As they have a low conductivity, there is a very high risk of electrostatic charges during the many different processes. Regular checks and documentation are required to safely manage and control these work steps and thus avoid charging. MBA Instruments, the specialist for conductivity measurement, has taken up this challenge and developed the MLA1000 meter which quickly and continuously delivers exact measurement results so that effective measures can be taken to prevent electrostatic charges. Strictly designed in accordance with the German TRGS 727 Technical Rule, the meter ensures the safe transport of light mineral oils to their destination.
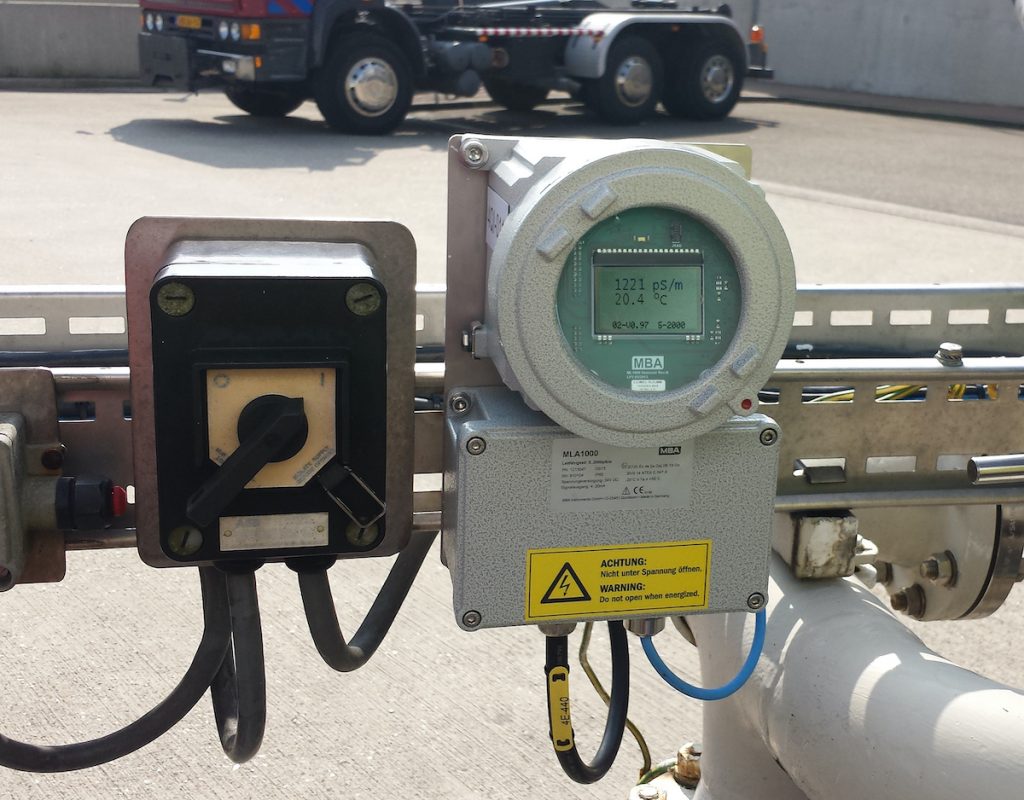
Jet A-1 type kerosene often has to cover a distance of several hundred kilometers in pipelines from the tank farm to its destination at the airport. Safety is at a premium here: as petroleum products such as kerosene have a low conductivity, they can be particularly easily electrostatically charged at high flow rates, which, in the worst case, may result in a fire in storage tanks, tank trucks or aircraft tanks. To prevent this from happening, accurate and regular measurements in the tanks and pipes are crucial.
Safety first: TRGS 727
The parameters for the safe handling of liquids are laid down in the German Technical Rules for Hazardous Substances “TRGS 727, Avoidance of ignition hazards due to electrostatic charges”, which are published and continuously updated by the Federal Institute for Occupational Safety and Health. These rules apply “to the assessment and avoidance of ignition hazards due to electrostatic charges in potentially explosive atmospheres and to the selection and implementation of protective measures to avoid these hazards”. TRGS 727 replaces and updates TRBS 2153 (“Avoidance of ignition hazards due to electrostatic charges”).
