NPSH is particularly important when dealing with liquids that have low vapor pressure and are prone to boiling at relatively low pressures. When a liquid starts to boil while being pumped, the vapor displaces the liquid, causing pumps to lose performance or fail altogether. This is called cavitation.
Understanding NPSH: Key to Preventing Cavitation
NPSH is a crucial factor in ensuring efficient pump operation, particularly in preventing cavitation—a damaging phenomenon where vapor bubbles form and collapse within the pump, potentially harming the impeller and other components. To understand NPSH in depth, let’s break it down into its two main types:
- NPSH Available (NPSHA): The “A” is Available. This is the absolute pressure head available at the pump suction minus the vapor pressure of the fluid. It indicates how close the fluid is to vaporizing. When NPSHA is low, the risk of cavitation increases.
- NPSH Required (NPSHR): The “R” is Required. This is the minimum suction pressure head required by the pump to avoid cavitation. Each pump design has a specific NPSHR, which depends on factors such as speed, size, and application.
Cavitation is particularly concerning in centrifugal pumps, as it can lead to severe performance issues, increased maintenance, and, if left unchecked, significant damage to the pump components. For this reason, understanding the NPSH values and ensuring they are balanced for the specific system is essential. NPSHA must exceed the pump’s NPSHR rating for the chosen operating conditions to ensure that cavitation is avoided.
To put vapor pressure (boiling points) into perspective, water boils at 212°F (100°C), Freon at -41.4°F (-40.8°C), CO₂ at -109.2°F (-78.46°C), and ethylene glycol at 387.1°F (197.3°C).
To give a working example of NPSH in action, let’s use water for this demonstration.
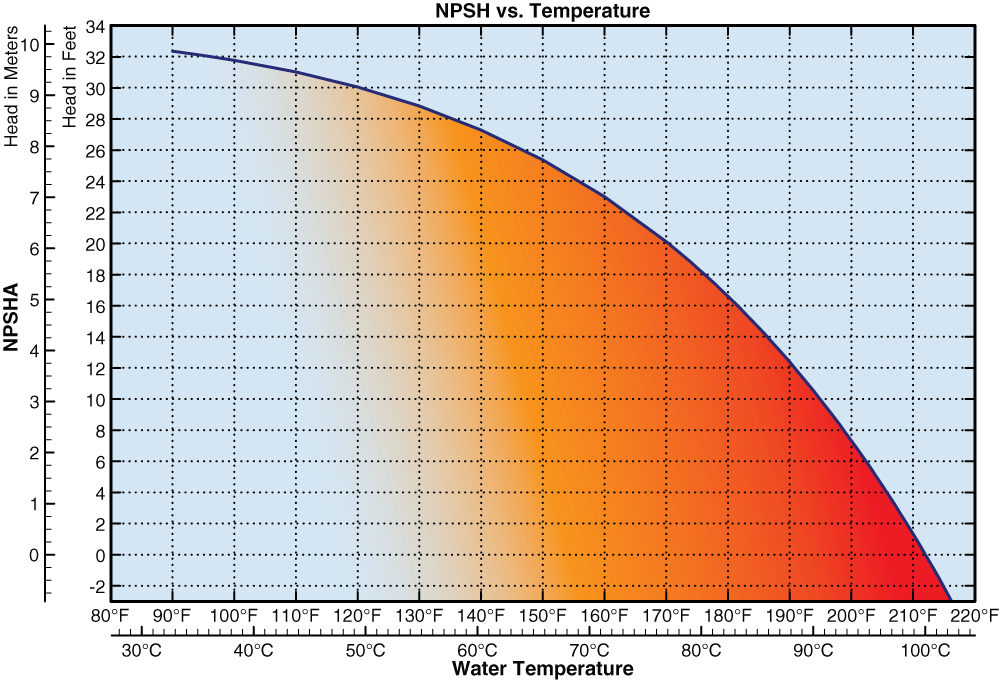
Keep in mind that atmospheric pressure at sea level is 29.9212 Inches Hg (Inches of Mercury). That converts to 14.696 PSI, 1.013 bar, or 33.9478 Feet of Head. The desired performance of the needed pump for this application is 5 GPM at 300 Feet of head. A MTH Pumps T51D is the pump we will select.
Example A – Ambient Temperature Water
- The water temperature is below 90°F.
