Loris Medart, a fluid dispensing engineer with more than 20 years of experience and founder of feed systems manufacturer SR-Tek, discusses some of the ways in which you can preserve the quality of your fluids and save huge sums of money by reducing lost production time.
Air bubbles can devastate production
Air bubbles can have a devastating impact on production. Medium viscosity adhesives, silicone, UV, epoxies, latex, and oil are just some of the fluids that are particularly affected. Trapped gasses can ruin the fluid or the part it is dispensed on, costing tens of thousands of pounds in lost production time. In the electronics industry, where epoxy resin encapsulation or coating is often an essential process, air bubbles lead to catastrophic parts failure.
There are a number of ways in which you can avoid or minimise the chances of gas entrapment in industrial fluids, including:
- Avoiding excess fluids
- Containing fluids within a suitably sized vessel
- Maintaining a consistent pressure and fluid level
- Minimising transfer between vessels
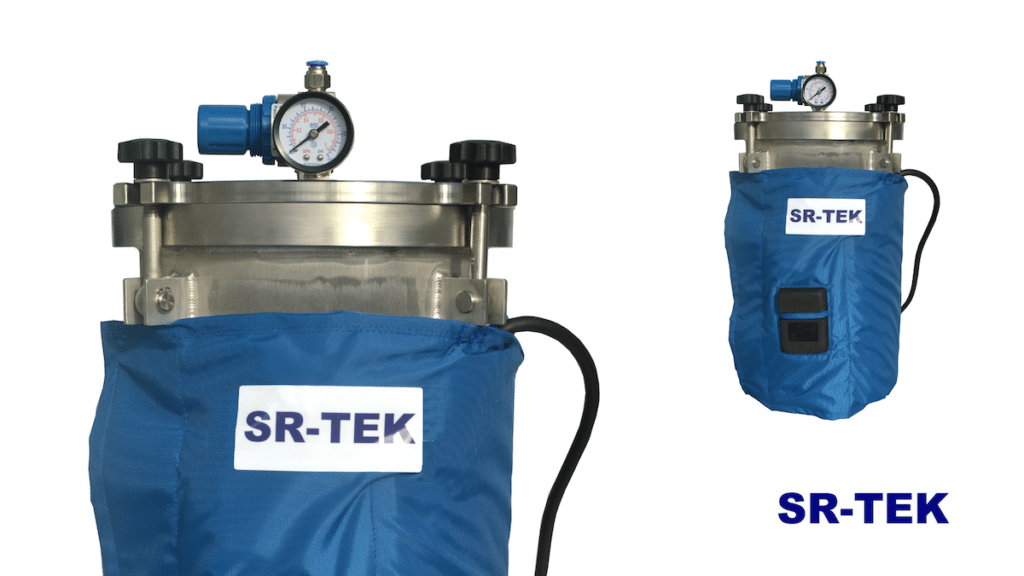
Temperature is another critical factor
Even if the temperature fluctuates just a couple of degrees, it can have a huge impact on the production line, potentially causing huge delays. This is particularly problematic if your product contains a temperature-sensitive liquid such as UV adhesive.
To support clients with changing temperatures, the latest SR TEK innovation, the Temperature Control Jacket allows you to maintain insulation at a consistent temperature and limit unwanted heat loss.
SR-TEK founder Loris Medart explains: “Temperature, like pressure, can impact viscosities and flow rates with changes of just a few degrees causing considerable disruption to production. This latest innovation enables total environmental control – a great advantage for customers using the SR-TEK ST Series.”
Take a look at our YouTube video for a demonstration of how the jacket works. The Temperature Control Jacket is currently designed to work with our ST Series pressure tanks and LT Series pressure tanks.