One benefit of EOR is that it lessens the need to create new oil fields in locations that may be environmentally sensitive. Another potential benefit is that it may sometimes be possible to use CO2 captured from power plants to enhance oil production, thereby helping to mitigate carbon emissions. In other situations, chemicals are used to perform EOR.
EOR requires accurate core flooding tests
In almost all EOR research, a core flooding test system is needed to study the performance of EOR methods in the lab before utilizing them in the real oil field. The research is especially complex and difficult because the laboratory tests must apply the same extreme temperature and pressure conditions that are found in the reservoir.
Typically, oil wells produce at a constant pressure condition called bottomhole pressure. To apply this condition in a core flooding test system, a back pressure regulator (BPR) capable of controlling with no fluctuation is required, and it must often be able to withstand extreme temperatures and chemistries. The multiple challenges of these systems often lead researchers to consider non-traditional methods of pressure control. Dome-loaded multiple orifice back pressure regulators can be a good solution.
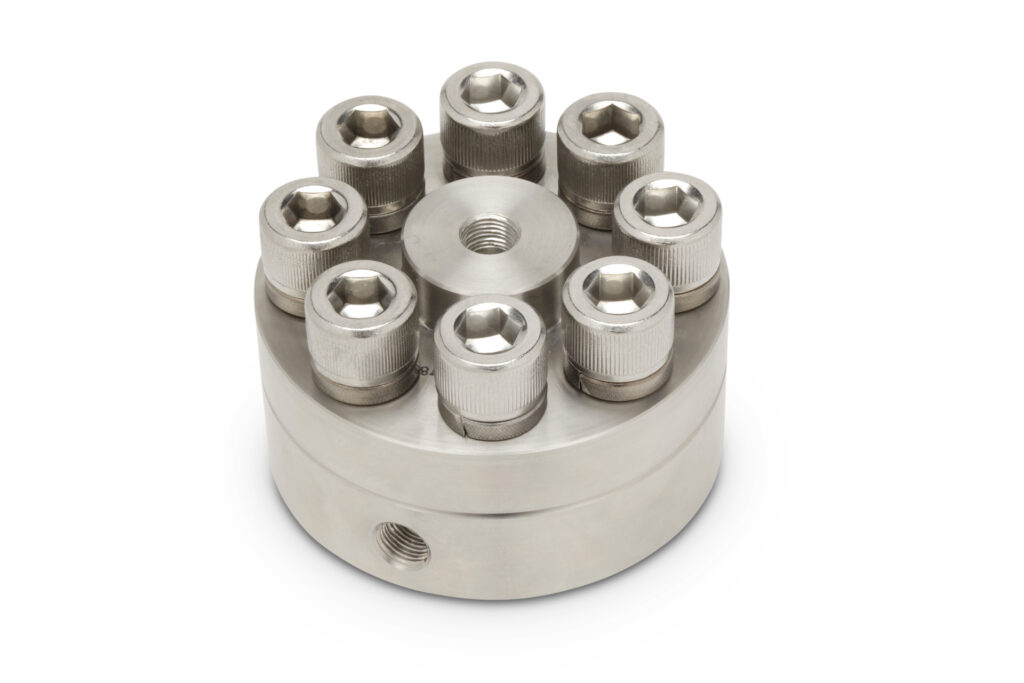
Advantages of dome-loaded multiple orifice BPRs for core flooding tests
Dome-loaded multiple orifice BPRs work in a completely different way than traditional fluid control devices. Their synergistic design elements offer multiple advantages. A supple diaphragm is the only moving part, enabling frictionless operation without hysteresis or cracking pressure. Because they are dome-loaded, they provide reliably stable pressure control. At the same time, the multiple orifice design results in an ultra-wide flow range, typically 100 times industry norms. By using unique combinations of body, diaphragm, and O-ring materials, these regulators are able to perform with high accuracy even in the harshest environments, including those with extreme temperatures and aggressive chemicals.
Case study demonstrates performance
In one recent case study, researchers required a BPR capable of maintaining a smooth production pressure to produce crude oil from core plug. They had originally used a traditional spring-type BPR in a core flooding test system, but they found that pressure fluctuations made it difficult to collect precise data for the study.
Working with fluid control engineers at Equilibar, a US fluid control company, the scientists determined that a dome-loaded multiple orifices BPR would be a better option to provide consistent pressure control for a mixed-flow of crude oil, brine, and gases at very low flow and a range of high pressures.
Equilibar’s application engineers recommended a stainless steel Equilibar® U10L BPR with Kalrez O-rings and a stainless steel diaphragm for the core flooding apparatus. This model of BPR is capable of handling the system’s pressures, which can go up to 10,000 psi, and extreme temperatures, which can go up to 300 °C.
The U10L is one of Equilibar’s Research Series of BPRs, which are designed for a variety of gas, liquid, and mixed-phase applications where precision performance is critical. The U10L model is specifically designed for applications where both ultra-low flow rates and high-pressure control are desired.
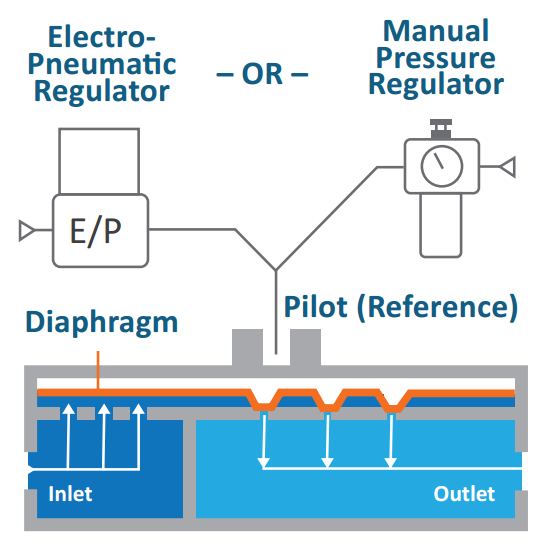
Equilibar BPRs are controlled by a pilot regulator, which provides the process setpoint. This setpoint regulator can be manual or electronic. For this particular EOR application, researchers are using an N2 cylinder with a manual high-pressure regulator to provide the setpoint to the BPR. This setup controls the back pressure precisely up to 200 bar. To apply higher pressure, they plan on using a gas booster and surge cylinder.
In this case study, the dome-loaded multiple orifices BPR was placed at the exit of the core holder, keeping precise pressure for the testing. Once installed, the U10L improved the pressure control of the core flooding system and has met expectations. Equilibar dome-loaded multiple orifice BPRs have been used for many other EOR applications around the world, as well as related applications including core analysis, pore pressure transmission testing, and other oil and gas scenarios that involve high pressure, harsh chemistries, extreme temperatures, and wide flow rate ranges.