- The water level of your source tank is 4 feet from the centerline of the pump to the top of the water level.
- The pump will have 36.34 feet of NPSHA (Available) for it to operate.

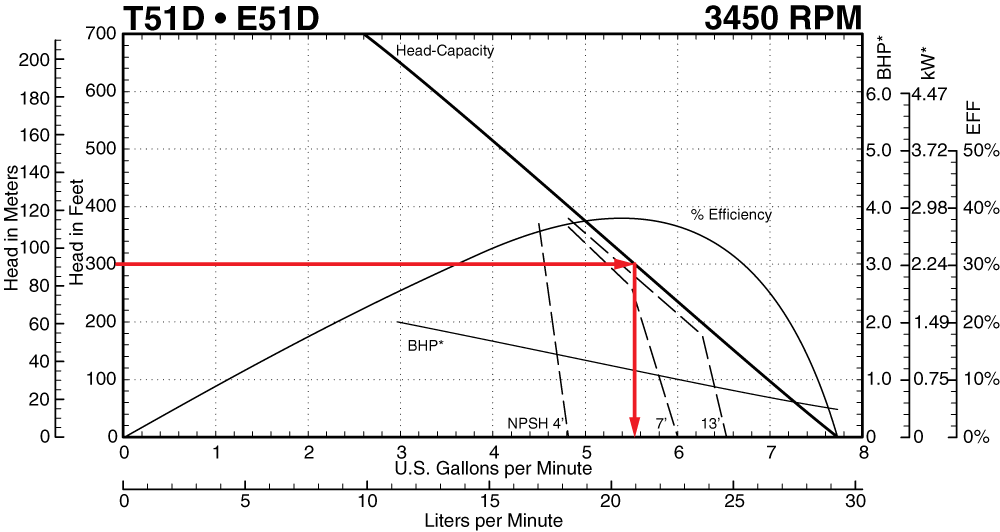
When the NPSH is not an issue, the pump will perform at full performance. The T51D will produce approximately 5 ½ GPM at 300 Feet.
Example B – Water that has been heated, but not boiling.
- The water temperature heats up between 207°F and 208°F
- The water level of your source tank is again at 4 feet from the centerline of the pump to the top of the water level.
- Because of the increased temperature, the NPSH of the water is now only approximately 3 feet. Combined with the 4 feet in the tank, the pump now only has 7 feet of available NPSH for it to operate.
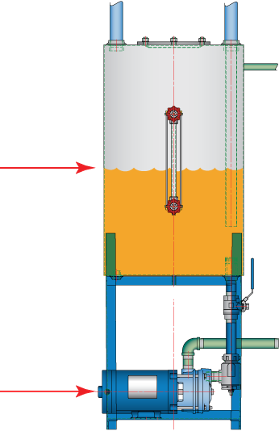
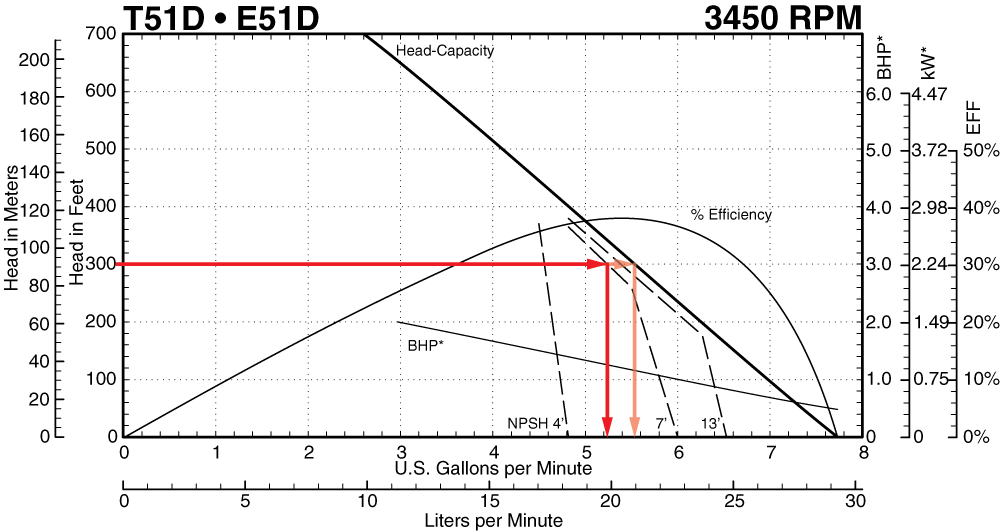
Because of the design of the regenerative turbine pump, any vapor that is forming inside the pump because of the high temperature (Low NPSHA) will immediately evacuate with the flow of the pump. This will cause the fluid that is being pumped to be displaced by the vapor and the performance of the T51D will decrease from the full 5 ½ GPM to approximately 5 ¼ GPM, while still maintaining 300 feet of head.
