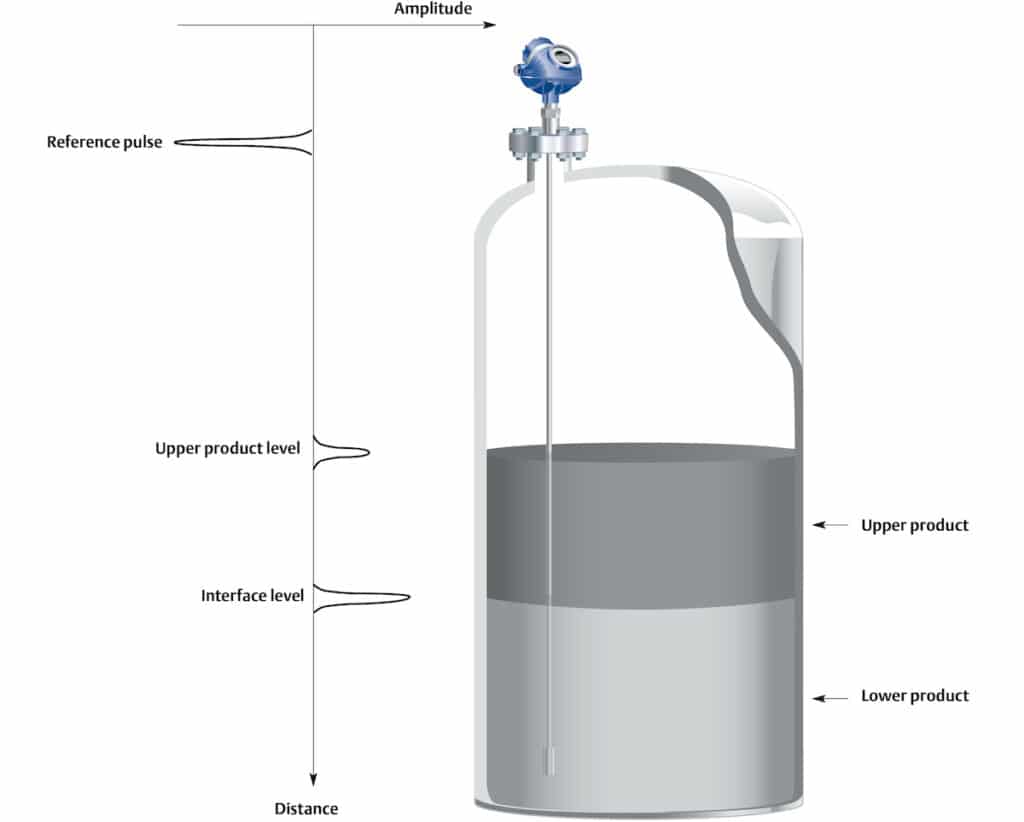
Accurately measuring the interface point helps in separating the liquids as efficiently as possible, so that cross-contamination can be avoided when the liquids flow out into independent channels. Should cross-contamination occur, it can prove extremely costly. The oil industry provides a good example of this, as oil reaching the water tank at a multiple well pad facility could cost over $1 million a year in lost revenue.
However, achieving accurate interface detection can be challenging as it depends on process conditions such as the dielectric constant of the liquids, and the presence of a distinct interface between the layers. The liquids will usually separate naturally because of their differing densities, with the lower density liquid settling on top of the higher density liquid.
In a vessel containing oil and water, for example, the oil will float on top of the water, with the interface point being the upper level of the water and the lower level of the oil. There can be occasions when the liquids do not separate entirely, with an emulsion layer (i.e., a mix of the two liquids) forming between them. The thicker the emulsion layer, the more challenging it becomes to accurately detect the interface point.
Technology options
The most straightforward way to detect an interface point is through a sight glass on the side of a vessel, but this basic method requires operator inspection, and is therefore labour-intensive and time-consuming. Also, sight glasses require regular maintenance and in certain applications, condensation may prevent an operator from detecting the interface accurately. Alternative technologies include floats and displacers, capacitance transmitters, differential pressure transmitters, and magnetostrictive sensors. However, these can also have limited accuracy and reliability in certain process conditions, and their maintenance and calibration requirements can be complex.