How liquids charge up
When a liquid flows through a pipe, electrons are displaced by friction within the liquid and at the inner pipe wall, whereby potential differences of up to several 1,000 volts may occur. The surface resistance of the pipe, the conductivity of the liquid and the flow rate are the main factors that determine the resulting charge quantity of the potentials. An excessively large charge quantity in the system may result in electrostatic discharge in the form of microsparks or spark discharge. Kerosene may ignite if the charges are particularly high and multiple discharges are possible as a result. To reduce the risk, a constant measurement of the conductivity and the use of certain additives is necessary. There are different ways of checking conductivity: mobile by hand, or stationary or automatic, by individual or continuous measurements. MBA Instruments offers devices for both cases: The MLA900 performs individual measurements to check, for instance, if the necessary conductivity has been achieved by adding sufficient additives. Its extension – the MLA1000 – is firmly attached to the tank, continuously monitors conductivity and temperature and, if necessary, automatically sends a signal to a pump for additives. Both meters are ATEX-approved and meet the requirements of the Technical Rules for Hazardous Substances (TRGS 727).
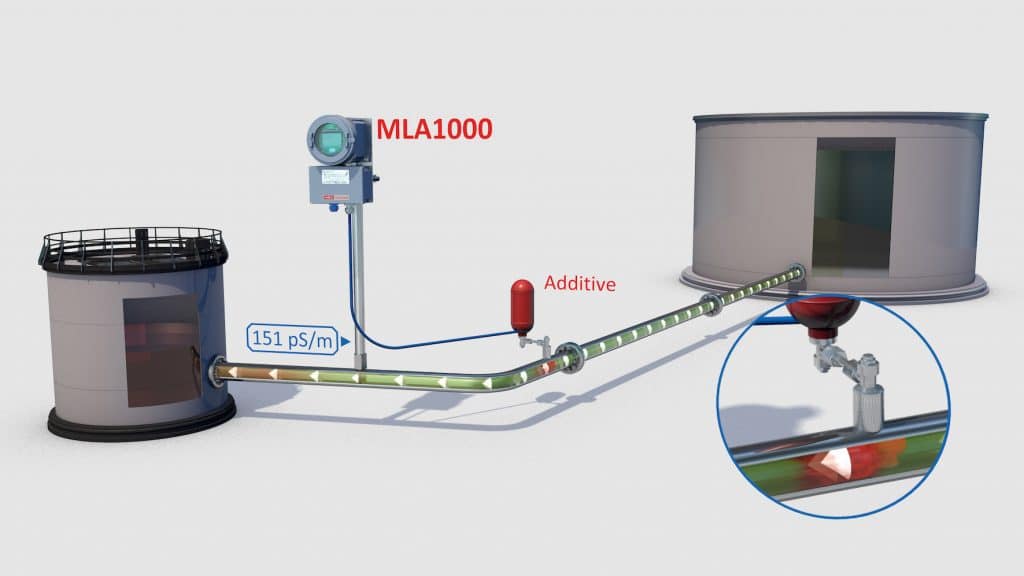
Countermeasures to ESD
To control the conductivity of liquids such as light mineral oils, it is common practice to use antistatic additives. These help to quickly dissipate electrostatic charges – by safely discharging them to the tank or pipeline wall – or even prevent them from occurring at all. Many airports have set the conductivity value at 300-600 pS/m to ensure safe fuel transfer, e.g. from the pipeline to the aircraft tank. But the principle of “as much as necessary, as little as possible” also applies when it comes to using additives. In many cases, concentrations in the ppm range are sufficient.
Besides the use of additives, the temperature also has a significant influence on conductivity – the higher the temperature, the higher the conductivity of the oil. As the measurement of conductivity must always be considered in connection with the temperature, the meters from MBA Instruments also supply the temperature value: both the MLA900 and the MLA1000 simultaneously measure the conductivity and the temperature. However, it is unfortunately not possible to deduce the conductivity from the temperature.
