Saving water in the paper industry
Where would humanity be if we could not write down our thoughts and ideas and pass them on to others? Even the building of the world-renowned Cheops pyramid in Egypt was documented on papyrus about 4,600 years ago. But it was certainly the industrial production of paper starting in the 19th century that paved the road for the global spread of knowledge and culture. Paper has become an essential companion in our society, for example, as banknotes, school notebooks and packaging material. But the paper industry has always had a huge thirst for water – a vital resource that must be protected.
Closed circuit
Ten liters (or 10.6 quarts) is the amount of water that it takes to produce a single DIN A4 sheet, experts say. “The high level of water usage in pulp and paper production can be sharply reduced with mechanical face seals working in a special operating mode. We call it the nonflow operating mode,” says Michael Gawin, Manager of the Cologne Service Center for EagleBurgmann. The innovation results in water savings of 90 percent. To put it simply: Double mechanical face seals are generally supplied with freshwater through an open barrier circuit. The water is drained away after its throughput. By contrast, with a nonflow operating mode, the water circulates in a closed system. It generally consists of line pipes, valves and a storage container supplemented by measurement and control devices. The water goes into the sealing system once and then remains there during its entire operating life. Only a minimal amount of freshwater from a water supply is required.
Paper factories can save huge amounts of water – even as high as the six-figure cubic meter range annually – if their pumps are equipped with nonflow seals. A paper manufacturer in southern Finland offers an example: A total of 41 pumps were converted to nonflow technology. Since the upgrades, the annual consumption of water needed for the seal supply system has been reduced by 181 million liters (48 million gallons). That enormous reduction reduces costs for plant operators.
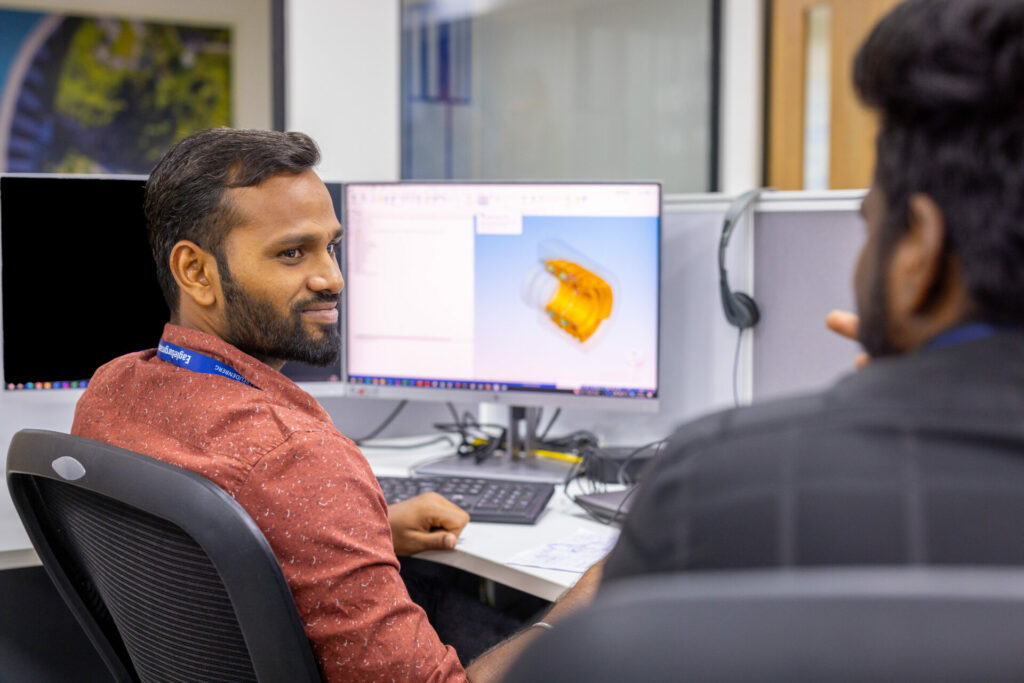
Another advantage is that nonflow seals are less susceptible to contamination and can be operated over longer periods. A convincing achievement. In 2022, EagleBurgmann began a campaign to help more customers in the paper industry become more sustainable with the help of nonflow technology.
