A mechanical seal consists of 3 parts – its spring, a rotating face and stationary face which are within close contact with one another and rely on the process fluid lubricating and cooling the rotating and stationary faces to ensure the seal functions as designed.
Although this seal prevents fluid from escaping at the rear of the pump casing, it is actually designed to leak tiny amounts of fluid to ensure it performs as designed.
Mechanical Seals can often last years, but should failure occur at frequent intervals further investigation should be sought into the reasons for premature or frequent failure.
Here are 8 reasons why a Mechanical Seal may fail within a process:
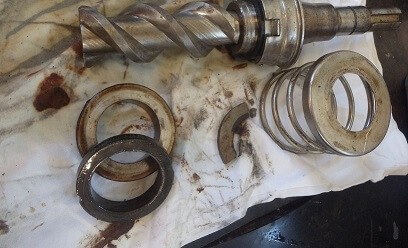
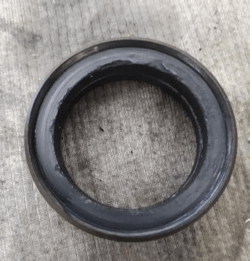
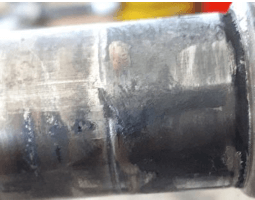
1. Dry Running
Dry running is where a pump is operated without fluid. This means internal parts which often rely on the pumped liquid for cooling and lubrication are subject to high amounts of friction and heat leading to prompt failure. Failure can happen in seconds and so it is always important to ensure the pump is completely filled with fluid prior to operation.
Tip: If a seal has been dry run, the face of it will usually white, and to prevent dry running a sensor detecting current draw can stop pump operation before too much damage occurs.
2. Chemical Attack
Every material has its Kryptonite. If a liquid is incompatible with a fluid it can cause internal parts such as rubber seals, gaskets, impellers, pump casings and diffusers to crack, swell, contract or deteriorate.
Chemical compatibility tables outline which materials are compatible with which fluids rating them from Good to Poor. Whenever frequent pump wear occurs, or should pump failure occur after a short amount of time- this is one of the first items which should be checked.
3. Cavitation
Pumps are controlled by the system they operate in. If not restrained they can operate at performances which are damaging to internal parts – similar to driving a car downhill in first gear at speeds where the rev counter is in the red.
Operating a pump at the wrong parts of a performance curve, lead to accelerated part wear – one of which can be the seal.
4. Excess Heat
Excess heat from high fluid temperatures can cause elastomers to swell or melt restricting its effectiveness leading to leakage.
High fluid temperatures not only originate from process but if fluid recirculation occurs for extended periods of time either due to operation against a closed valve or should fluid continue to recirculate through a relief valve, energy is transferred to the fluid causing heating of the fluid.
5. Incorrect Fitting
When a seal is installed it is designed to move with the shaft. Lateral and vertical movement is normal. If installed incorrectly then excess play can cause damaging forces to the seal. If too restricted the seal springs can snap or faces wear.
6. Shaft Movement due to bearing Wear
If a shaft has too much play, its lateral movements will cause the seal to absorb such forces rather than the bearings – something which it is not designed to do. High torsional forces can cause the seal to tear.
7. Worn Shaft or Wear
Certain elastomers such as Viton can increase shaft wear, meaning when a seal is replaced, it the shaft has a smaller outside diameter (OD) reduced by friction over the years, then the seal will not fit tightly causing fluid to leak.
8. Solid Ingress
Seals are specifically designed for a pumping process and should a seal encounter solid particles such as sand or silt which it is not designed to handle, it can cause the forming of grooves in soft seal faces causing the seal to drip and leak the process medium.
Installing a hard faced mechanical seal can limit and prevent this issue from reoccurring provided concentrations of solids are not above those specified at enquiry stage.
If you are frequently experiencing Mechanical Seal Failure, and are looking to eliminate this from your process, speak to us – North Ridge Pumps to see how we can help.