Especially hearing-sensitive underwater animals such as whales or any other mammal species suffer enormously from the noise pollution that occurs during the construction of offshore facilities such as oil platforms, wind farms but also research platforms. The drilling and hammering create a noise pollution under water which you cannot imagine. Due to the higher speed of sound, especially in salt water, the sound spreads better, faster and over a larger area. The sensitive marine life suffers extremely here.
The underwater sound protection is generated by an air bubble system, which is fed by a compressor station, this is located for example on a boat or the offshore park itself. Up to 24 compressors feeding compressed air simultaneously are not uncommon. The bubble curtain dampens the sound underwater and provides an environmentally friendly noise protection.
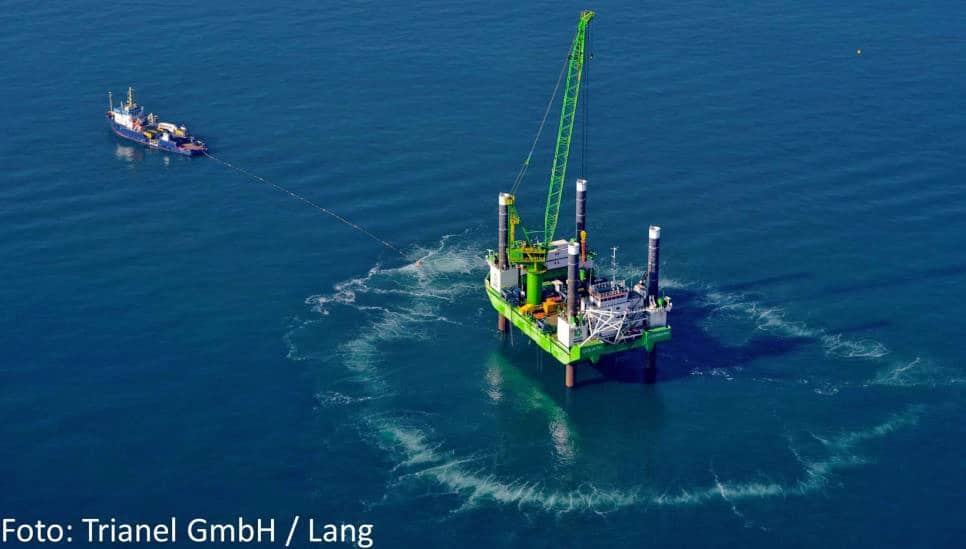
In the left picture, the boat on which the compressor station is located can be clearly seen next to the bubble curtain. It is easy to imagine that enormous amounts of energy are needed for such a bubble curtain, an optimized gas supply can therefore bring a great cost advantage. A monitoring of the compressed air consumption is more than recommendable.
Since the required compressed air is gassed directly into the sea, it must be obligatory oil-free, otherwise the noise protection would represent an even greater danger for flora and fauna, the oiling of the world’s oceans.
For optimal underwater noise protection, we recommend:
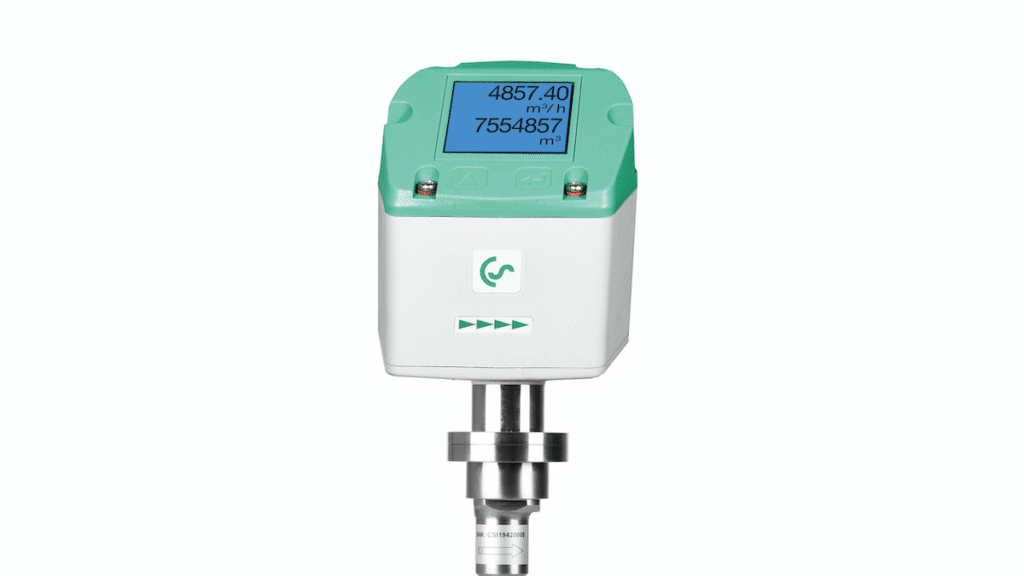
VD 500 – Flow meter for FAD measurement
The integrated, precise differential pressure sensor measures the differential pressure/ dynamic pressure at the sensor tip. The pressure depends on the respective gas velocity. The flow is therefore easy to determine by means of the pipe diameter.The additional measurement of temperature and absolute pressure and calculation of the relevant density means that measuring can be carried out for various gases, a wide variety of temperatures and pressures.
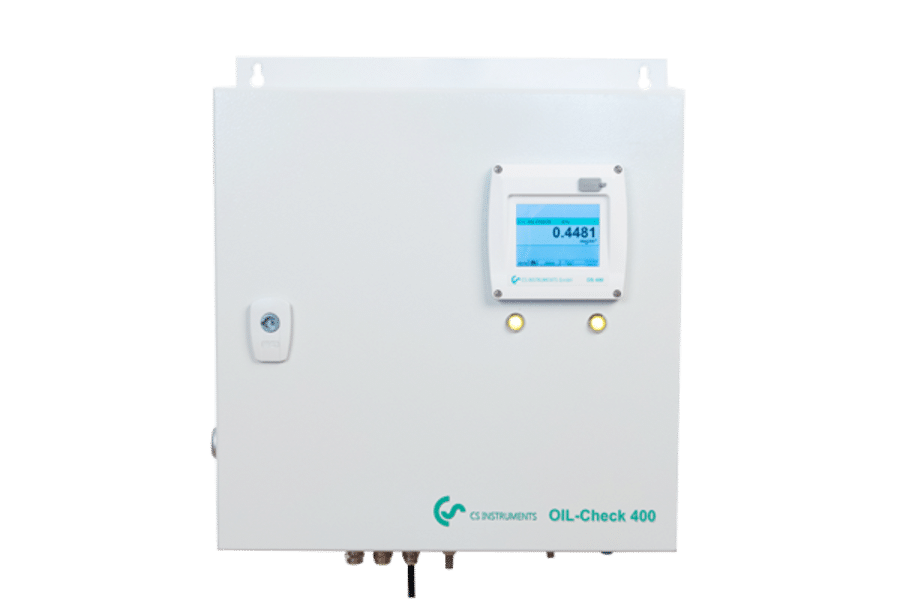
DS 400 – Residual oil content measurement OILCHECK according to ISO 8573
The residual oil content sensor OIL check measures the vaporous residual oil content in the compressed air. By means of a sample taking a representative part volume flow is taken from the compressed air and led to the OIL check. Due to the continuous measurement threshold value exceeding will be recognized immediately and remedial actions can be initiated to ensure oil-free compressed air.