Example C – Water that is at boiling temperature.
The water is now boiling 212°F
The water level of your source tank is still at 4 feet from the centerline of the pump to the top of the water level.
Now that the temperature has reached boiling, there is no NPSH available in the water itself, except for the 4 feet of water remaining in the tank. Therefore, the NPSHA is 4 feet.
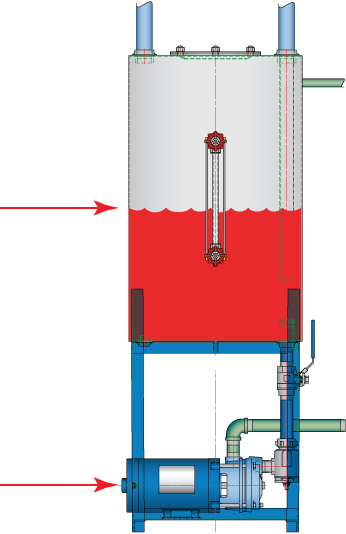
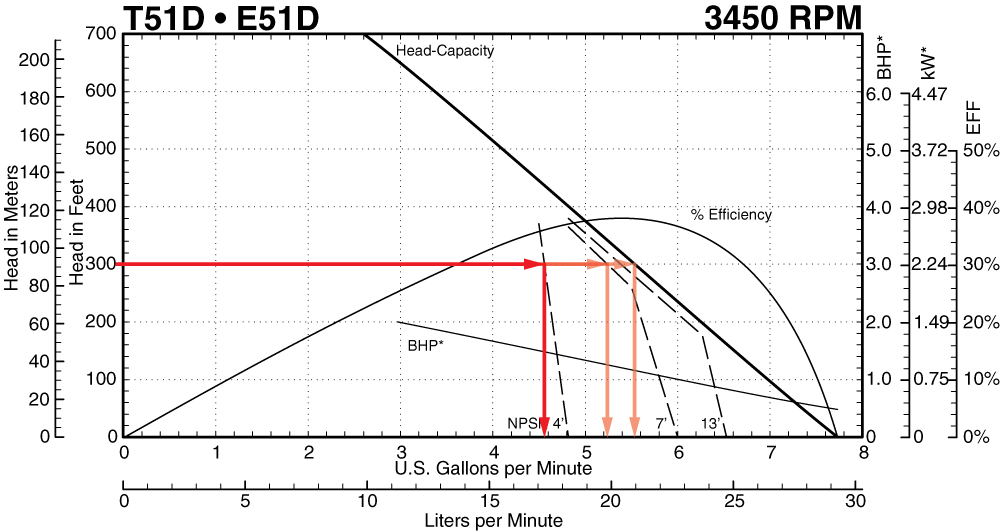
MTH’s close coupled performance curves are published with the head-capacity of the pumps taken into account for the most common NPSHA scenarios. In the case of the T51D running with only 4 feet of NPSH, the flow of the pump has now been reduced to approximately 4 ½ GPM, while maintaining the 300 feet of head needed for the application.
Under boiling fluid conditions, most centrifugal pumps will experience cavitation starting at the eye of the impeller, where there is the least amount of pressure. This creates a barrier of vapor that can all together stop the flow and quite possibly cause damage to the pump.
These principles of NPSH are consistent with many applications where the source tank is open to the atmosphere. Many of these applications are boiler related, where heat is being produced for the purposes of climate control or for processes that need high temperature liquids, such as food manufacturing or sterilization. Other applications where NPSH is important is in closed loop systems with liquids that have low vapor pressure, such as refrigerants and CO2. Those processes are often under extreme pressure to keep the liquid in a liquid state while it is circulated throughout the system.