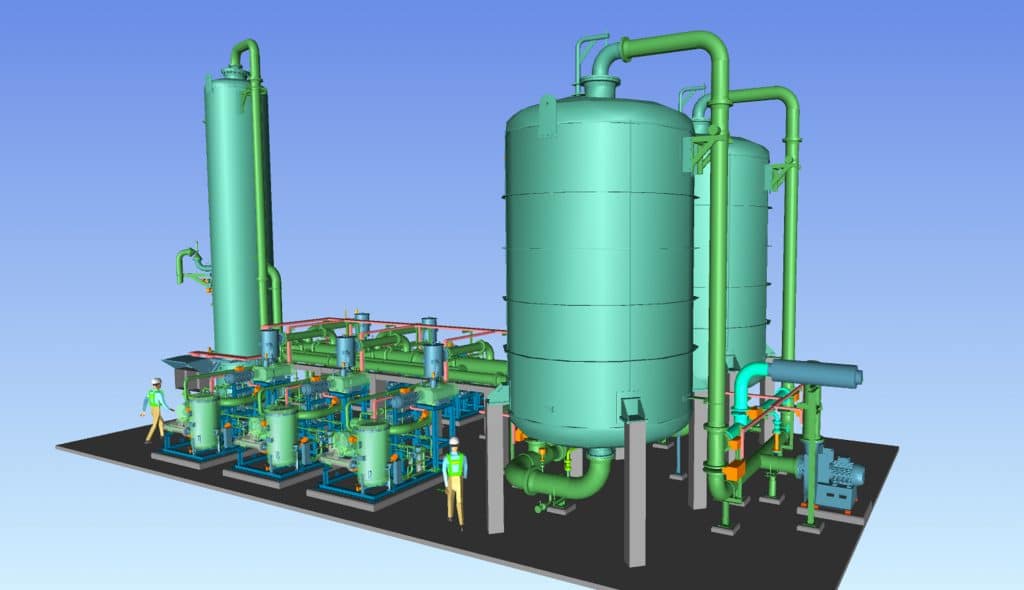
OPTIMISED VACUUM SYSTEMS
As standard, the vacuum system consists of rotary vane vacuum pumps, which have the lowest energy consumption among vacuum pumps, equal to the screw vacuum pumps. Upstream the vacuum pump, Roots blowers are installed as boosters to the vacuum pumps. Roots blowers are characterized by being able to transport large vapour volumes, over a relatively modest pressure range, highly energy-efficient. In the DTL VRUs, roots blowers evacuate VOC vapour from the activated carbon, in the pressure range 10 to 20 kPaA. At 20 kPaA, the VOC vapour volume is compressed to approximately the half of the volume it makes out at 10 kPaA. This requires a vacuum pump with only the half vapour capacity operating from 20 kPaA, in comparison to if it operates from 10 kPaA.
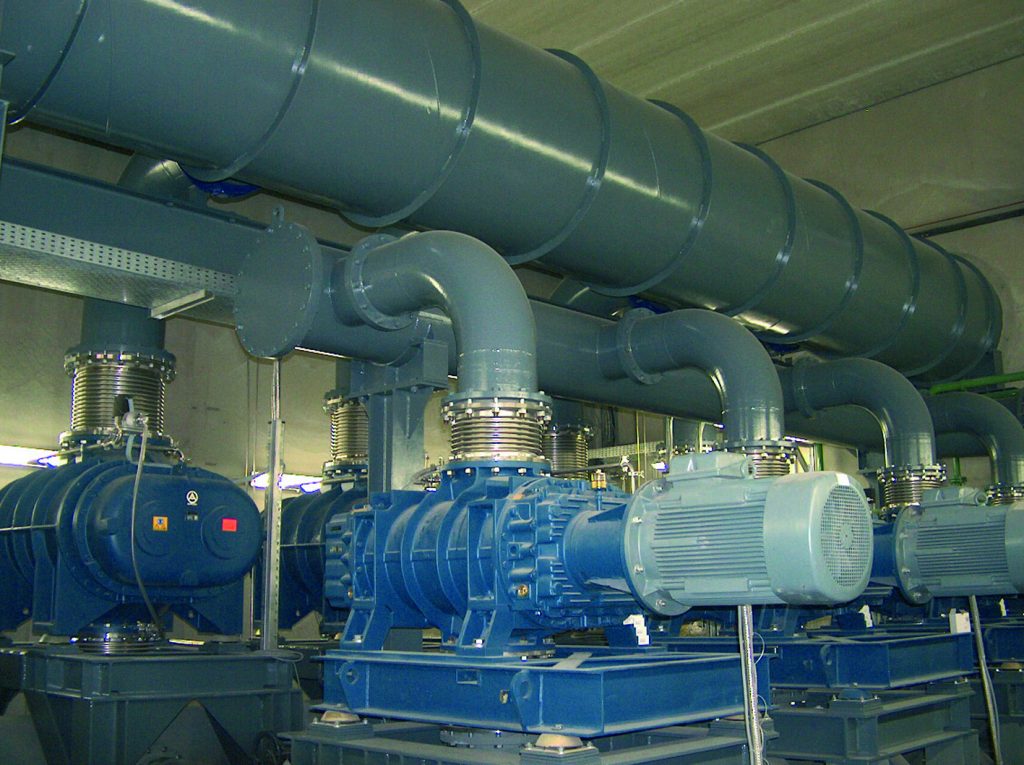
The very high energy efficiency of roots blowers, combined with rotary vane vacuum pumps of half vapour capacity, compared to the necessary vapour capacity of vacuum pumps installed in conventional pressure swing VRUs, gives an overall energy saving of 10 – 25% per m3 VOC vapour processed, relative to VRUs equipped with only screw vacuum pumps, and 30 – 50% relative to liquid ring vacuum pumps.
Following the reduction in the necessary vapour capacity of vacuum pumps, physical dimensions and weights of machinery and piping are reduced, and so is the footprint of the installation, and also the CAPEX of the DTL VRUs.
