The choice of secondary treatment is generally between aerobic or anaerobic treatment, although a combination of both methods can also be used. Anaerobic and aerobic systems are both forms of biological treatment which use microorganisms to breakdown and remove organic materials from wastewater. The key difference between aerobic and anaerobic treatment is the presence of oxygen. Aerobic treatment is typically applied to efficiently treat low strength wastewater (with relatively low BOD/COD values) when the treatment requires the presence of oxygen. In contrast, anaerobic treatment is typically applied to treat wastewater with higher organic loading.
In aerobic treatment, oxygen (air) is used to circulate the material, providing the right conditions for aerobic bacteria to reproduce. These bacteria assimilate and then break down organic matter and other pollutants like nitrogen and phosphorus into carbon dioxide, water, and biomass (sludge). As the name suggests, anaerobic digestion utilises bacteria which do not need oxygen. They break down organic material in the wastewater into methane, carbon dioxide, and biomass (digestate).
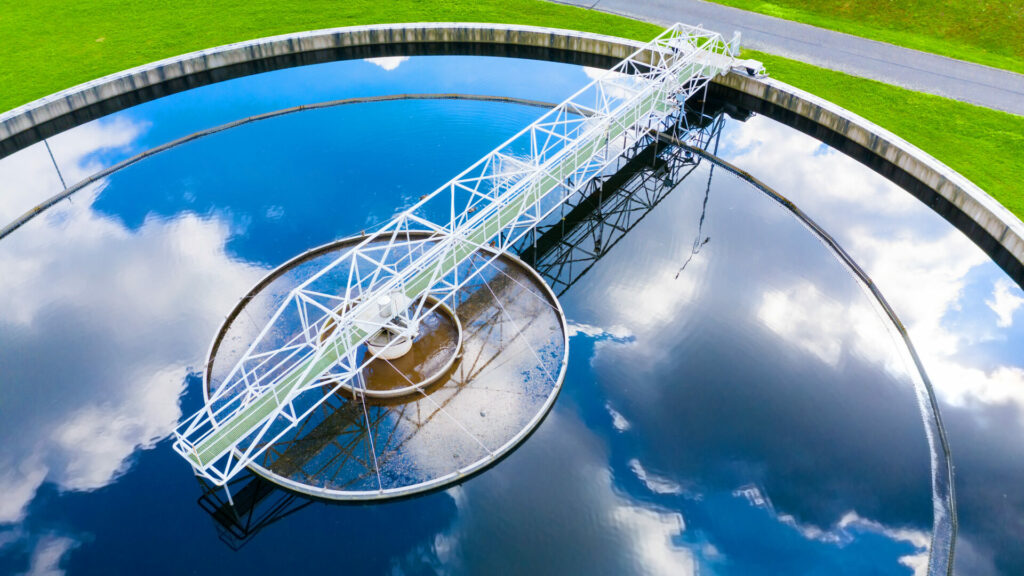
Some of the factors in favour of aerobic treatment include the fact that it has less odours (as hydrogen sulphide and methane are not produced), and nutrient removal from the wastewater to the sludge can be more efficient – meaning that treated water can often be discharged directly into the environment. However, oxygenation of the wastewater can require large amounts of energy (or a large surface area for the treatment lagoon) and untreated biosolids can settle out from the process – requiring further treatment or disposal. The capital investment (and space) required for aerobic treatment is usually greater than that needed for anaerobic facilities.
While there are pros and cons to both approaches, anaerobic digestion (AD) has a number of advantages, including:
- AD is better at dealing with slurries with higher solids content
- AD produces biomethane gas which can be captured and used as a renewable energy source (including providing the energy to run the AD plant itself)
- AD produces less sludge (digestate) for a given volume of wastewater
- The stable digestate produced by AD is easily converted into a valuable biofertiliser
- AD plants generally have a smaller footprint than aerobic treatment
Improving the efficiency of anaerobic digestion
As the points above show, one of the major benefits of anaerobic treatment is its improved energy efficiency and the lower volume of residual solids produced as digestate. However, when designing or upgrading an AD plant there are numerous ways to maximise operational efficiency – improving both economic returns and environmental performance.
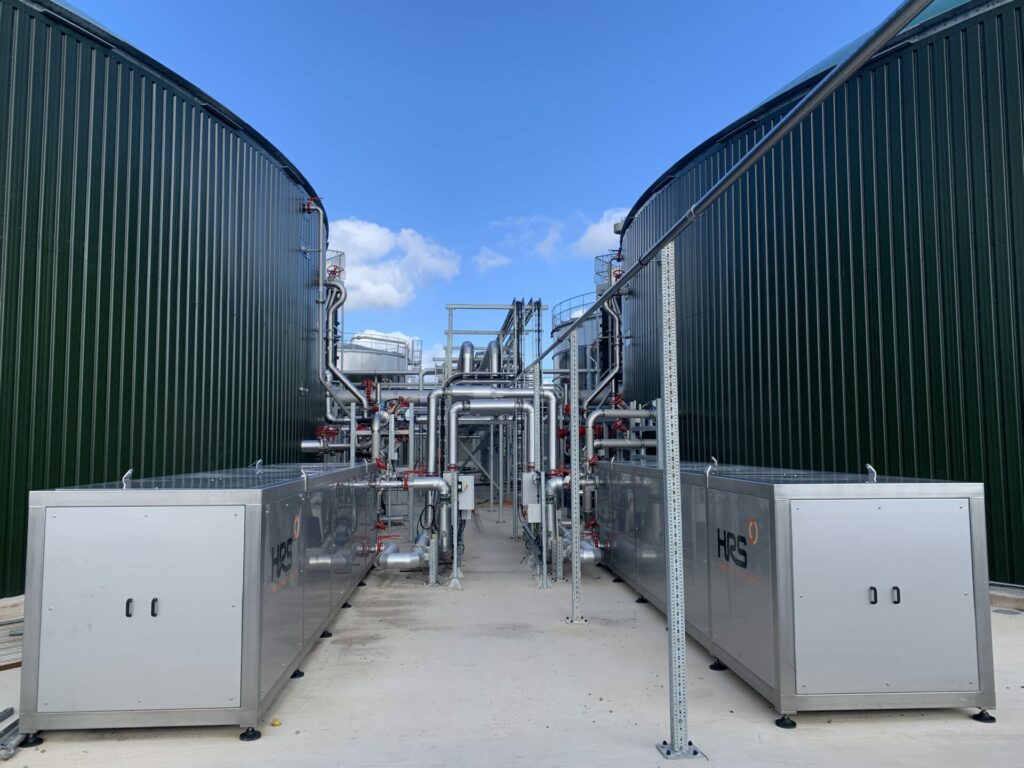
The use of anaerobic digestion is rapidly increasing in the wastewater sector.
