Rodelta’s choice was not to lean back on there proven record by there installed base, but to redesign the OH5 successfully to the latest standard of the API without any deviations. We believe that today’s markets require innovators that work according to the latest API guidelines. Because these guidelines are a summary of the latest customer experiences in the field and ensure the smooth functioning of their critical processes.
Goal of the redesign is maximum reliability with minimum rotating and stationary parts. Our experience of the OH5 pump type in the field made is feasible to conduct this exercise for redesign. Evaluating the hydraulic field chart, one can see that both flexibility and coverage were our main parameters for defining the hydraulics of the pump.
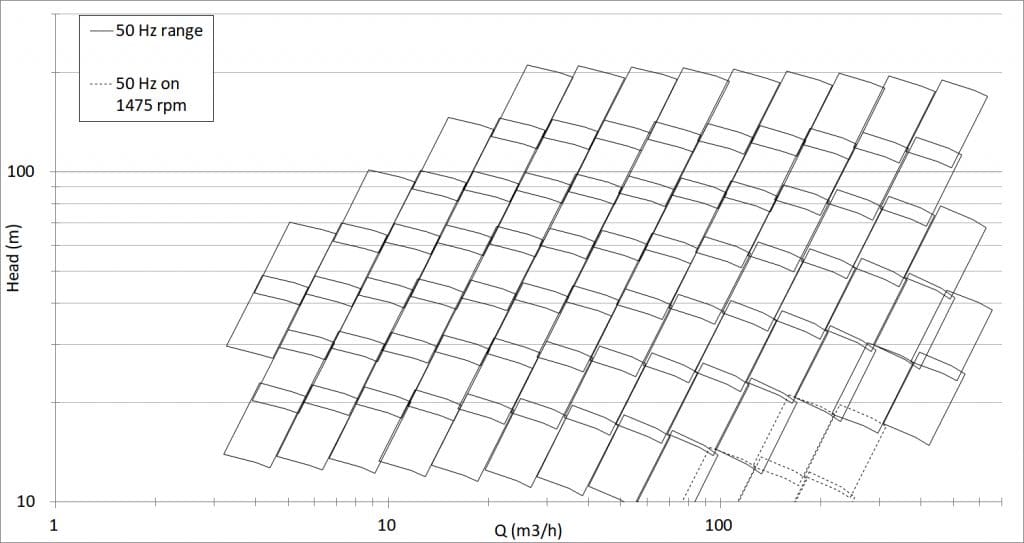
As NPSH is a crucial topic in selecting a pump, we have designed an unique suction box, “on which a patent is pending”, enabling the customer to find a good match in the overhung pump range without using tools like an inducer (not allowed by API). Alternative for conditions with low NPSHa would be change of pump type to between bearing type. Besides cost this would also effect footprint.
The OH5-ETL pump type complies with the most stringent emission requirements considering shaft seals. For instance, the seal chamber is fully compliant with the API 682 and suitable for all mechanical seal styles, including advanced gas barrier seal technology.
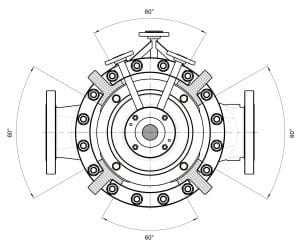
For easy maintenance we designed the pump to have 240 degrees opening accessibility to the seal. The mechanical seal is positioned to allow seal connections not being affected by the studs and nuts on the pump cover. In conjunction with the redesign of the pump housing, this has no adverse consequences to the shaft span. The shaft span is even one of the shortest in the market and also complies with the shaft flexibility index as described within the API 610.
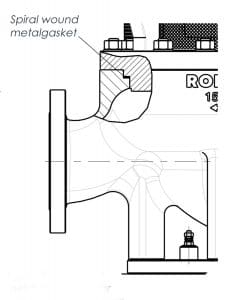
Pump casing and cover have a metal-on-metal fit to ensure complete enclosed and controllable compression of the gasket. This guarantees good alignment and sealing. There is sufficient space everywhere for the use of mechanical torque wrenches in order to enable easily set pre-tension in a controllable manner. The cable can be connected to the motor through the closed sides of the motor support. All possible motor options can rotated in steps of 45 degrees relative to the pump housing.
