In order to keep the production processes running, these components must be permanently available. This requires accurate filling level measurement. In order to continuously monitor the fill level of the barrel pump, wireSENSOR WDS-P60 draw-wire sensors from Micro-Epsilon are used.
Consumables such as greases, silicones and pastes must be continuously available in numerous production lines. This task is performed by barrel pump systems, which squeeze these consumable components out of a barrel via a hydraulic pressing system. In order not to interrupt the industrial production process, it is absolutely necessary to replenish the fill level of the barrel before the old barrel is emptied. For this reason, the optimum time for replacement must be apparent and planned for at an early stage so that the barrel is not changed too early or too late. Draw-wire displacement sensors from Micro-Epsilon therefore continuously measure the fill level of the barrel.
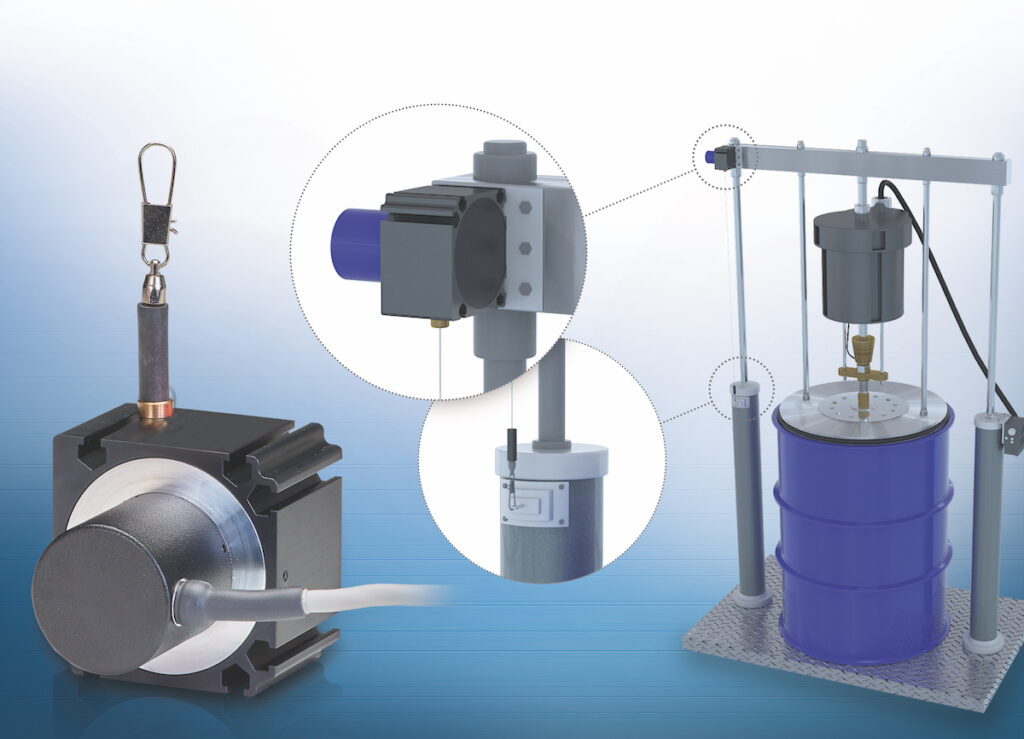
For this measurement task, the barrel stands on the platform of the hydraulic press. There is one hydraulic cylinder each on the left and right. Both cylinders are connected to each other by a cross beam. In the middle of this is a piston which is pressed into the barrel. A wireSENSOR WDS-P60 draw-wire sensor is mounted on the outside of the crossbar. The wire exits downwards and is attached to the base of the cylinder tube. The two outer cylinders are now filled with hydraulic oil and the pistons move slowly down into the cylinder tubes. As a result, the piston is pressed into the barrel at the center of the crossbar and the consumable component is pressed upwards by the pressure created in the barrel. The wire shortens and the sensor thus measures the decreasing lifting height of the cylinder via the potentiometer. Subsequently, the analog output signal is transferred to a controller.
The fill level of the barrel can thus be displayed on a screen in the production monitoring center. This ensures continuous measurement and level monitoring.