In recent years brighter LED luminaires have emerged that are causing process experts to re-assess their vessel lighting needs. What is the ideal level of brightness? What is the relationship between brightness and the size of the vessel? How should brightness be measured? The International Society for Pharmaceutical Engineering’s Bioprocessing Equipment (ISPE-BPE) subcommittee is looking at these questions in the hope that someday guidance may be offered. In the meantime, this article may shed a little light on the subject.
The traditional halogen luminaire emerged from industry suppliers based on the technology that was available. Halogen luminaires were brighter than other incandescent luminaires, and they could be used in explosion-proof enclosures. A 50W bulb was about the right size for the application. Higher wattage bulbs were available, but they required bulky enclosures to remove the heat.
Suppliers did not develop their luminaires to achieve any particular target of brightness, as no standards for light brightness or tank illumination existed. If the view was dimly lit, the only option was to increase the wattage of
the bulb. This added more light but also had the negative side effect of adding additional heat to the process.
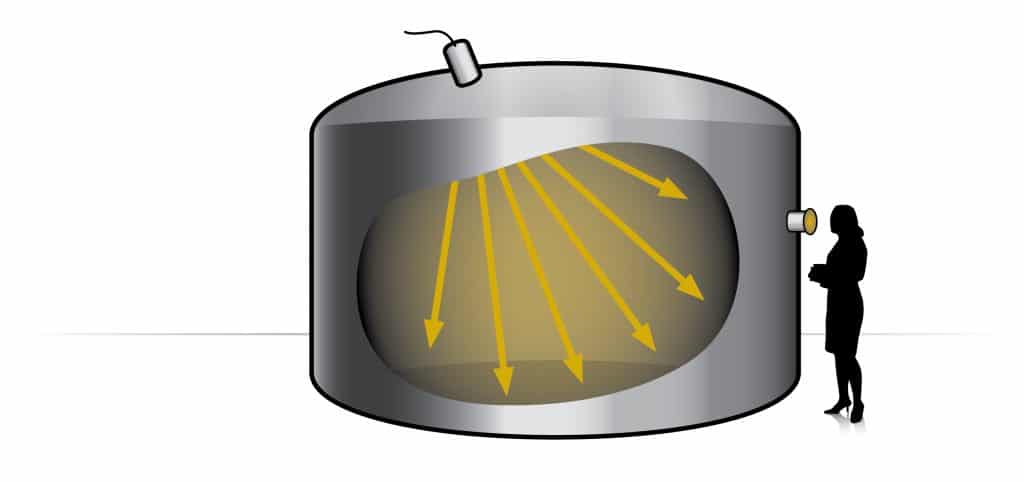
Now that LED luminaires are available that are up to four times brighter than traditional halogen luminaires, and lumens are replacing watts as a unit of specification, process experts are wondering how many lumens are enough and how many are overkill for a given application. The answer requires an understanding of emitted light, reflected light, distance, angles, perception, and light measurement methods.
The brightness of the emitted light (technically called “illuminance”) of a luminaire is measured directly with a light meter. After the luminaire is installed on a process vessel, the illuminance can only be measured from inside the vessel. Obviously, this would be an invasive procedure and be impractical in many process applications. Alternatively, light can be indirectly measured externally via a sight glass viewport, but that can measure only
the brightness of the reflected light, technically known as “luminance,” rather than “illuminance.”
As the object of process inspection is not the light but rather the process media that the light illuminates,
it makes sense to measure the reflected light at the sight glass port that operators use for visual inspection.
In addition, using the sight port ensures that all measurements are made at the same point and angle.
It also allows for measurement during different vessel conditions, which can affect luminance. For example,
light reflection from stainless steel is approximately 50%, but the process media can have varying levels of
emissivity depending on color and opacity. Therefore, a half-full vessel will likely have different luminance than
an empty vessel.
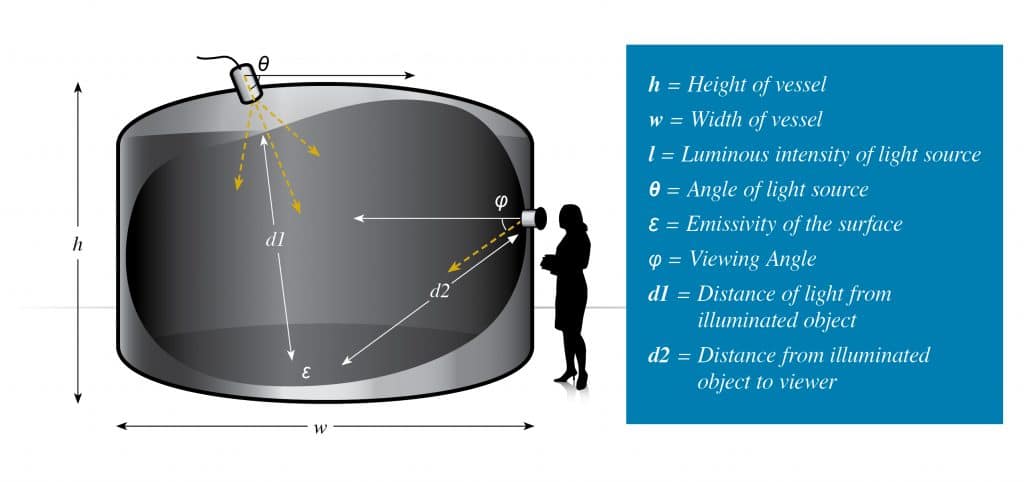
But is it really true that, by measuring the light levels of a stainless steel vessel from a viewport (sight glass, opening, etc.), an operator can determine that the lighting inside the vessel is appropriate for proper process observation? Let’s look at the physics involved.
