“3D printing involves cumulatively building up materials, layer by layer, using various processes. Currently, this is primarily done using plastics,” Roman Schmidt, Division Head of Software & Systems in the development department. “3D printing is creating entirely new possibilities for mechanical components than was previously possible using traditional processing methods, such as milling, turning, or drilling.”
So, it comes as no surprise that the additive manufacturing process is also becoming increasingly popular in sensor technology. Being able to handle electronics and housing and to physically test the interaction of these components is much more informative than seeing a simulation on the computer. In Puchheim near Munich, our engineers even initiated a new manufacturing process and are now able to create pressure channels three-dimensionally within solids. And in Berlin-Weißensee, where complex sensor systems are created, the experts are also happy about structures that could not be produced otherwise – such as a product-specific vacuum pipette.
Digital development assistance
Does this mean 3D printers are the future of sensor production? “In sensor technology, we can make use of more complex housing or components, and the manufacturing possibilities offered by 3D printing in series production are rapidly evolving,” says system expert Roman Schmidt.
With an advanced printing process and more flexible materials, production of certain elements has become simpler. “Highly complex silicon chips cannot yet be manufactured using 3D printing techniques, but sensors are already being embedded in 3D printing. Simple sensor structures can even be printed completely. There will be even more possibilities in the future. It might even be possible to print circuit boards, tiny metallic components, and new materials such as glass in series production.”
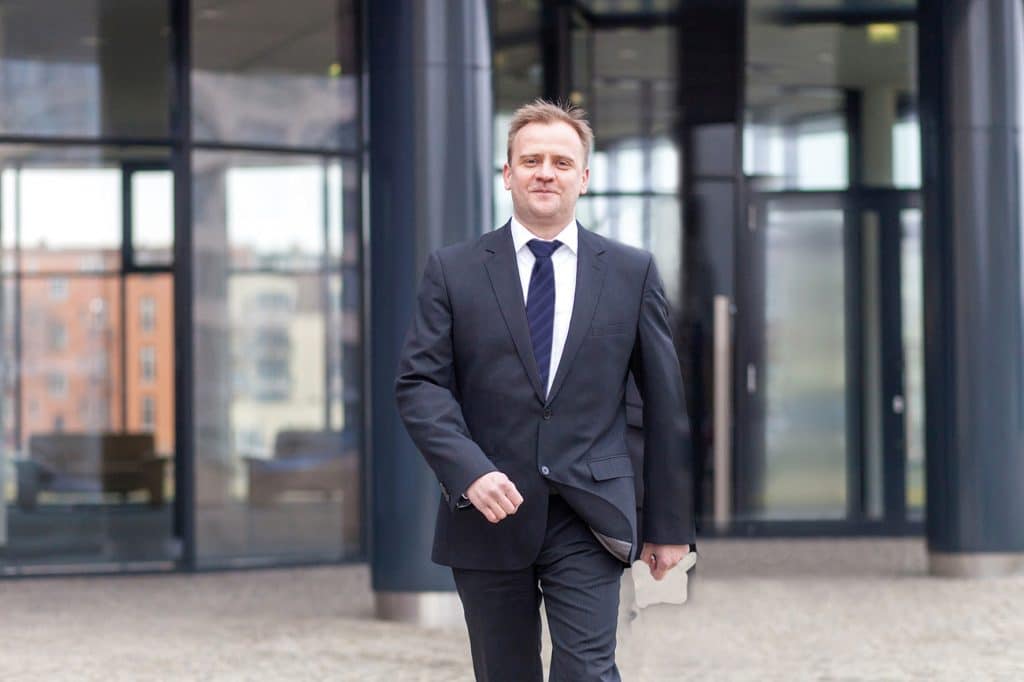
Still a long way to go
However, it is likely to be a few more years before 3D printing can be used in large-scale sensor production. Another important point is the improvements in printing technology. For example, depending on the size required, it can take many hours to print all of the thin layers needed to create a finished object. However, the materials that are suitable for 3D printing are becoming more diverse every day and some of them are already as resilient and reliable as the conventional materials used for mechanical processing or injection moulding.
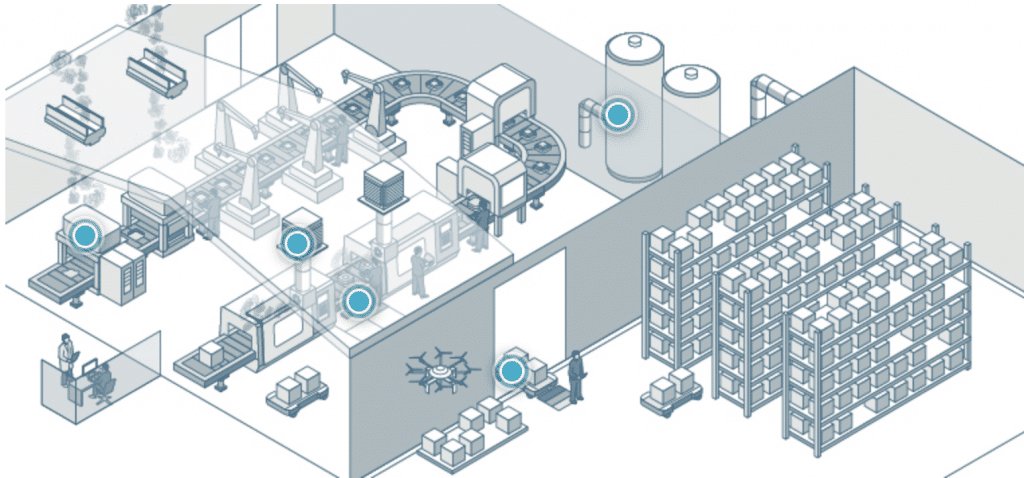