A major mining company in Peru faced the challenge of selecting a reliable point level measurement for a silicon hydration reactor. This reactor, essential for the production of silicon compounds, operates under complex conditions: the system involves a process temperature of 120°C and intense steam. The dimensions of the container are 2 metres in height and 5 metres in length. Fernando Soares Pinto, Sales Director for Latin America/Iberia of the UWT team in South America, was tasked with finding a sensor that could withstand the harsh conditions while providing precise and reliable measurement results.
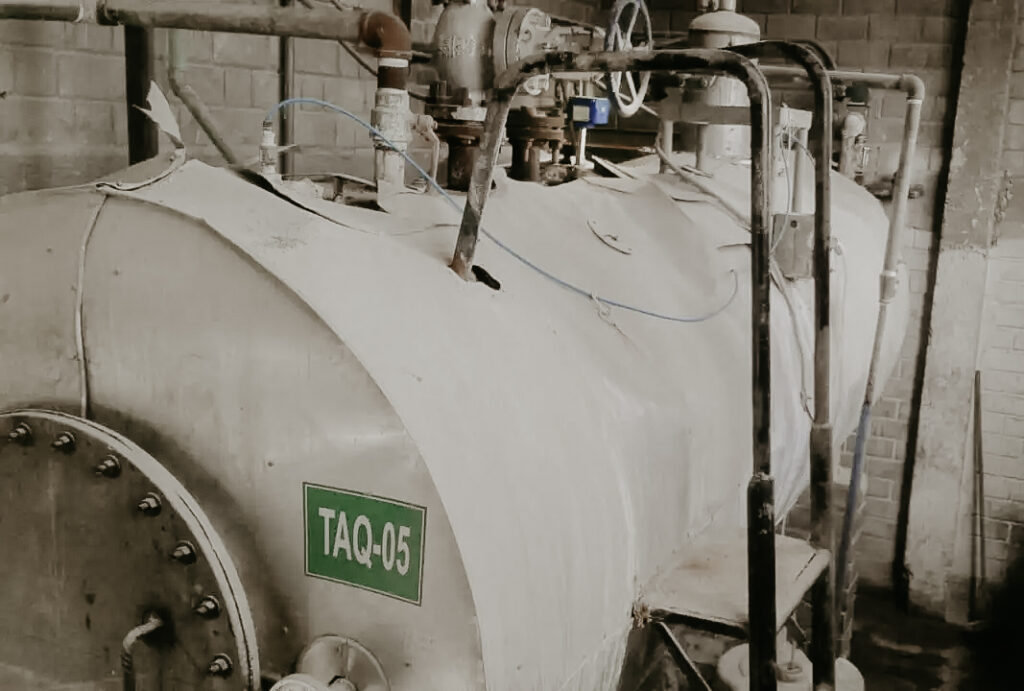
Point level sensors for capacitive measuring systems offer a wide range of solutions for applications in media such as liquids, pastes, foams and slurries. These sensors can be integrated into a wide variety of container types, whether they are made of metal or non-metallic materials. The precision of the capacitive level switches extends to both conductive and non-conductive media. The importance of the capacitive measuring principle is proven, as it delivers precise and reliable results even under demanding process conditions. The flexible application options and high measuring accuracy make capacitive point level sensors an ideal solution across a wide range of industrial applications.
Robust sensor with capacitive RF technology for demanding conditions
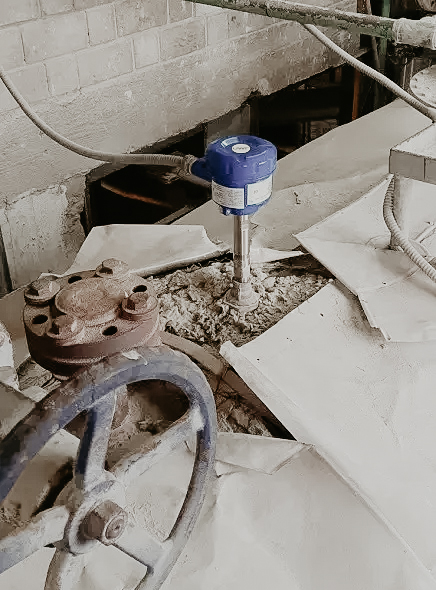
The UWT solution for this complex application was the RFnivo® 8100 capacitive level switch. This sensor is specially designed for process temperatures of up to 200°C and process overpressures of up to 35 bar. Its robust design, in which both the probe and the FKM seal in contact with the medium have a high chemical resistance, makes the RF 8 the first choice for this application. The FKM seal is also highly thermally resistant and prevents any gas or liquid ingress.
