Biomanufacturing, a complex modern industrial process system, relies on numerous pieces of equipment working in concert to produce life-altering therapeutics. The equipment relies on various subsystems to achieve the desired results. In a bioreactor, one of the most essential subsystems provides gas management for the gases necessary for cellular metabolism. The thermal MFC is at the center of the gas management subsystem, precisely measuring and controlling the delivery of pertinent gases to the bioprocess.
Why You May Never Look Back After Using a Smart MFC
Fortunately, modern day mass flow control devices, with their highly integrated microprocessor-based electronics, are extraordinarily robust and reliable. The capabilities of these devices, due both to their electronic hardware and the supporting firmware, offer more than just gas delivery. These devices now possess native “intelligent” functionality associated with the industrial internet of things (IIoT), namely, data management and connectivity. This functionality can be used to improve or enhance biomanufacturing operational efficiency.
Properly applied, specified, and configured, intelligent mass flow control devices are able to gather, generate, and communicate a variety of data. These devices along with other typical bioprocess equipment data sources (e.g., sensors, probes) have the capacity to generate enormous amounts of data. It should be kept in mind, not all data is useful. Sufficient contextual data can provide information necessary to gain insight and make appropriate decisions. For additional information about the advantages of using rich data from your digital instrument, check out this blog post from our product expert, Steve Kannengieszer.
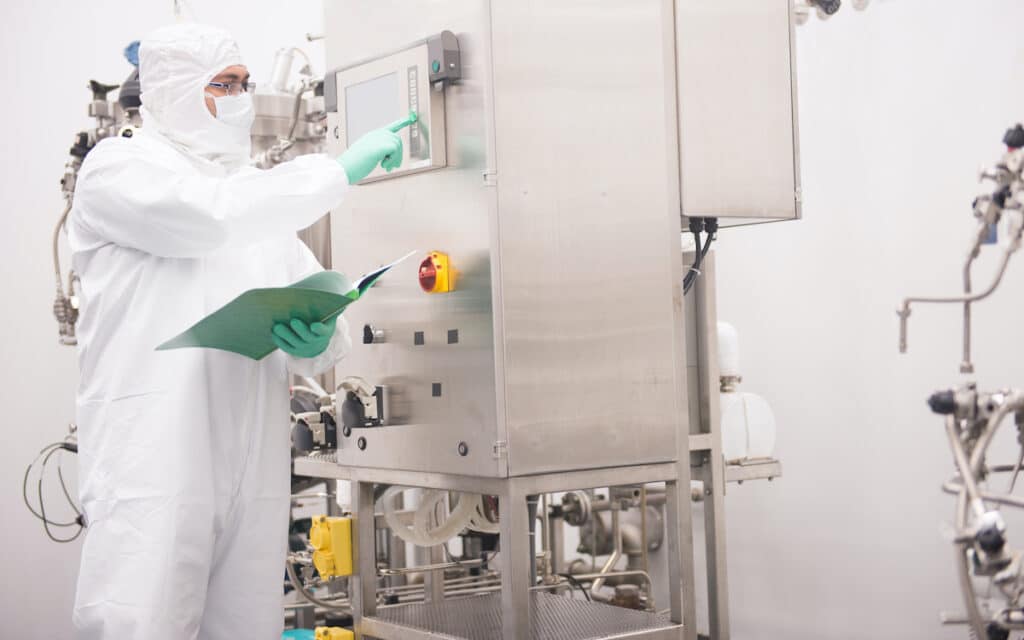
How The Data Can Help You
Understanding available device data allows definition of meaningful data categories. Benefits of consensus categorization include: (a) creation of a common language with which stakeholders can communicate, (b) prioritization of design activities, and (c) simplification of lifecycle management. As an intelligent component, or device, three specific MFC data categories can be defined: pedigree, performance and reliability. Specific data within each category may be used to create new ways in which the capital asset (bioprocess equipment) is managed. Pedigree covers static configuration and installation attributes, like serial number, network address and calibration. Calibration-related data includes gas type, flow range and calibration date. The performance category addresses dynamic operational attributes such as gas flow rate, temperature and pressure. Reliability category data may be used for troubleshooting and maintenance of the MFC, the bioreactor or the process. Relevant data combined from each of these categories can contribute to bioprocess analytics.