The ETL has milled and interchangeable diffuser channels, which are generated specifically for each customer duty. This offers a high degree of flexibility when dealing with changing production parameters. An infinite number of hydraulic solutions can be generated with 13 pump housings and 13 specific speeds on impellers in this family.
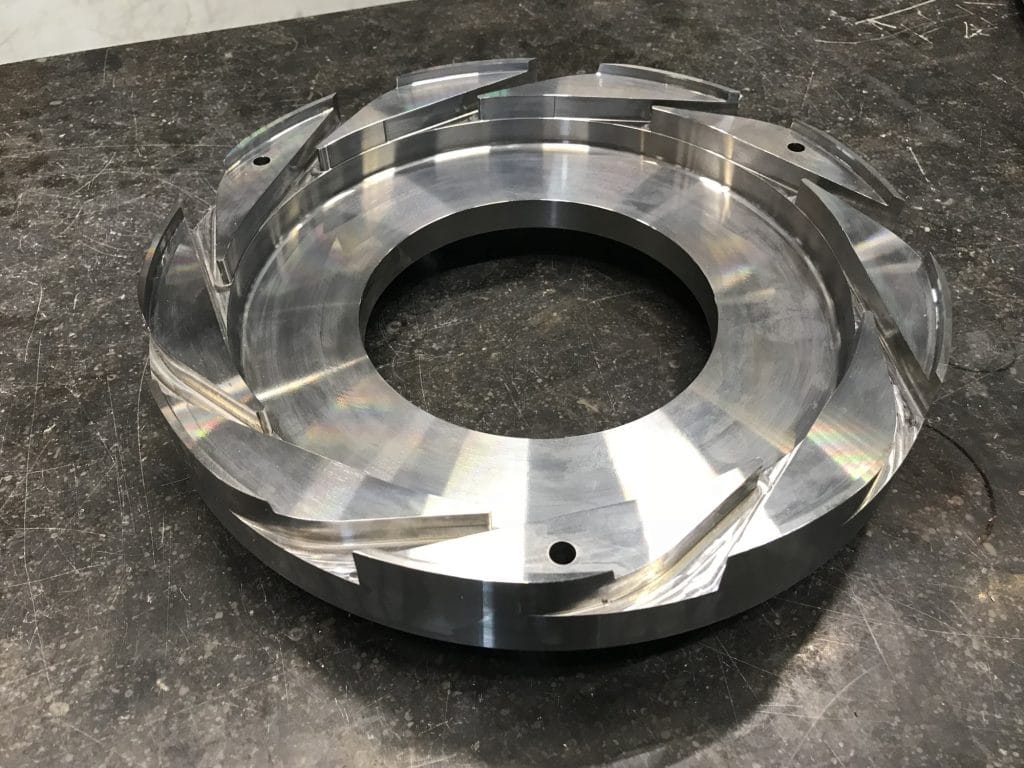
The connection dimensions of the pressure- and suction flange are made according to the British Standard BS4082. Complying to the British Standard ensures this OH5 pump type can easily be exchanged in situations where pipework meets this standard with regard to centreline and distance between flanges. The footprint of the pump is in accordance with the DEP requirements set by Shell in which the anchors and ground dimensions for fixing the pump are normalized.
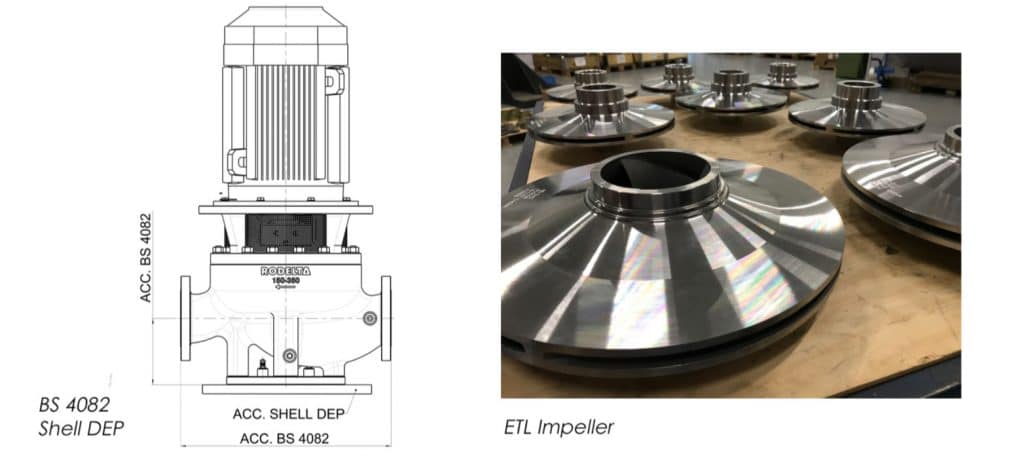
The impeller is casted with ceramic mouldings to make sure the high quality and efficiency demands are met with the most sophisticated casting and production techniques. All impellers are dynamically balanced according to the latest requirements set by the API. This ensures flawless performance for the given operation range with vibration levels of nearly zero.