The solution: reliable conductivity measurement using the MLA1000
The MLA1000 meter from MBA Instruments GmbH meets the demand for safety through conductivity and temperature measurement as well as the automatic and precise use of additives and strictly complies with TRGS 727. It is therefore no surprise that the MLA1000 is already being used at numerous tank farms and many European airports. “In close cooperation with our customers from a wide variety of sectors, we have developed a groundbreaking system which fully automatically documents and stabilizes the conductivity value,” says MBA Managing Director Andreas Heckel.
The MLA1000 performs a conductometric measurement of the electrical conductivity. The conductivity of the light mineral oil is precisely set and continuously maintained at the set value by the MLA1000 in a control loop.
At 0-2,000 pS/m, the measuring range for conductivity in kerosene, measured in pS/m (S = siemens as the reciprocal of the resistance), is extremely low. In the further development to a continuously working variant of this measuring technique – the MLA1000 measuring system – various physical details had to be considered. For instance, polarization effects occur on electrodes after a short time of measurement. To obtain reliable, continuous measurements, two physical disciplines were therefore metrologically linked: electronics and flow dynamics. The meter uses the flow rate within the pipeline. While there is a comparatively strong flow between 0.5-7 m/s within the pipeline, the small size of the inlet and outlet openings reduces the flow rate within the measuring probe. The resulting laminar flow between the two electrodes within the probe leads to a permanent degradation of the polarization and thus to a highly accurate measurement of conductivity and temperature. The developers from MBA Instruments GmbH were thus the first to realize the continuous measurement in a flowing medium in a pipeline. The geometry of the sensor ensures a laminar flow within the sensor and thus permit trouble-free, fast and reliable measurement.
This method allows the additives used to prevent electrostatic charging and sparking to be controlled extremely accurately and in the right quantity to ensure that the oil does not become too “contaminated”.
Even greater safety
To ensure reliable and accurate measurement, the MLA1000, too, is subjected to a function check, which is carried out by applying a magnet that closes a test contact and thus generates a given display value. The additional and optional use of a sliding sleeve allows the probe to be disassembled during pipeline operation.
Advantages of the MLA1000

Andreas Heckel, Managing Director of MBA Instruments GmbH, attaches particular importance to the quality aspect of this measurement technology: “Continuous conductivity measurement primarily guarantees the constant quality of the light mineral oil by continuously documenting it and certifying this to the customer. Every step within a process is extremely safe, not least thanks to compliance with TRGS 727, and is subject to constant control.” The MLA1000 makes it possible to continuously monitor the conductivity of the light mineral oil and, by automatically feeding additives into the pipeline, manage it accordingly so that the customer’s desired and set value can be maintained and documented. This gives the certainty of delivering a shipment that has been tested in its entirety and can be certified with regard to the conductivity parameter at this stage of the supply chain. By monitoring the conductivity of kerosene, airports, pipeline operators, refueling companies and the like can improve the safety of fuel transports while at the same time reducing the use of additives.
SMB International and MBA Instruments: the material handling specialists for automation and instrumentation
The SMB Group in Quickborn develops sophisticated system solutions for worldwide use. SMB International is a leading planner, developer and manufacturer of highly complex, automatic loading and unloading systems, filling systems, palletizers, conveyors, compact storage systems and ship loading systems. MBA Instruments is a specialist for digital level measurement technology and conductivity measurement in light mineral oils such as kerosene.
Both companies deliberately rely on a high share of in-house production at their location in Quickborn near Hamburg. Customer requirements can thus be met quickly, in a targeted manner and at consistently high quality. The companies’ own design and production facilities provide the basis for their high manufacturing depth which permits the timely delivery of high-quality products. The company’s service teams work on large-scale projects both nationally and internationally. The distribution network, which has operations worldwide, ensures swift and effective information-sharing and coordination.