The vacuum system used in the DTL VRUs is extremely reliable. The rotary vane vacuum pump was introduced in pressure swing VRU service around the millennium. The experience has shown that this vacuum pump type in general operates with VOC vapour in VRUs for more than 15 years, without need for overhauls, which is highly unusual compared to other types of vacuum pumps or rotating process machinery, and it definitely keep the OPEX of the DTL VRUs at an absolute minimum. The roots blower has a history dating back to 1860, when it was patented. Today it is one of the most common blower, millions are installed as superchargers for combustion engines. Process wise the roots blower is simple and very reliable machinery.
It is particularly easy to maintain the vacuum system of the DTL VRUs. Only change of lubrication oil and oil filters is required at prescribed intervals.
VRU OPERATION ENERGY MANAGEMENT
For oil distribution terminals, in which VOC vapour may be returned from loading of ships and/or includes VOC vapour balancing with storage tanks, the DTL VRUs includes a feature for a very high rate of energy saving, called adsorber to adsorber equalisation (ATAE). 20% of the energy usage in a pressure swing VRU, is spend by the vacuum system on evacuating the adsorber vessels from atmospheric pressure down to 50% vacuum. In the DTL VRUs, the adsorber vessel which has finalised the regeneration of the activated carbon and still is at 90% vacuum, is equalised back to a higher pressure from the other adsorber vessel, which is at atmospheric pressure and going into regeneration. The resulting pressure of the two vessels after the equalisation is 45% vacuum.