How the RFnivo® fulfils the requirements in a silicon hydration reactor
In a silicon hydration reactor, conditions prevail that pose a major challenge for conventional sensors. The process generates intense vapour and condensation often forms around the process connection. In addition, sensors must be able to work reliably at high temperatures and under high pressure.
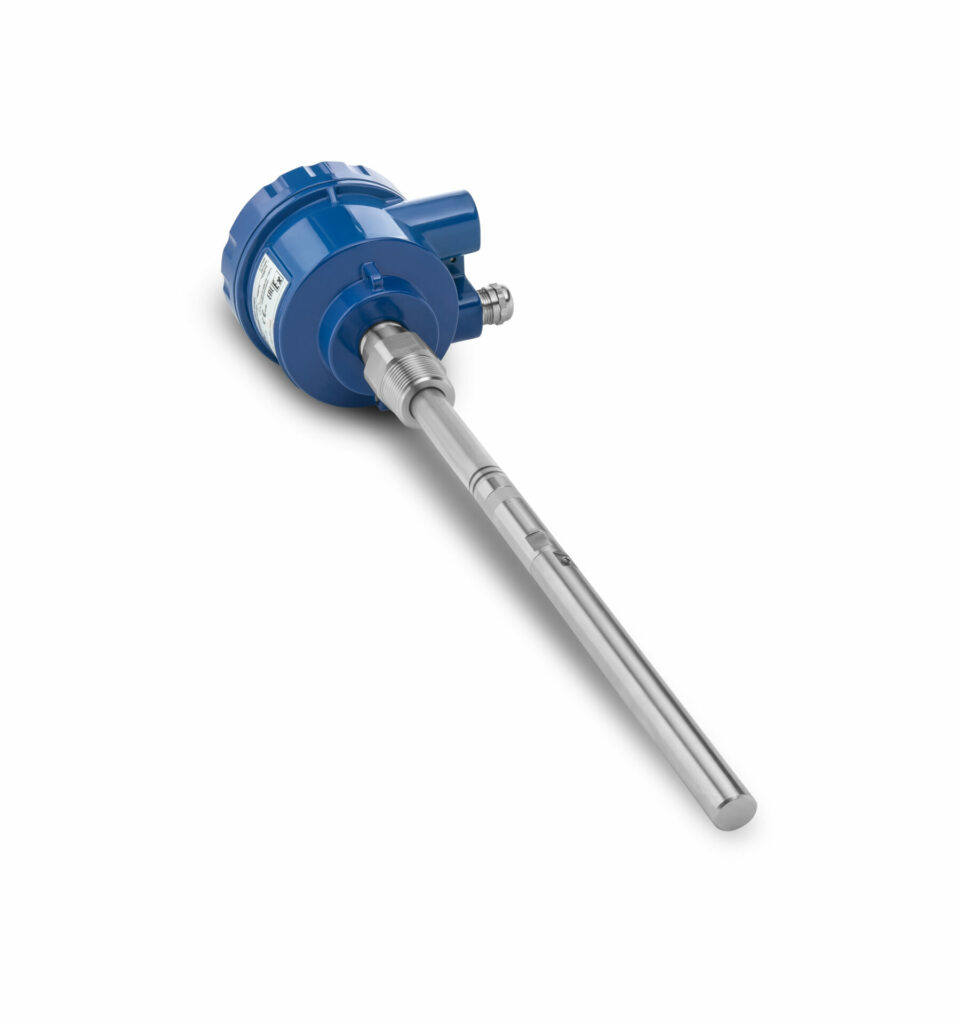
The RFnivo® 8100 masters all these challenges thanks to its innovative technologies and robust design:
Active Shield Technology: This technology ensures that condensate forming around the process connection has no adverse impact on the measurement result. The sensor remains insensitive to adhering media and thus guarantees precise measurements even under constant vapour influence.
