A company specialized in paint and pigments for over 110 years turns raw materials into pigments and offers them as powders, stable dispersions, granules and other forms. The products are used in a wide variety of industries, including specific industrial varnishes or for staining and dyeing asphalt, plaster, plastics, textiles, paper, glass and much more.
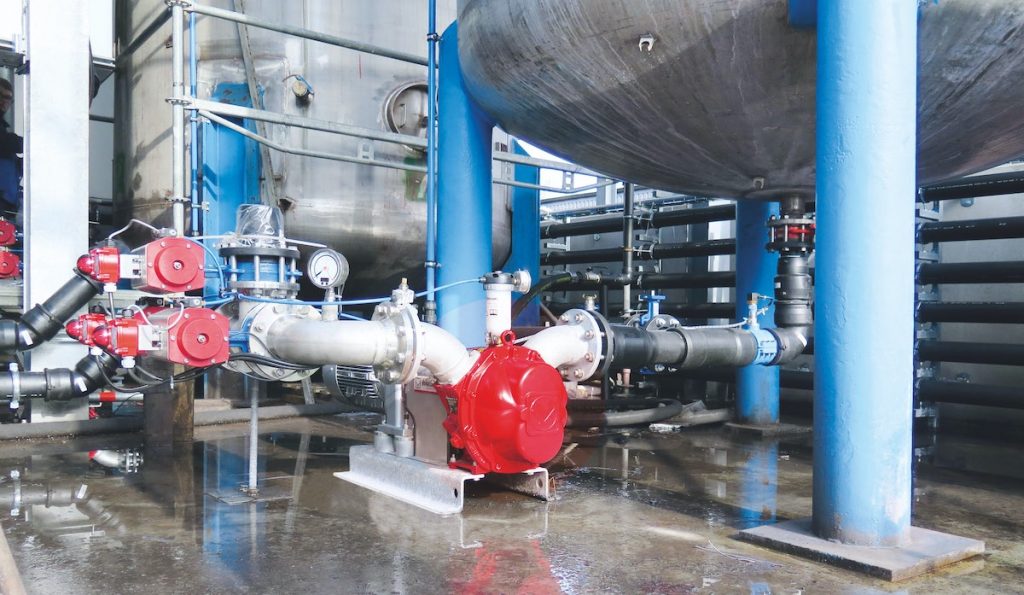
Pump requirements
The company has begun to modernize its operations. This involves bringing together multiple production subsections into a single hall. Some connecting components such as pumps and pipes were renewed and sub-processed. Because many separate work processes are now performed in one location, an unexpected problem occurred: noise levels in the new hall were excessively high and had to be reduced. The hose pumps that had been used previously now produced too much noise. Also, they did not deliver the necessary quantities so they had to be replaced. The company’s machine park also includes three mixers. These disperse water and pigments to form paints. In other words, the solid pigments are mixed in water until they reach the desired consistency or they are distributed so finely in the water that they remain suspended. This is why metered pumps are needed to feed the individual components into the mixer. When it comes to moving the finished product away after the mixing process, quiet, powerful and durable pumps are called for. The company ordered a Vogelsang VX136-70Q rotary lobe pump for the three mixers. The pumps convey the mixed paint at a rate of 60 m³/h and a pressure of up to 10 bar to a tank for subsequent homogenization. In this way, the contents of a mixer – approximately 6,500 kg of paint – can be decanted to a tank in ten minutes.
Self-priming
The company uses about 25 tanks to store finished products. During the restructuring and modernization, new pumps were also added. One of the reasons was to provide recirculation pumping in order to mix the paints. Also, the centrifugal pumps used previously could not withstand the abrasive paints. As a result, they purchased a Vogelsang rotary lobe pump from the IQ series for each tank. Thanks to their reversible flow direction, they were well suited to installation and were also used to decant the end product to tanker trucks or litre boxes. As with the VX rotary lobe pumps on the mixers, the pumping speed was also a key factor with the IQ models. The paint had to be pumped quickly, particularly when it came to filling a truck, as the trucks could not afford long holding times. The new IQ pumps conveyed the end product five times faster than the old centrifugal and hose pumps. Filling up the tanks now took just four minutes instead of twenty.