The total amount of light emitted from a luminaire is called luminous flux. It is measured in all directions
directly. As soon as the luminaire is placed into the application, the luminous flux cannot be measured. In application,
the main concepts are illuminance and luminance. Illuminance is the amount of light that lands on a surface
and luminance are the amount of light reflected by that surface. For example, if a light is shone onto an object,
then that light is illuminance, while the light that reflects off the object is luminance. Luminance is what is seen
by the observer (Figure 1).
The reason this is important is that the light seen by the person observing the interior of a vessel is luminance light. This light sums up the countless variables that can affect the lighting conditions inside of the tank, figure 3.
It is generally accepted that to observe an object in fine detail, one should have an illuminance somewhere in excess of 1000 lux. As stated previously, measuring the inside of a tank is difficult and can’t be done during production. Also, calculating this lighting is a complicated affair that requires many known variables.
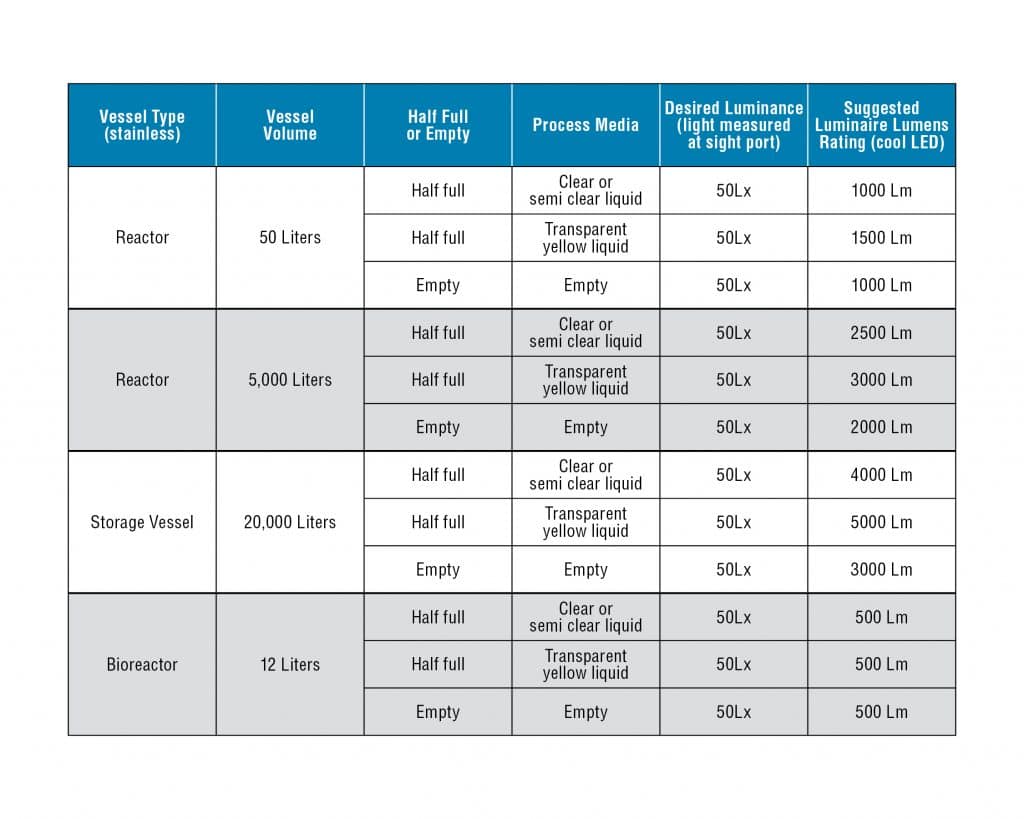
Measuring light at the viewport is simpler, and the light that reaches the viewport is—in a way—the final output of the lighting system. All the variables that affect the light inside of the stainless steel vessel have come into play (as long as the light is not directly shining on the viewport). If the luminaire at the viewport is at some minimum lighting threshold, operators can assume that the inside of the tank is achieving proper illuminance, without completing a complicated equation.
A minimum luminance level is acceptable because the human perception of bright light is surprisingly flat, meaning it takes large quantitative changes in light to produce a noticeable qualitative change in light. Just because a light is brighter by a large margin, it does not mean the change will be noticed easily by a person. Also when human performance is measured at various lighting levels, performance remains fairly constant as long as a minimum brightness is surpassed. If the interior of a tank is over-lighted, then the ability of an observer may not be significantly improved, but if the interior is insufficiently lit, then observation will be negatively affected.
The goal, therefore, is to select a luminaire bright enough to meet the minimum threshold of luminance for reliable observation in a particular application without paying for more lumens than one really needs. The surest answer is to try a luminaire and see how well it works. If the view is too dim, then replace it with a brighter luminaire. A better approach is to measure the luminance of the vessel at the sight port. As these approaches may be impractical, L.J. Star www.ljstar.com, a manufacturer of process vessel luminaires, offers a table of rough guidelines (Table 1).