Challenge
The brewery was extending its lines and needed a valve that could not only meet its rigorous production demands, but could minimize water hammering, ease maintenance and provide production flexibility while supporting their sustainability goals. It had a range of competitor valves on-site but none of these valves met all the requirements.
Sustainable Solution
Engineered for reliability, the D4 valve was recognized as the solution to meet their needs. The brewery was concerned about water hammering which can cause pipe vibrations that spur leaks and damage equipment. Fully-balanced in open and closed positions, the D4 valve provided dependable operation against water hammer events enabling flow in any direction without slamming and safe maintenance. The design also eliminates the need to apply live air during removal and installation of the valve for maintenance purposes.
In order to achieve its sustainability goals, the brewery wanted to reduce its CIP cycle. The D4 mix-proof valves enabled the brewery to conduct extensive cleaning of product contact surfaces and reduce operational costs by minimizing the use of CIP fluids during cleaning cycles. This is due in part to the internal geometry
and fabrication of SPX FLOW valves, which are designed to optimize the CIP fluid rate and the associated chemical / waste disposal costs. Figure 1 shows the CIP fluid use for SPX FLOW valves vs. other leading brands.

Product Safe Design with Improved Standard Option
One of the main goals the brewery wanted to achieve was a fully-automated process system that could ensure safety and integrity of all process fluids while maximizing production capabilities. Brewery operators were immediately drawn to key design areas of the D4 mix-proof valve that would help them achieve their goals:
- A fully-balanced, mix-proof valve design was deemed to be important as it resists hydraulic shock created by pressure spikes and high flow velocities. This fully-balanced design also enables bi-directional flow creating more freedom within the process, a benefit given their longer-term plans for process expansions.
- Secure Position feedback on all four positions. The brewery’s experience with competing valves was they lead to false and nuisance alarms due to the external switches and cabling that were susceptible to snags and natural vibrations during operation. The D4 was selected given its protected design that was found to reduce potential false alarms.
- The D4 was also selected due to its enhanced sanitary features. The D4’s leakage chamber, which is larger than most other competing mix-proof valves, was found to eliminate buildup / blockage that can compromise the process fluid’s integrity. The brewery chose the leakage chamber flush option which is a standard feature that promotes product safety by keeping the vent area clean.
Safe and Easy to operate and maintain
A major benefit for the brewery is the D4 series’ ease of maintenance, with downward opening valves, inserts weighing up to 40% less than competitor and cavity spray as standard the valves are easy to maintain. All sensors are pre-wired in the control unit, and all electrical parts are internal so there are no external cables, meaning there is less hazardous fluid needed during CIP and as a result less waste fluid and risk of electrical shock minimizing labor and safety risks during washdown. This has saved the brewery time and money while reducing the total cost of ownership.
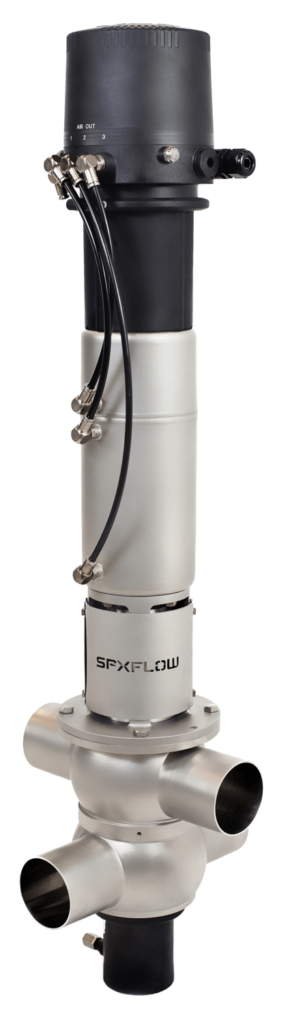
Maintenance crews were impressed to learn that a jacking screw can handle quick maintenance procedures, so no compressed air or lifting tools are required for removal and service, which eliminate potential pinch and ergonomic hazards.
They also appreciated that fewer parts needed to be kept on hand given the standard seals across various D4 product sizes and configurations – there are only two sizes across the entire range and replacement inserts can easily be upgraded.
Operation personnel were advocates for these valves as well. They commented the slim stainless actuator, which is fully enclosed, prevents fluid ingress and the open yoke design reduces heat transfer from the product zone into the actuator. They were also very impressed by the guards that serve to protect personnel during actuation, eliminating potential pinch hazards.