Quantifying the Impact
Routine operations – such as product changeovers and cleaning-in-place (CIP) cycles – often result in substantial product loss. With rising raw material costs, increasing tariffs, and tighter regulatory scrutiny, these invisible losses are no longer sustainable for companies aiming to remain competitive and compliant.
Advanced Liquid Product Recovery: The HPS Solution
To address this challenge, many industry leaders are adopting HPS Advanced Liquid Product Recovery Technology, which is a form of “pigging” technology. Unlike traditional methods, this system uses a specially designed projectile (or “pig”) made of FDA approved materials, which is propelled through pipelines by compressed air, nitrogen, carbon dioxide, water, or even the next product batch.
The pig travels through the pipeline – even around bends and elbows – recovering up to 99.5% of product that would otherwise be discarded. The technology includes a range of other components, such as specialist valves, launch and receive stations, automated controls and software and pig detectors to ensure efficient, safe, and hygienic operation. Modern systems are designed for seamless integration with existing infrastructure, minimising operational disruption.
Manufacturers report several advantages, including:
- Significant reduction in product loss: Up to 99.5% recovery from pipelines, even with viscous or high-value formulations.
- Decreased cleaning times and chemical consumption: Up to 70% reduction, supporting both cost savings and sustainability goals.
- Shorter changeover periods: Faster transitions between production batches, boosting overall capacity.
- Lower risk of cross-contamination: Enhanced hygiene and reduced risk of batch compromise.
- Reduced water and effluent generation: Less environmental impact and lower disposal costs.
- Rapid return on investment: Many companies see payback within months due to higher yields and lower waste-handling expenses.
Broader Industry Adoption and Suitability
Pigging technology is widely used not only in pharmaceuticals, but also in food, beverage, cosmetics, and chemical industries. Systems can be customised for different product viscosities and pipeline sizes (typically from 1.5 inches up to 8 inches).