Inverse Frequency Shift Technology: This method enables the sensor to deliver precise measurement results even under widely varying process conditions. It ensures that the sensor is able to accurately measure the DK value of the medium, which is essential for precise level detection.
What makes the RFnivo® with the high-frequency signal so special?
The RF 8 is characterised by several important features that make it particularly suitable for the most demanding applications:
- Temperature resistant: Depending on the version, the sensor has a process temperature range of -40°C to +400°C, which makes it ideal for applications in hot water and steam environments, among others.
- Pressure-resistant: With a pressure resistance of up to 35 bar, the RF 8 can also be used in extreme operating environments.
- Chemical resistance: The FKM seal offers excellent media resistance and prevents any gas or liquid ingress, which is particularly important in chemically aggressive environments.
- Maintenance-free: The sensor is virtually maintenance-free and offers a warranty of up to 6 years, which significantly reduces operating costs.
- Versatility: The RF 8 can be used as a full, demand and empty detector in all liquids, including viscous liquids, from a DK value of 1.5, making it a universal tool for a wide range of applications.
Implementation of the full detector for precise monitoring
The installation of the RFnivo® 8100 in the Peruvian mining company’s silicon hydration reactor went smoothly. The sensor was installed as a full detector from above in the steel tank in order to precisely monitor the maximum fill level. Thanks to the sensor’s robust design and reliable technology, the company was able to ensure continuous and accurate monitoring of the reactor level.
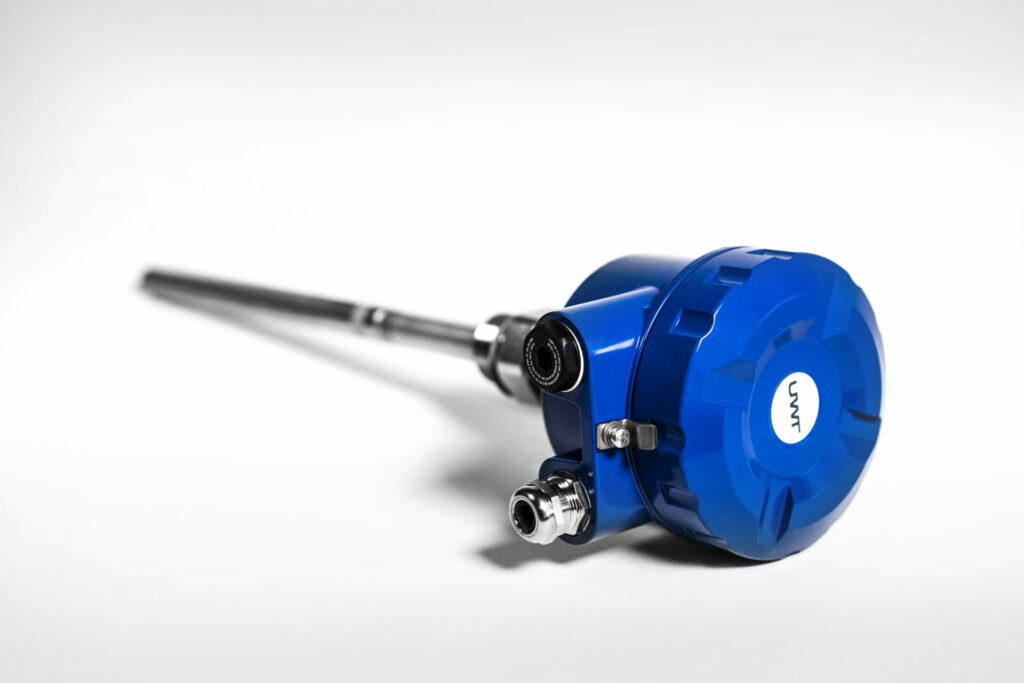
The Active Shield technology proved to be particularly advantageous as it completely eliminated the problems associated with adhering condensate. This ensures significant measurement accuracy and reliability, even with constant vapour build-up above the probe.
Thanks to the UWT solution, the company was not only able to improve the efficiency and safety of its processes, but also reduce operating costs through the maintenance-free operation of the sensor. The RFnivo® 8100 has proven to be an excellent choice that more than fulfils the requirements of the demanding application.