Application
Remote Tank Monitoring
Market
Specialty Chemical and Lubricant
Challenge
Rayco Chemical had two major concerns; improving production forecasting at Rayco’s manufacturing facility to reduce costs and down-time; additionally, ensuring on-time deliveries to customers improving reliability of their operations. Like most companies, Rayco relies on their customers to provide appropriate lead times for deliveries, which is not always a reliable process. This creates customer service challenges for Rayco and production challenges for Rayco’s customers.
“Monitoring my remote ‘long haul’ customer tanks is a real help, it improves my scheduling and improves customer service”, said Keving Triggs, Account Manager, Rayco Chemical.
Solution
In 2018, Rayco Chemical installed the TankScan cellular tank monitoring system at their remote “long haul” accounts. The TankScan system leverages existing wireless cellular infrastructure and a cloud software application (ATEK Intelligence Platform) to eliminate large startup and setup costs associated with typical SCADA systems. The installation requires screwing the TankScan monitor into a 2” port on the top of tank and plugging in the battery. The TankScan cloud application is setup remotely and offers unlimited users, historical trending, and email/text notifications.
The tank levels are viewed from the customer login and/or from Rayco’s login, from a cell phone or from a PC at the main office. The system is very cost-effective due to its use of existing infrastructure of the internet, internet browser, email, text message and cloud compute. The user is provided with accurate readings to devices they already own, understand and support.
Results
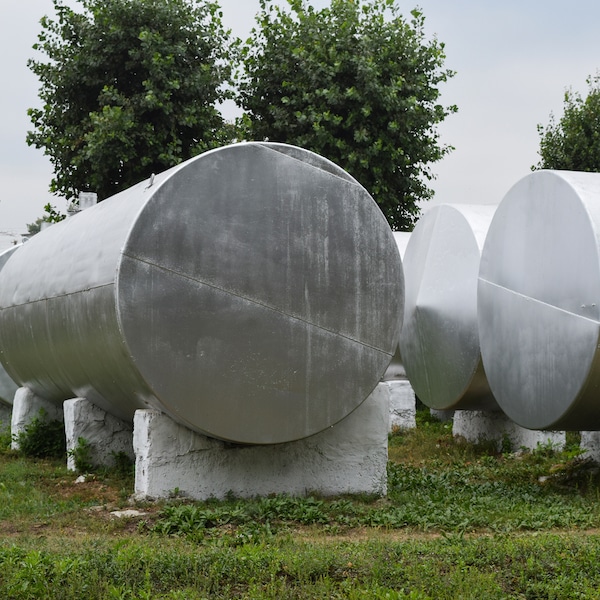
Since installation of the TankScan monitoring system, Rayco Chemicals have seen several benefits to their operations. There is improved reliability of on time deliveries. Production scheduling for large orders has been streamlined. And they now have improved confidence in their scheduling and understanding of their client’s usage.
“On time deliveries have improved with the installation of remote monitoring. This results in improved customer experience and a smoother all around execution of our operations”, said Triggs.