However, pigging is not suitable for powders or diameters less than 1.5 inches, and each installation should be evaluated for compatibility with specific products and processes.
Please note that while it is possible to use pigging with a wide range of liquids, the regulations around certain categories of pharmaceutical product, for example products that are to be injected, may not permit its use. Please refer to your relevant regulations and laws for guidance.
Case Study: Improving Efficiency and Reducing Contamination
A European biotechnology firm recently implemented HPS pigging technology on its silicone gel transfer lines. Previously, thicker products left considerable residue, resulting in waste and increased cleaning requirements. After adopting the system, the company achieved:
- A significant increase in production capacity
- Major reductions in downtime associated with CIP
- Noticeable decreases in product loss and cross-contamination risk
Sustainability and Environmental Impact
By minimising water and chemical usage during cleaning, pigging systems help pharmaceutical manufacturers meet corporate sustainability targets and reduce their environmental footprint. Less waste also means lower effluent treatment and disposal costs.
Complementary Technologies: Liquid Transfer Routing Manifolds
HPS pigging systems often work in tandem with liquid transfer routing manifolds – available in manual or automated configurations like the Automatrix and Rotomatrix. These manifolds enable efficient, error-free transfer of liquids between multiple sources and destinations, reducing manual handling and cross-contamination risks.
By integrating pigging with valve manifolds, manufacturers benefit from streamlined product routing, faster changeovers, and enhanced operational safety – maximising yield and process efficiency in complex pharmaceutical and biotech environments.
Seamless Integration, Rapid Results
Unlike major process overhauls, HPS systems can be integrated with existing infrastructure -often delivering measurable improvements immediately. For many manufacturers, the decision is not whether to implement product recovery technology, but how quickly they can realise the benefits.
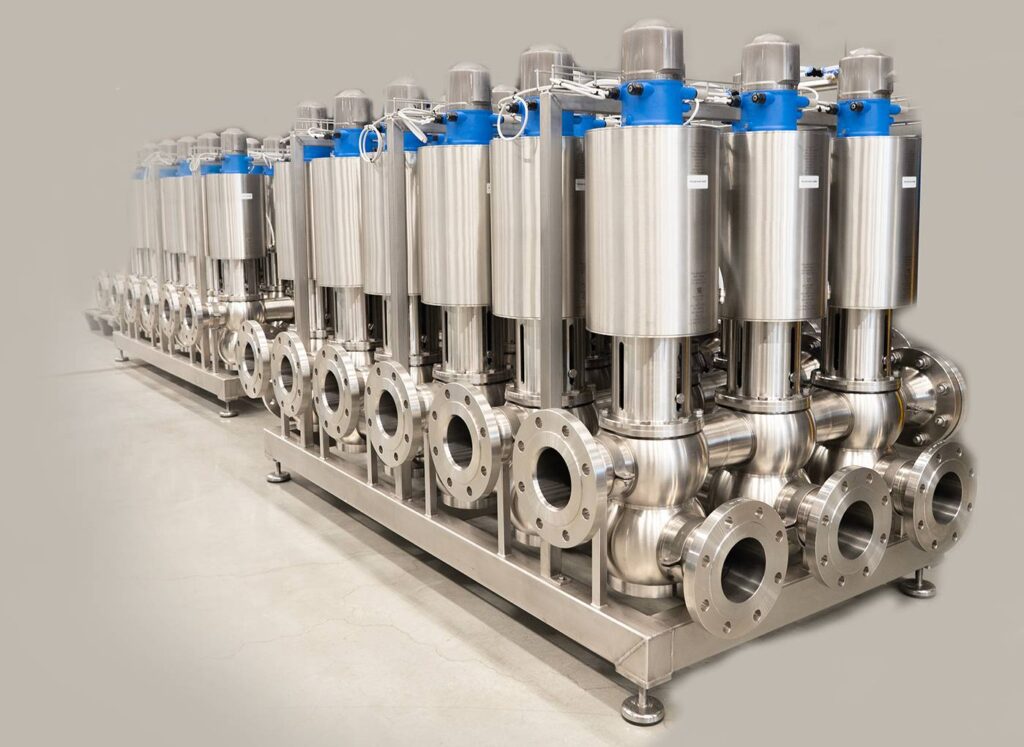
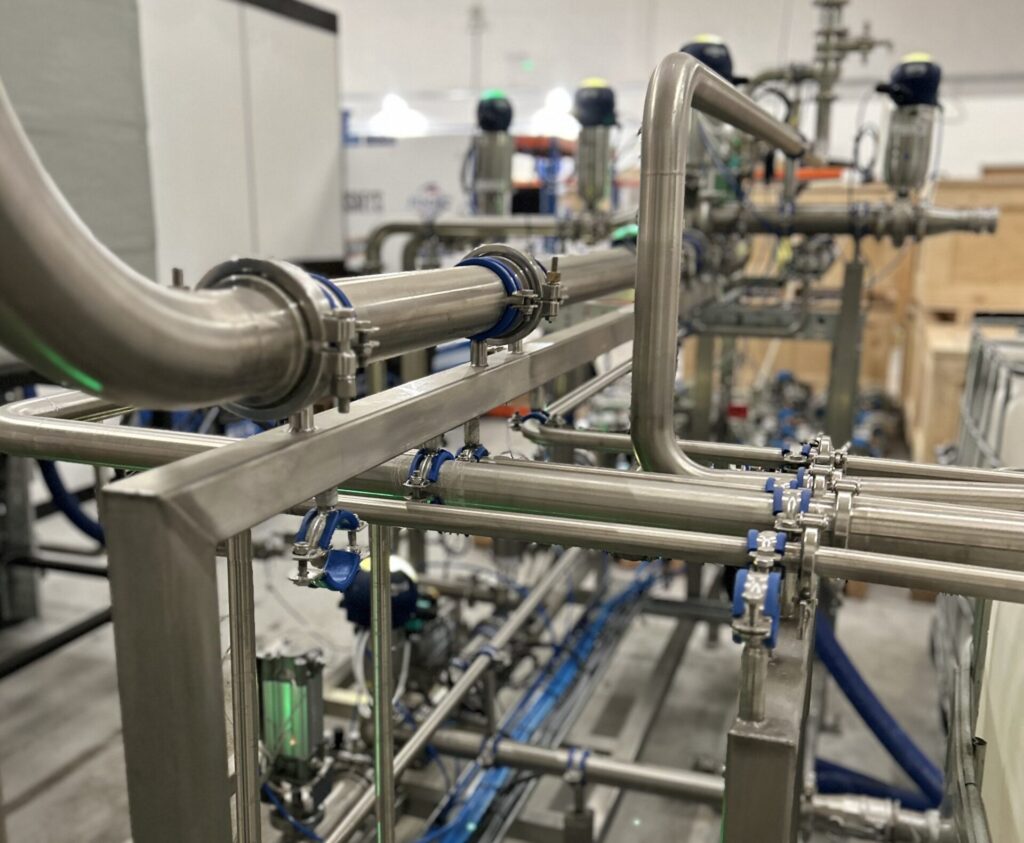
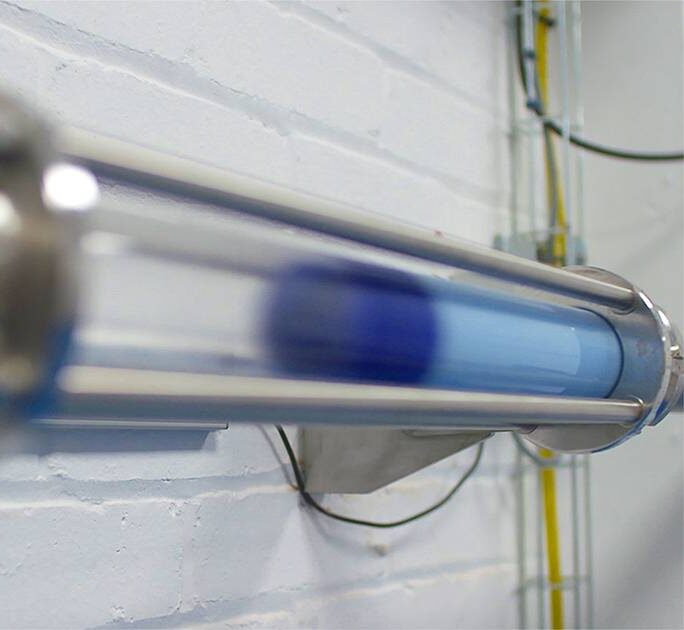