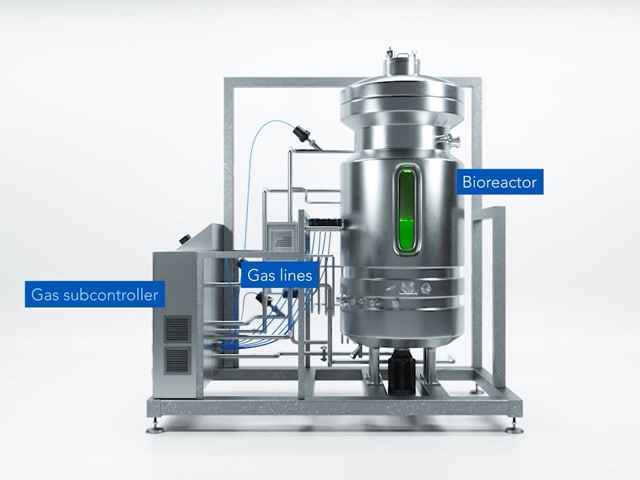
Use in Bioprocess
Bioreactors include several functional subsystems to create and control the proper process environment for growing cells. Numerous process parameters are measured including temperature, agitation speed, dissolved oxygen (DO), pH and pressure. The gas management subsystem is used to control both dissolved oxygen and pH levels. Essential for this control are thermal mass flow controllers (MFC). Typically, air and oxygen MFCs are used for dissolved oxygen control while a carbon dioxide mass flow controller is used for one side of pH control (the other side uses liquid base addition). MFC response, stability, and reproducibility are critical in maintaining proper dissolved oxygen and pH levels. MFC performance is verified across a wide flow range assuring MFC product repeatability and reliability. Mass flow controller response and repeatability have direct impact on DO and pH control loops, therefore, system performance. For a better understanding of intelligent MFCs in a bioprocess, view this video.
In Summary
Change is a constant force, as pervasive in the biopharmaceutical industry as in any other industry. As biopharmaceutical manufacturers adopt technologies to create value and sustain competitiveness, so too, will equipment and component suppliers. Industry 4.0 principles will define a new, more agile biopharmaceutical industry. Fortunately, the path to achieving such goals is facilitated by myriad devices, capable of generating huge volumes of data. Incremental change is expected, with some increments being more far-reaching than others.
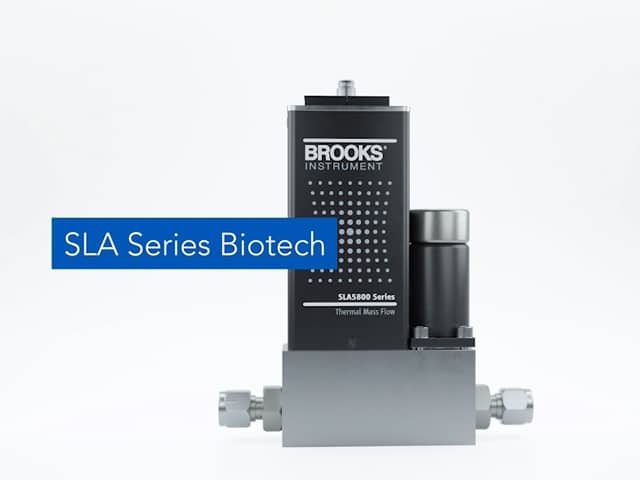
Incorporation of intelligent devices and, the appropriate integration and use, of their data is just beginning. As capabilities and requirements change over time, included among possible incremental changes may be a shift in subject matter expertise, perhaps, ultimately leading to enough machine intelligence to supplant the bioreactor and device suppliers’ subject matter expertise, placing device, equipment and process troubleshooting, and maintenance fully in the hands of the drug maker. In any case, data and digitization, regardless of how and when it is leveraged, will create new opportunities for efficient, reliable drug supply.
Additional Resources
To learn more about how the SLA Series Biotech MFC operates, check out the Theory of Operation video here. Or, to access the white paper on this topic, click here. For information on the Brooks Instrument SLA5800, read the product page.