External digester heating (for example using HRS DTI Series heat exchangers) offers a number of advantages over heating systems which are located in the digester. External heating can be checked, cleaned or serviced at any time without the need to empty (or enter) the digester. Other benefits include the fact that external systems can be designed so that one heat exchanger array heats more than one digester, and the improved thermal performance reduces heating requirements and improves the overall energy efficiency of the AD plant. Operating life is often considerably greater compared to internal heating units, and routine maintenance is more straightforward.
Cooling and recovering the heat from exhaust gases can increase the efficiency of combined heat and power (CHP) plants used to generate electricity from biogas. Using HRS G Series heat exchangers on the exhaust recovers energy which can be used elsewhere in the plant, including feedstock and digester heating, pasteurisation and digestate concentration.
The HRS BDS Series is an efficient solution to cool and dehumidify biogas for combustion. The system condenses up to 90% of the water contained in the gas, which is continuously separated before the clean biogas is ready for use as a fuel in the CHP engine, and an optional heat recovery step can reduce energy costs up to 20%.
The HRS DPS (Digestate Pasteurisation System) is designed to effectively and efficiently pasteurise digestate, feedstocks, sludge and similar materials, allowing operators to maximise the efficiency of their overall process while meeting regulatory requirements and increasing potential markets for digestate as a biofertiliser. Traditional single tank pasteurisation units simply dump this heat afterwards, meaning they are incredibly wasteful and inefficient. In contrast, the DPS recaptures this heat and uses it again, making it up to 70% more efficient than traditional single tank ‘heat jacket’ type pasteurisation systems.
After digestion and biogas production, the digestate is often separated mechanically into solid and liquid phases. The HRS DCS (Digestate Concentration System) uses an evaporation process to concentrate the digestate, meaning that the volume is decreased, reducing the costs of storage, transport and application. Using a multi-stage evaporation process, the liquid digestate volume can be reduced by up to 80%. Unlike other technologies, the HRS DCS increases the content of crop nutrients whilst recapturing energy for use in the subsequent concentration phases, increasing energy efficiency and reusing the condensate elsewhere in the AD plant, preventing additional discharge to the environment.
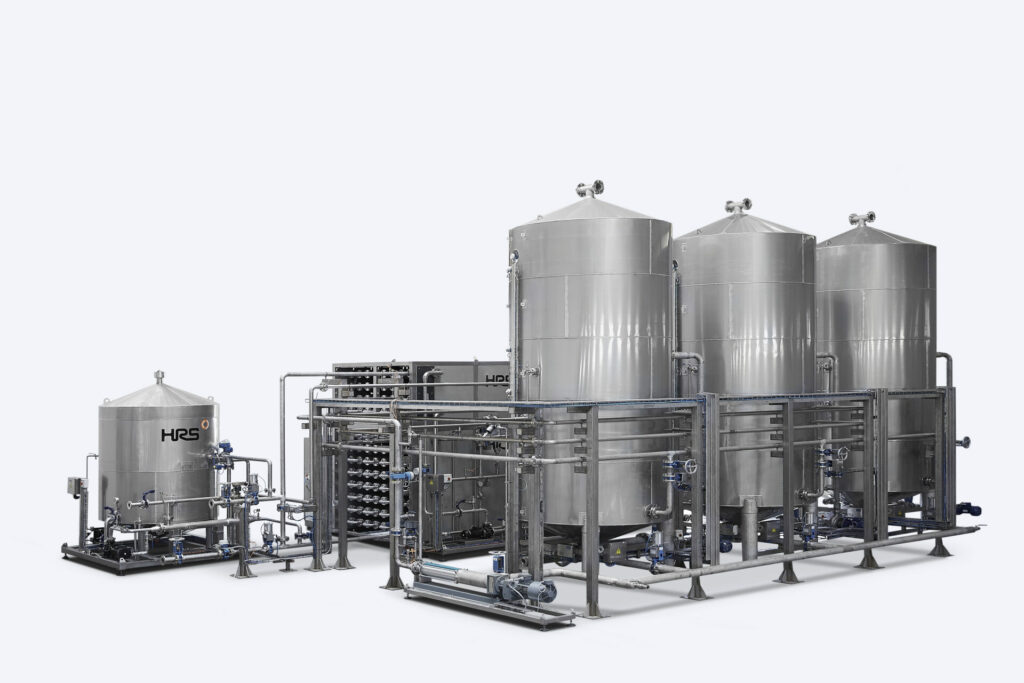
The HRS DPS (Digestate Pasteurisation System) is designed to effectively and efficiently pasteurise digestate, feedstocks, sludge and similar materials