“We entered into discussions with decision-makers with an excellent concept and were able to persuade them to become partners,” Gawin said. The lead management, the sales team and the technical departments at the headquarters in Wolfratshausen near Munich worked closely with one another and were particularly successful with a German paper company, among other customers. “We are a leading maker of containerboard, which is especially used in packaging. Every day, two machines can each produce 1,500 kilometers (about 930 miles) of paper,” says the workshop manager at the customer facility “In 2022, the company’s total production was 535,000 tons.” That is the weight of about 20 humpback whales. Many steps, great effect. Along with other eco-initiatives, the customer has been committed to reducing water consumption for years. This takes more than a single major technological advance. “We are meeting our goal with a variety of innovations, new ways of thinking and the will to continually improve. Everything has to mesh together. In EagleBurgmann, we found an ideal partner to bring the right know-how to the table.”
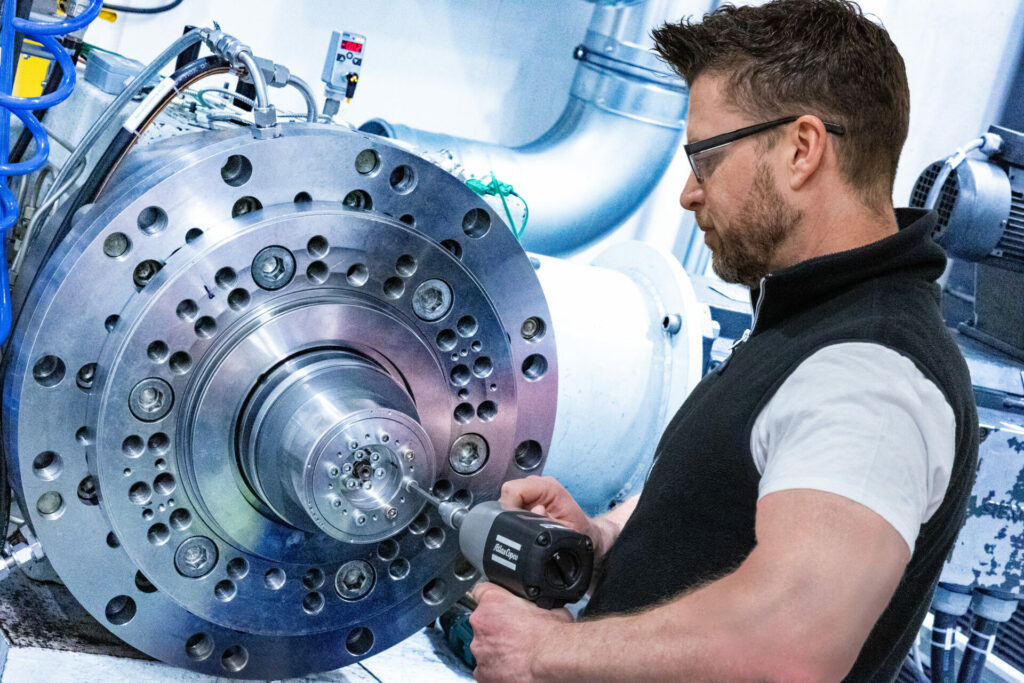
The German customer started out in 2021 with the conversion of some of its pumps and mixers, saving more than 13.3 million liters (3.5 million gallons) of water that year alone. Last year, with more modifications, the company achieved a total volume of 26.6 million liters (7 million gallons). When all the planned conversions are carried out with EagleBurgmann, the savings will reach 66.5 million liters (17.5 million gallons) per year. With that amount, you could fill the Cheops pyramid at least 25 times.