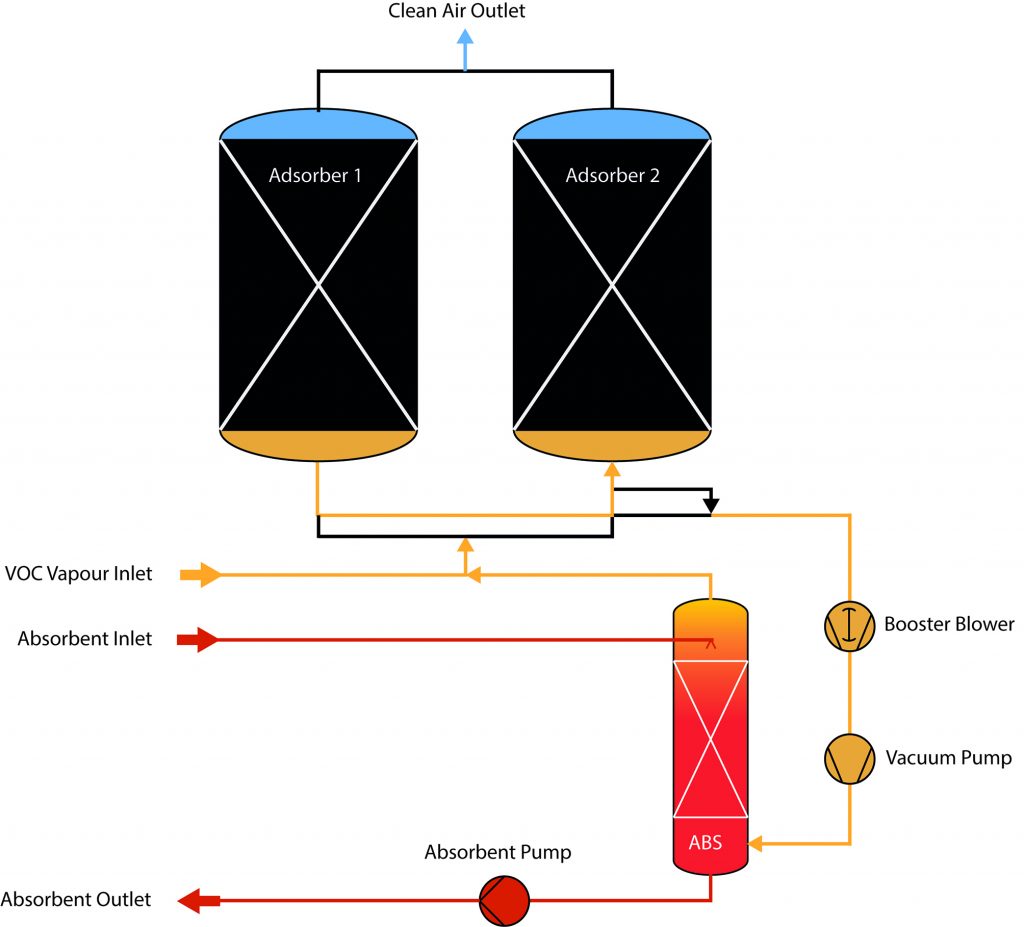
The evacuation of air or inert gas, from the second adsorber vessel going into regeneration, from atmospheric pressure down to 45% vacuum, comes for free, as the vacuum system does not spend energy on this part of the evacuation.
The optimised vacuum systems and the ATAE energy saving features, built in as default to the DTL VRUs, reduces the energy consumption of the DTL with 20 – 50% per m3 VOC vapour processed, relative to conventional pressure swing VRUs.
Another energy saving feature built in default to the DTL VRUs is the emission control energy manager (ECEM). The ECEM measure the VOC emission in the vent from the VRU, and when the VOC emission reaches a pre-set value, adsorption switches from one adsorber to the other, and start the regeneration of the adsorber which is saturated with VOC. When loading in the terminal is below the design volumes, or loading of products mainly consist of gas oil or diesel, resulting in VOC concentration of the vapours below design figures, the adsorbers will last longer time before saturation, and the vacuum system will rest for a longer period. As oil distribution terminals typical have peak loading hours and low loading hours throughout the day, the ECEM will show significant energy savings in the low loading hours.
Combining the optimised vacuum systems, the ATAE and ECEM energy saving features of a DTL VRU, will obviously save a considerable amount of OPEX in an oil distribution terminal equipped with a VRU, over the year, compared to conventional VRUs.
FOR MORE INFORMATION:
This article was written by Morten Reimer Hansen, Senior Vice President BD & sales at VOCZero, +45 8172 2100, morten.reimer.hansen@voczero.com.