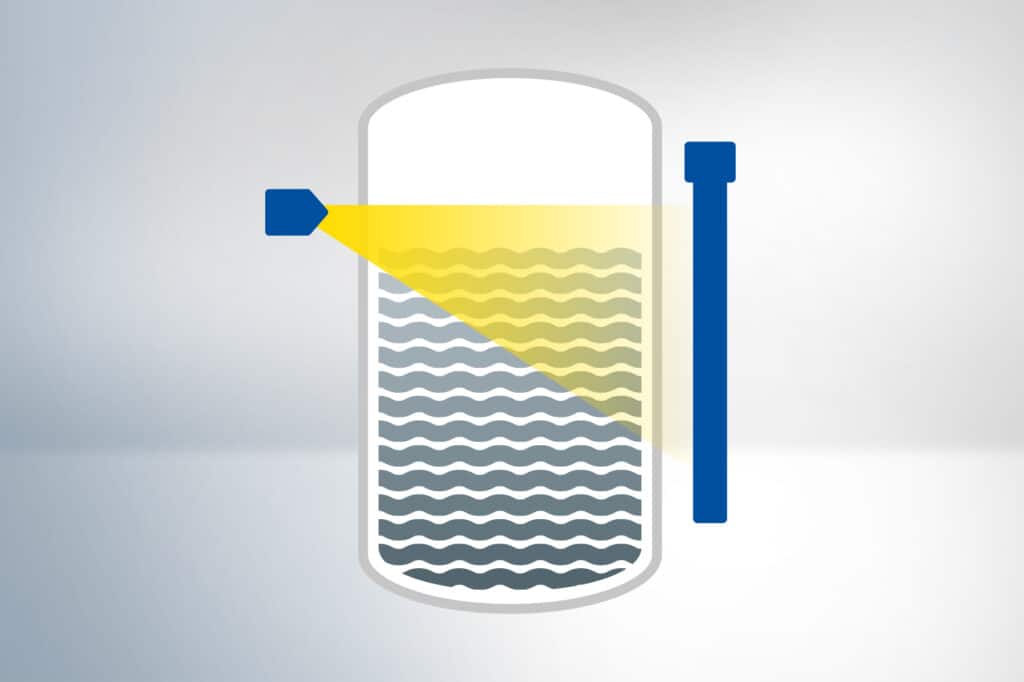
Where other measurement methods reach their limits, the use of radiometric measurements is unrivaled. Radiometric measurements for industrial processes have been in use for several decades and have become a mainstay in performing the most difficult and critical level measurements. Thereby, a typical measurement system consists of two components: a radioactive source and a detector, both mounted on the opposite side of the corresponding vessel (see Figure 1).
Simple, yet sophisticated principle
Radiometric measurements are based on the principle of attenuation. The source emits gamma radiation that penetrates both, the vessel and its contents, and is subsequently detected by the detector. If there is no material in the radiation path, the intensity of the radiation remains almost the same. However, if the radiation has to penetrate matter, it is attenuated. The attenuation increases with increasing density of the penetrated material. Since this principle applies to almost every radiometric measurement, it can be used to determine not only the density of the material in the vessel, but also its level, or to perform a limit switch task.
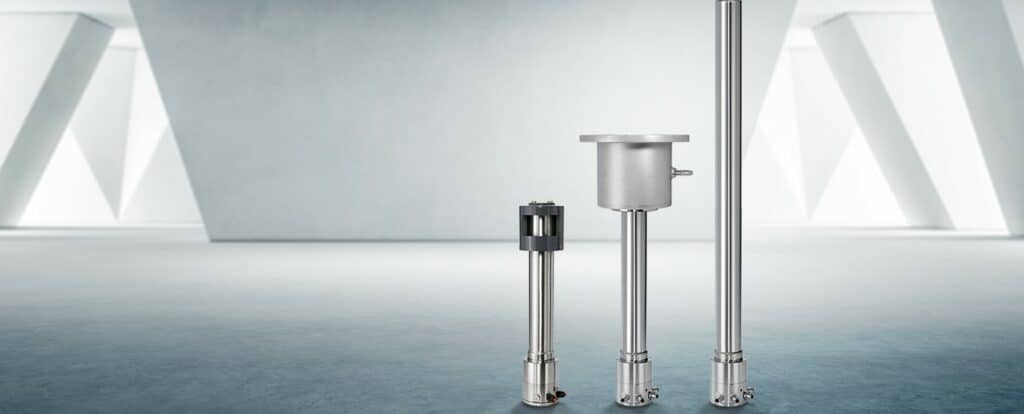
To avoid any unnecessary radiation exposure, the source activities used are designed to be as small as possible and application specific. The radioactive material is safely sealed and housed in a robust, steel-sheathed lead housing as a shield, which ensures safe handling. Due to the design of the detector and the available materials, the scintillation detectors used are very robust and provide reliable and reproducible results even under extreme measurement conditions. In order to choose the right detector for each application and requirement, different detector types with different scintillator sizes (point or rod detectors, see Figure 2) are available on the market.
Level Control, not only of single-phase media
Several layers can make level measurement more difficult, especially if the levels of each individual phase are of interest. For the measurement of more than two phases or of interfaces that are not clearly defined, e.g. emulsions, a more complex measurement system is needed. Such a multiphase level measurement system, like Berthold’s EmulsionSENS, consists of several density measurements installed on different heights with detectors mounted on the vessel outside and sources inserted into a closed dip pipe inside the vessel to create a density profile of the vessel contents (see Figure 3). Based on that and using sophisticated algorithms, levels of the individual layers can be calculated.
