
From this mixture, high-purity butter oil can be separated as a valuable raw material. An important instrument for its automated, economical and high-quality refinement is the ITM-51 turbidity sensor. In addition, sensors for flow rate, point level and temperature that match perfectly the specific medium support process control for maximum system efficiency and reliability.
The water-butter oil mixture from the plant rinsing process is pumped into a stacking tank in which natural phase separation already takes place. In a separator the butter oil phase can then be concentrated to a refinement degree of 99.5%. This quality level can be supervised in several ways. Experience shows that visual control during phase separation does not allow sufficient accuracy for a consistent final product. Continuous sampling and laboratory control assures a better quality, but this requires a lot of manpower and is very cost-intensive.
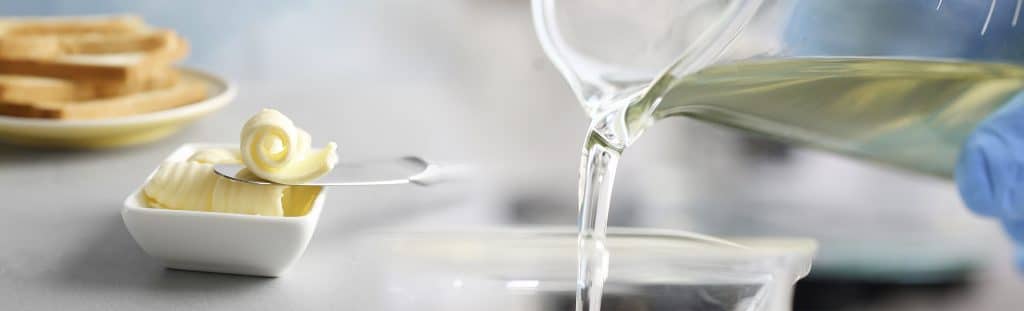
The automated phase separation based on high-precision turbidity measurement of the butter oil mixture with the ITM-51 turbidity sensor is the most efficient method. In practical customer applications this technology proved to ensure consistently high and verifiable production quality in operation.
The ITM-51 turbidity sensor uses the backscattered light method, which detects the reflection of particles in the medium. With its front-flush sensor head, it can be integrated very easily into the pipe system using a weld-on socket or adapter. For precise separator control, the ITM-51 can be programmed individually in the application itself. For this purpose, samples were taken in a test run, analyzed in the laboratory and compared with the values displayed in the sensor. In the exemplary practical case, a range of 0-50 % TU was preset for a target maximum value of 0.5 % water content in the butter oil mixture.
The use of this technology provides a double benefit:
The high process reliability in the separation of the phases ensures, on the one hand, a constant quality of the butter oil gained and increases the value margin. On the other hand, the waste water management is considerably simplified and the disposal cost reduced, since the residual water is only contaminated to the minimum.
A number of other hygienic measuring instruments are used in the entire plant control system.
The reliable operation of the separator is monitored by one flow meter each in the separator inlet and separator outlet. Due to the low conductivity of the butter oil mixture, magnetic-inductive flow meters cannot be used here. The HM-E turbine flow meter is ideal for this application. Independent of the conductivity of the media, it achieves a very high measuring accuracy due to a non-contact pulse measurement.
At certain intervals, the residual mass from the separator has to be emptied into a discharge drum. The fill level of this container must be monitored for automated control of the entire process. For this purpose, either a continuous level measurement with the potentiometric NSL-F is possible, which ensures fast and very precise level monitoring even with the pasty, creamy mass. Alternatively, an NCS point level detector can be used, which is likewise independent of the conductivity of the medium and indicates with a full signal that emptying of the discharge container is required.
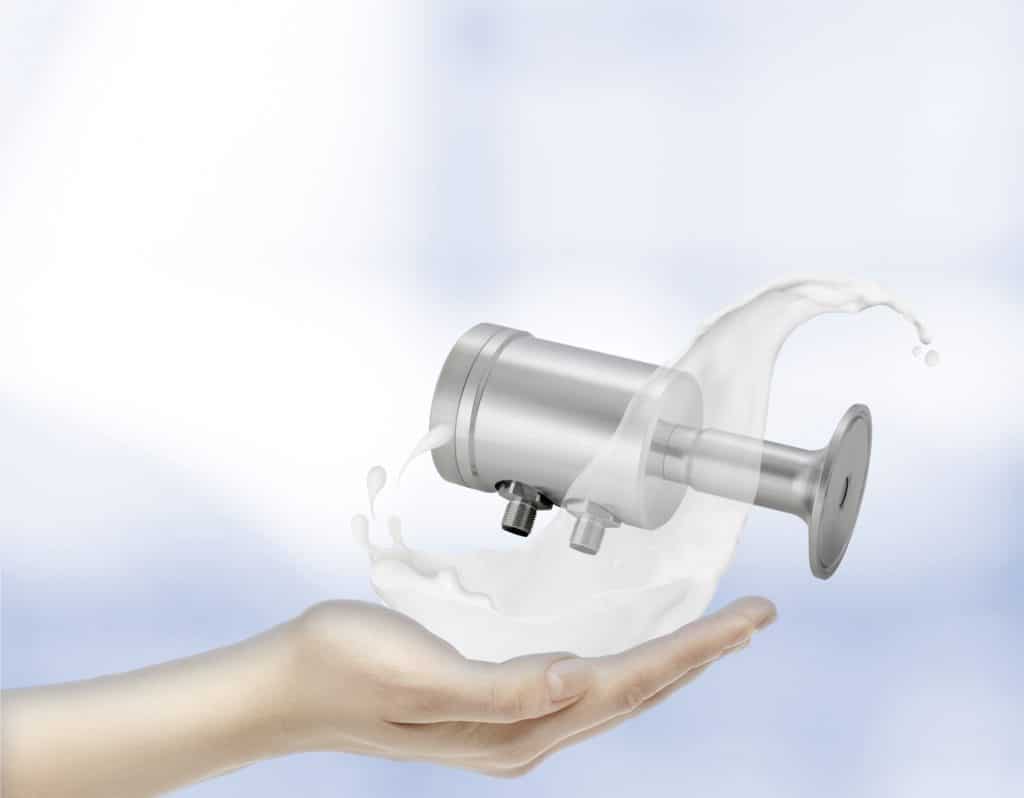
Process monitoring based on temperature is made possible by a large number of different sensor types. For example, if the product line is to remain suitable for the use of pigs, the flush TFP variant can be selected, as this means that no components protrude into the pipeline in the inlet.