These were needed for AdBlue dosing at high pressure through an injection lance. The pumps would be a key component in a larger system designed to reduce exhaust emissions in an industrial plant using a process known as Selective Non-Catalytic Reduction or SNCR.
So what is AdBlue?
You might know AdBlue as a popular type of diesel exhaust fluid. It’s usually stored in a separate reservoir and topped up via a blue filler cap next to your fuel filler cap, in the boot or under the bonnet.
But it’s used by many more people than just motorists. In fact in just a few years, it’s become perhaps the most important fluid in the transport industry after fuel. It’s essential for cars, trucks, tractors and even trains and boats. It’s also used in thermal power stations, generators and factories.
It’s composed of 32.5% urea and 67.5% demineralised water. Urea is a synthetic product derived from ammonia and it’s also naturally present in human and animal urine.
So what’s it used for? AdBlue dosing works through urea injection to reduce emissions in exhaust gases and fumes. In diesel engines, it’s part of a process called SCR – Selective Catalytic Reduction. For the treatment of fumes, it used in Selective Non-Catalytic Reduction or SNCR and may have a different composition: up to 40% urea for example.
What’s an SNCR System?
Selective Non-Catalytic Reduction is a tried and tested, commercially-available technology that’s been working successfully around the world since 1974, It’s installed in over 300 systems globally on various combustion sources including coal-fired utility applications.
As well as being used extensively in the electric power industry, SNCR is also being adopted to control nitrogen oxides (NOx) emissions from a range of combustion sources including industrial boilers, cement kilns, pulp and paper power boilers, thermal incinerators, steel industry process units, refineries and more.
How does it work?
The SNCR system simply converts nitrogen oxides (NOx) into harmless nitrogen (N2) and water vapour (H2O). It does this by using ammonia or urea injection at high temperature directly into the upper furnace or convective pass of a boiler using water as a carrier.
NO2 + NO + 2 NH3 ↔ 2 N2 + 3 H2O
4 NO + 4 NH3 + O2 ↔ 4 N2 + 6 H2O
2 NO2 + 4 NH3 + O2 ↔ 3 N2 + 6 H2O
It’s the simplest and most economical form of nitrogen-reducing technology. It’s ideal for applications where an NOx reduction of 30% to 40% is required working to tight schedules and with limited space.
In fact, the process can achieve surprisingly high NOx reduction rates without using an additional catalyst. It can do this providing the flue gas temperatures are high enough, between 895°C and 1100°C, to achieve the chemical reaction.
It’s more cost-effective than SCR – selective catalytic reduction which is significantly more expensive because of the need to buy and maintain the catalyst. SNCR is a more affordable solution where the operating environment is not suitable for a catalyst.
Specific project requirements
As part of the project brief, our client required two automatic metering dosing pumps to administer AdBlue at high pressure through an injection lance.
Here at North Ridge Pumps, we’re not restricted to a single pump technology. We use our expertise to offer a bespoke solution, not something straight off the shelf. So we can select the best pump for any particular client and application at the lowest lifetime cost.
The automatic metering dosing pumps we specified were electric diaphragm dosing pumps with locally mounted controls which enable accurate and complete control of fluid dosing via the screen or remotely via wifi, 4-20ma or ethernet.
The pump head contains a diaphragm housed in a chemically resistant material which in this case was polypropylene. The PTFE diaphragm is compressed, and opened via a polyethylene (PEUHMW) piston, with ball valve on the suction and discharge ensuring that the pump can self prime and repeatedly dose at the required pressure.
Diaphragm compression and the associated dosing rate of the pump is controlled via the motor speed and rate at which the eccentric movement of the gearbox compresses the diaphragm via the piston rod. As the design is positive displacement, the pressure generated will remain consistent with only the flow varying.
The spraying nozzles on the urea injection lance ensure the NH3-Water solution is injected into the flue gas at the required pressure, and spray pattern. The water which acts as a carrier evaporates, leaving the gaseous NH3 to react with the NOx.
Exact pump specifications
The metering dosing pumps we manufactured were designed to achieve flows of up to 11L per hour and pressure up to 15 bar. They would be remotely controlled via their 4-20ma input for full automatic dosing control.
In addition, these automatic dosing pumps had advanced controls to provide proportional dosing using a variety of methods:
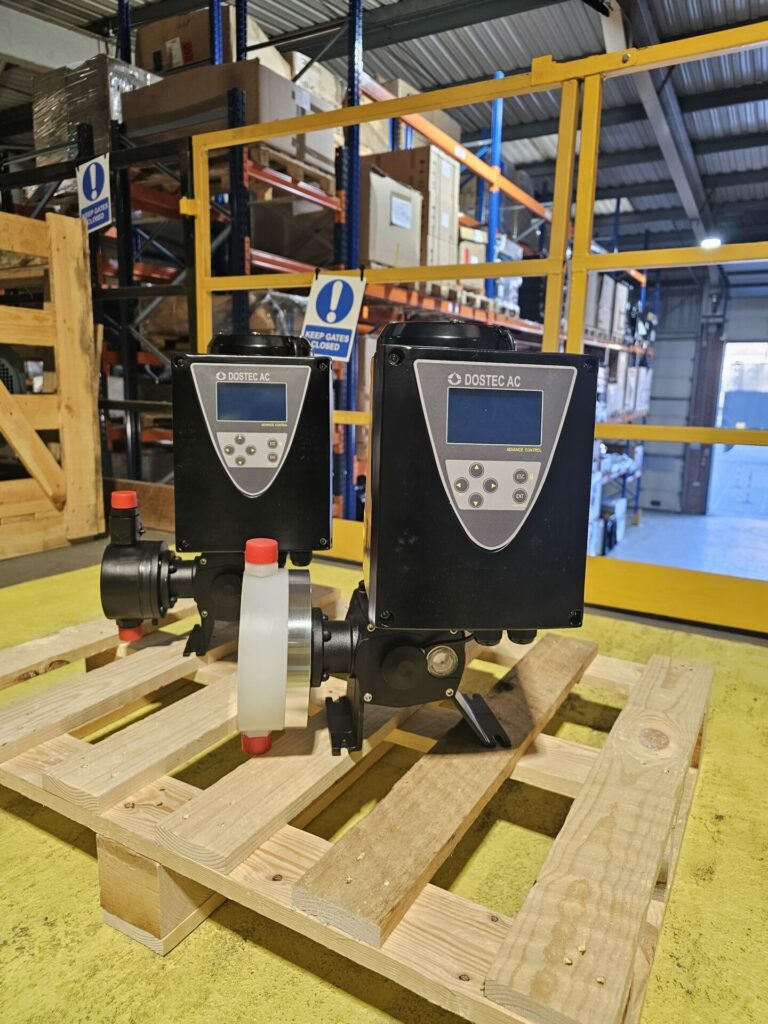
- Manual: flow adjustment using the on-board controls and display
- Analogue: dosing proportional to a 0/4-20mA signal
- Proportional to flow: dosing according to water flow
- Proportional to pulses: stroke frequency proportional to input pulses via a flowmeter or other device
- Volume batch control: dosing a defined volume, after a manual, remote or timed pre-set start
- Timed batch control: dosing for a set time, after a manual, remote or time pre-set start
- ModBus: full dosing control through ModBus on-site control protocol.