It relies on the unique physical properties of water above the critical point (above 378 °C and 22.1 MPa) to accomplish these tasks. Part of the appeal of supercritical water is that it is an environmentally benign organic solvent.
At the same time, supercritical water gasification is largely developmental. Research involving the technology often includes complex factors, such as difficult pressure control scenarios. This case study shows how a dome-loaded multiple orifice back pressure regulator was able to provide a fluid control solution for research involving a continuous flow supercritical water reactor.
Background
As a PhD candidate working in Professor Igor Novosselov’s laboratory at the University of Washington, Brian Pinkard worked to design and fabricate a continuous flow supercritical water reactor for the destruction of chemical waste.
While supercritical water gasification has been studied extensively at the laboratory scale in batch style reactors, the technology is now transitioning toward continuous flow reactors to improve economic efficiency and move toward market competitiveness. A continuous flow reactor has numerous benefits over its batch style counterpart, including smaller footprints, tunable process parameters, opportunities for in situ process monitoring, and higher reactant throughput.
Supercritical water reactors typically rely on back pressure regulators to achieve pressure control within the reactor. In most cases, the regulator operates in tandem with a constant mass flow rate pump supplying pressure at the front end of the system.
The Challenge
When determining decomposition rates, establishing precise reaction residence times is crucial. Precise pressure control in the supercritical water reactor allows the establishment of precise residence times in the reactor section, which in turn allows the generation of accurate chemical kinetic data for various test compounds. Having precise and consistent pressure control is especially critical at low flow rates.
Pinkard and his fellow researchers faced high temperature and high pressure process conditions as well as the need for extreme accuracy at low flow rates. This combination of challenges led them to explore options other than traditional back pressure regulators to control the internal pressure of the supercritical water reactor.
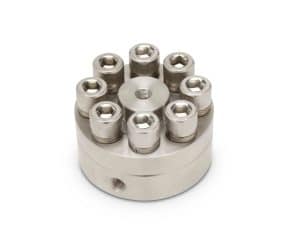
They contacted Equilibar, an engineering and manufacturing company that specializes in difficult fluid control applications, to discuss a radically different type of dome-loaded back pressure regulator that uses a diaphragm covering a field of parallel orifices. As fluids flow through the unit, the diaphragm lifts off the orifices to release pressure. If flow is minimal, as in Pinkard’s situation, only a portion of one orifice will open to release the pressure. These devices do not rely on springs or traditional valve seats, but rather use a direct 1:1 gas pressure on top of the diaphragm to maintain stability across a wide flow range.
Because the regulator body and diaphragm can be made from a wide range of materials, Equilibar back pressure regulators offer the unique advantage of providing precise pressure control at extremely low flow rates while also being capable of handling extreme process conditions, including high temperatures.
The Solution
Equilibar engineers helped determine the best back pressure regulator design and components to meet the needs of the supercritical water reactor. They recommended an Equilibar® U6L Ultra Low Flow Series Precision Back Pressure Regulator with a PEEK diaphragm and Kalrez O-Rings.
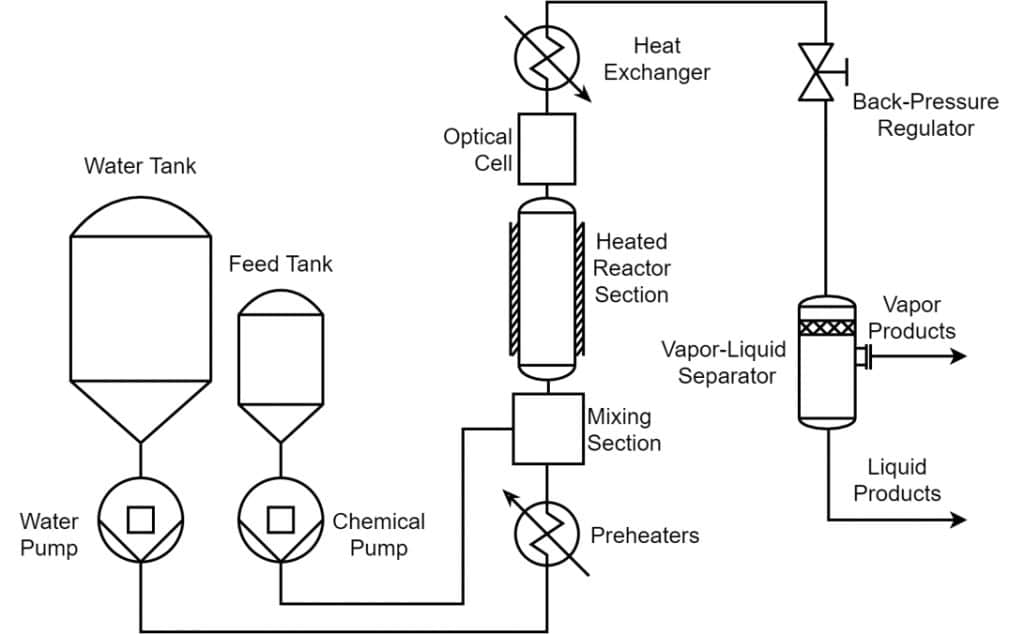
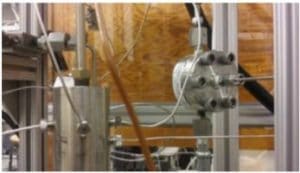
Equilibar’s U6L Research Series High Pressure Ultra Low Flow Back Pressure Regulator was originally designed to meet the demanding requirements of catalyst research and high pressure reactor control applications. It will hold stable pressure across extremely wide flow ranges and can handle liquids, gases, or multi-phase mixtures.
Equilibar Research Series units are 1:1 dome-loaded, meaning that a pilot pressure must be supplied to the dome of the regulator equal to the desired setpoint. This pilot pressure can be supplied by a manual gas regulator or by an electronic pressure regulator for automated control. The Ultra Low Flow UL Series uses a single outlet orifice design.
The U6L has performed admirably across a range of flow rates and set pressures and is an essential and reliable component in our supercritical water reactor system. The unit was easy to install and is straightforward to operate.”
Pinkard
About Novosselov Research Group
The Novosselov Research Group at the University of Washington conducts multidisciplinary research in the areas of combustion, aerosol science, supercritical fluids, and fluid dynamics.