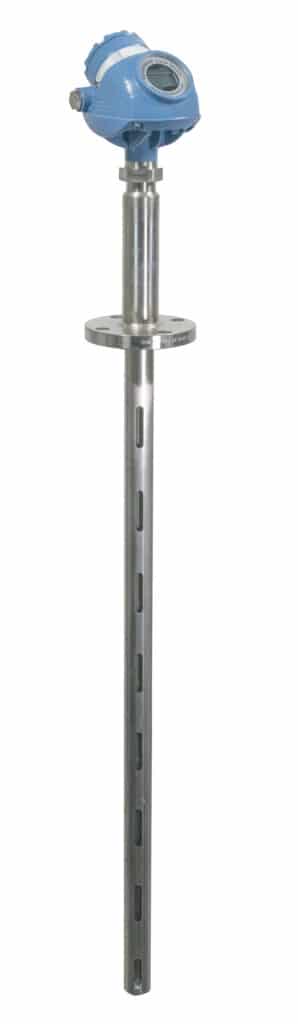
Guided wave radar
Guided wave radar (GWR) is a field-proven and widely-applied technology in interface detection applications. GWR transmitters deliver a top-down, direct measurement of the distance to both the top liquid surface and the interface point, and provide many advantages compared to other technologies. Changes in pressure, temperature and most vapour space conditions have no impact on their accuracy, and no compensation is required when there are changes in dielectric constant, conductivity or density. GWR transmitters are easy to install, require minimal maintenance, and their advanced diagnostics quickly alert operators to any degradation in performance.
Detecting an interface point
GWR technology is based on the time domain reflectometry principle. A pulse of microwaves is guided along a probe that is submerged in the process media. When the pulse reaches the surface of the upper liquid, a significant proportion of the microwave energy is reflected back to the transmitter. The time difference between the generated and reflected pulse is converted into a distance from which the level is calculated. As a proportion of the pulse continues down the probe through low dielectric fluids, a second echo can be detected from the interface point between the two liquids.
Dielectric constant
The speed of travel of the pulse – and therefore the accuracy of the interface point detection – depends on the dielectric constant of the two liquids. Top-down GWR transmitters are suitable for use in interface detection applications only if the upper liquid has a lower dielectric constant than the lower one, and if there is a difference between the two dielectric constants of at least six. In an oil and water application, water has a significantly higher dielectric constant than oil, so the interface point can easily be detected by a top-down GWR transmitter.
In applications where the upper liquid has a higher dielectric constant than the lower one, this prevents a top-down interface detection using GWR. However, in such instances the positioning of the transmitter can be inverted, with the device mounted on the bottom of the vessel to enable interface detection.
Emulsion layers
Depending on their composition, some emulsions can break down into two distinct layers when given time to settle. In these applications, installing a GWR transmitter in a calm, still area of the vessel, where the layers have a chance of breaking down, may enable interface detection. Also, the use of a stilling well can help to achieve better product separation.
Measuring a thinner upper layer
When using a GWR transmitter in an interface detection application, the upper liquid layer must be of a certain minimum thickness to enable the device to distinguish between the signals reflected from the two liquids. This minimum thickness has typically varied between 50 and 200 millimetres, depending on the transmitter model and probe style. However, the Rosemount™ 5300 Level Transmitter from Emerson provides functionality that enables the minimum detectable thickness of the upper liquid layer to be reduced to 25 mm.
This significant enhancement has been enabled by a new software algorithm that allows the transmitter to detect signal peaks that are closer together without having to decrease its signal bandwidth and therefore reduce its high sensitivity and its ability to handle disturbances. Being able to detect a thinner top liquid layer helps to prevent unwanted product ingress and optimises the performance of the separation process, helping end users maximise operational efficiency and increase profitability.
By Denny Nelson, solutions engineer at Emerson.