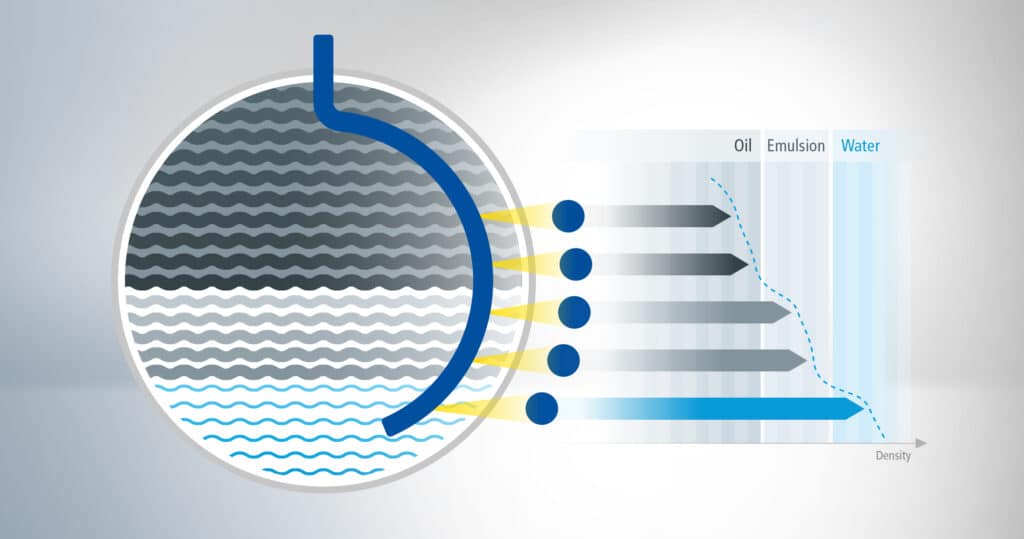
Contactless and yet perfect
For process level control, radiometric measurements are usually the very last option. Of course, the use of radiometry involves a certain amount of work, such as regulatory approvals, but with proper care and compliance with some regulations, this technique offers many advantages that should not be neglected. The radiometric measurement technique is highly reproducible and reliable. The systems are characterized by their wear-free and maintenance-free operation; moreover, a single calibration is usually sufficient during initial commissioning. The advantages of the systems extend over the entire lifetime, starting with the simple installation, which can also be retrofitted to existing vessels without any problems, through the smooth handling and operation, to the very long, reliable and safe use.
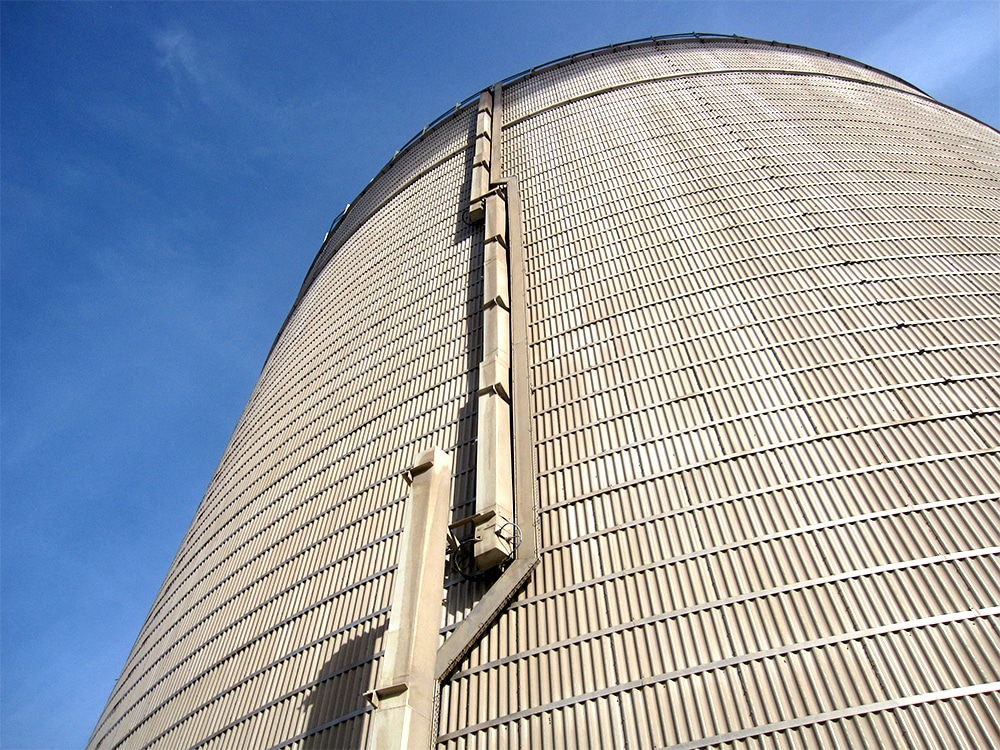
We customize a solution for your application and process, pairing detector length and sensitivity with the appropriate source length, activity, and shielding. We even provide sources which can be inserted into a dip pipe and shields that allow them to be locked out to allow vessel access. Radiometric-based continuous level measurement systems allow measurement ranges from a few millimeters to several tens of meters to be monitored (Figure 4). The measurement experts for process control from Berthold will find a solution to suit almost any vessel geometry, economic concerns, and accuracy requirements.