Most importantly, the old centrifugal pumps were not self-priming, so they could not be installed at the desired position. Some of the mixers were set into the ground. If they were drained using centrifugal pumps, the pumps would have to be installed below the level of the mixer drain. This variant was rejected due to poor accessibility. The company therefore decided on selfpriming pumps that could be installed above ground. The IQ pumps from Vogelsang were set up at ground level because they are able to draw medium up from depths as low as nine meters. Thanks to the built-in InjectionSystem, the interior sealing in IQ pumps is better. This increases their suction capacity and makes the pumps resistant to dry running.
Nitrile rubber lobes
As the metal core of the lobes is coated in rubber, the pump is resistant to chemicals. Similar media also withstands high pressures. The lobes do not come into contact with the pump housing, which results in a gap that prevents abrasion on the lobes and ensures a long service life. The blades of the lobes are twisted about the axle at a defined angle. This HiFlo® principle, developed by Vogelsang, ensures gentle pulsation-free pumping by eliminating pressure surges.
Maintenance
Having the IQ pumps at ground level makes operation and maintenance much easier. Furthermore, the housing of the IQ model consists of a single component, meaning that the pump chamber can be accessed with just a few hand movements. “When cleaning and replacing all the wear parts – including the rotary lobes, wear plates and gasket – you don’t have to unscrew the pump from the pipe. This saves time and makes service easier. The pump only requires a few spare parts, which keeps the costs of maintenance and replacing wear parts down.
How to dismount an IQ pump
1) Open the pumping chamber
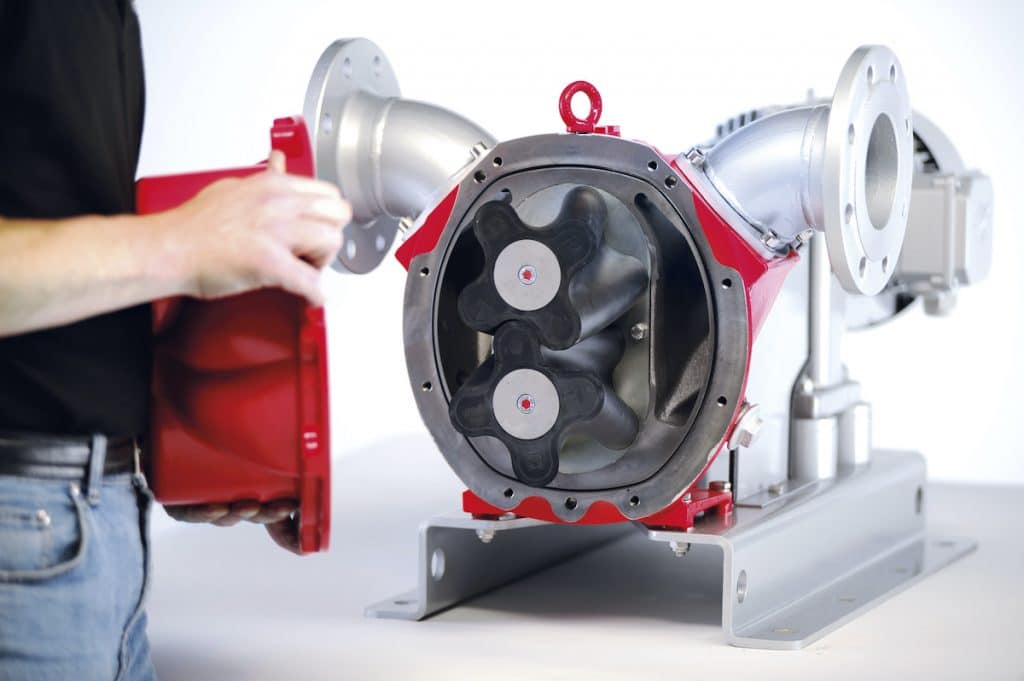
2) Dismount the rotary lobes
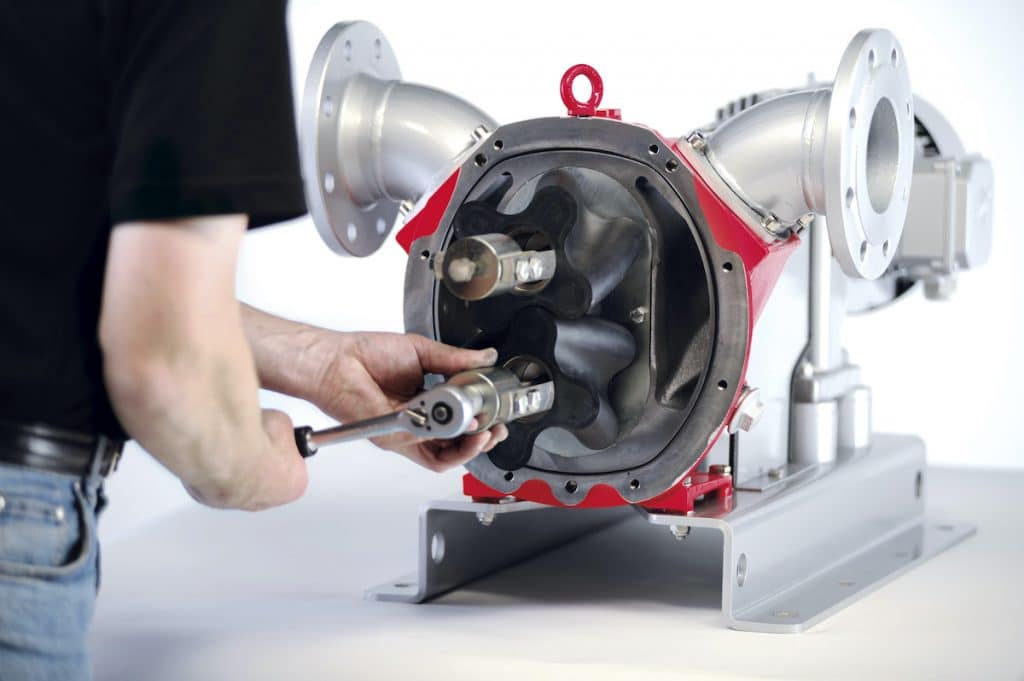
3) Remove the wear plates
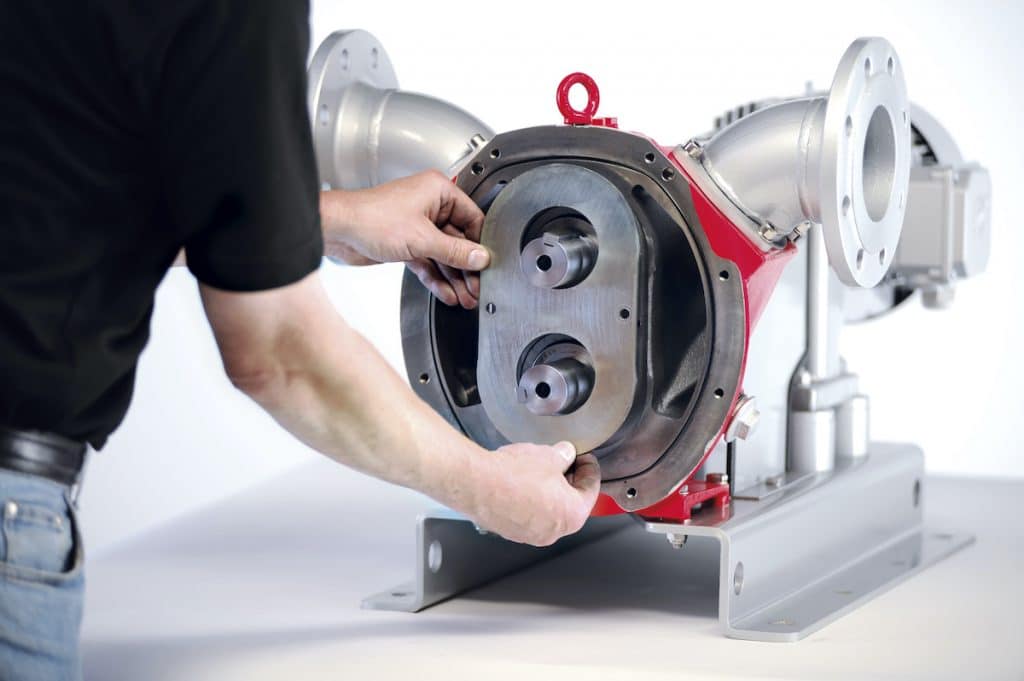
4) Remove the Quality Cartridge mechanical seal
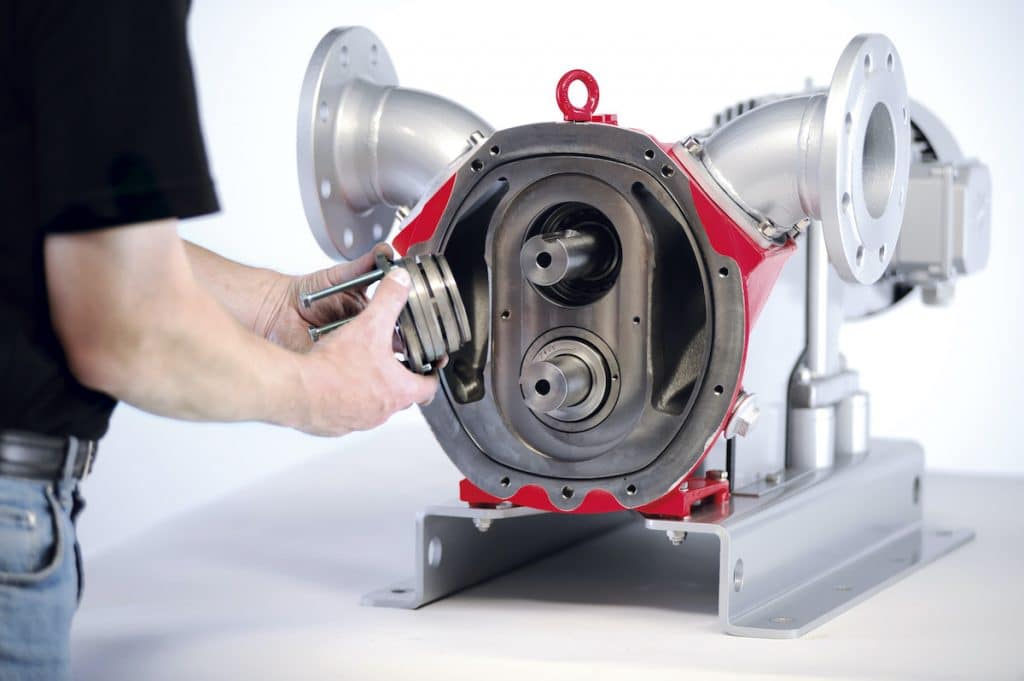
5) Assembly
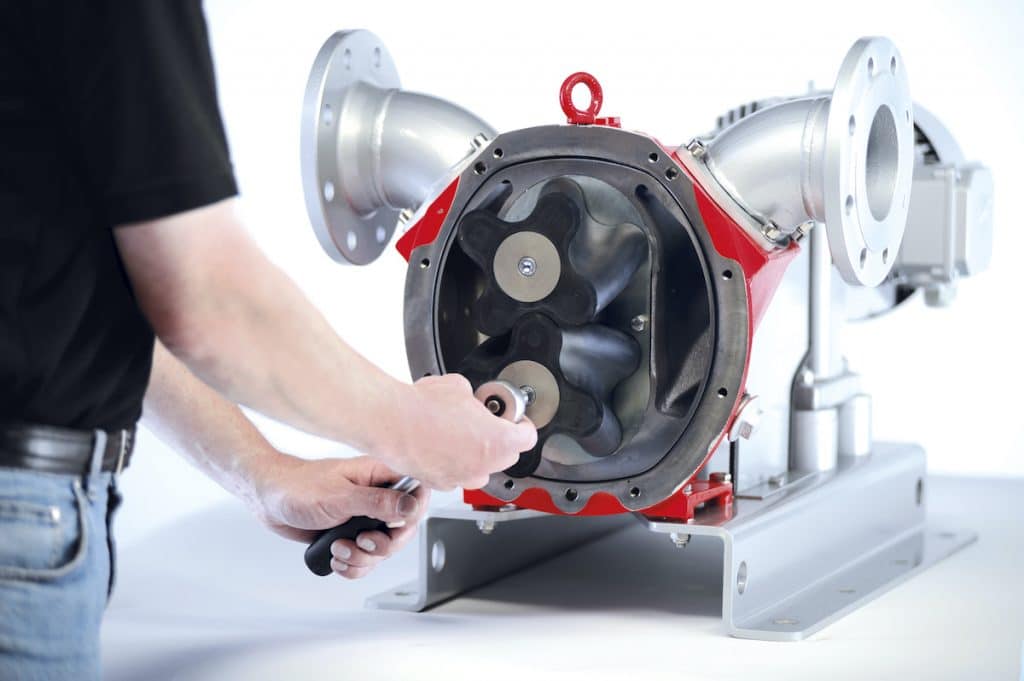