Reviewing the ETL (OH5) pump to a similar size OH2 pump, the ETL offers many advantages. Besides the fact that a large number of parts are made redundant due to the construction, the OH5-ETL has a much smaller footprint. This makes it ideal for installations where floor space is limited. In addition, the simple drop-in assembly makes maintenance much easier in tight, confined spaces.
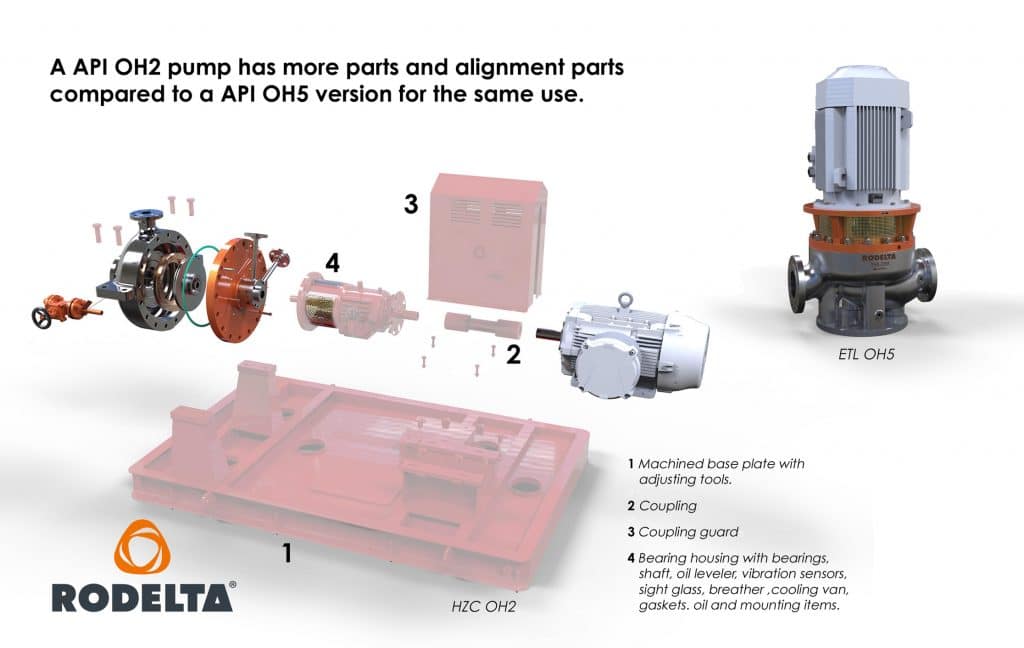
Less pump parts results in less initial cost but also the less rotation parts will result in longer Mean Time Between Repair (MTBR) and less parts on stock (= less operational cost) Floor space
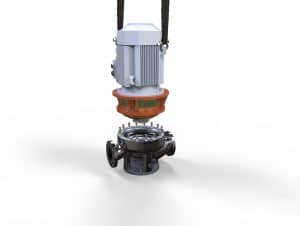
Per industry experience we know that about 90% of the pump life cycle costs (LCC) is after the equipment has been purchased and installed. In addition to its product range, Rodelta provides an extensive package of solutions to offer customers cost savings during the life of the pump system, including
• First purchase
• Installation
• Energy consumption
• Maintenance
• Production losses
• Environment