This paper explains that technology diversification is not a requirement of the relevant industry safety standards, and that there are certain advantages to selecting the same technology for both systems. It describes why radar has become the dominant technology in such applications, with new installations often including two radar level gauges to provide both level and independent overfill prevention measurements. The paper also describes how the latest “2-in-1” technology enables a single radar gauge to be used for both level measurement and overfill prevention purposes, in compliance with industry standards, and how this allows for cost-efficient safety upgrades on existing tanks.
Introduction
The owners and managers of bulk liquid storage facilities depend on accurate and reliable level measurement instrumentation within both their ATG and their OPS. With tanks often storing materials that are hazardous, flammable, or explosive, an overfill can lead to injuries or even deaths, significant damage to assets, and extensive environmental harm. A company’s reputation can be seriously affected, while the cost of such incidents can sometimes be measured in billions of dollars.
It is therefore essential for companies storing hazardous materials to invest in a robust OPS that is compliant with current industry safety standards. IEC 61511 sets out best safety practices for implementing a modern OPS in the process industry. In addition, API 2350 addresses the minimum requirements to comply with modern best practices in the specific application of non-pressurized above-ground large petroleum storage tanks.
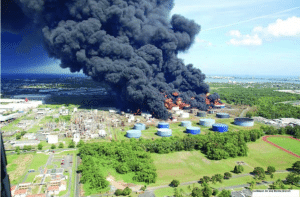
OPS can be either manual or automatic. Manual systems are regarded as being easier to implement and less complex, with lower initial costs. They typically consist of a level sensor or switch that transmits an audio-visual alarm to an operator, notifying them to take appropriate action, such as manually opening or shutting off a valve to prevent an overfill. However, the risk reduction factor of manual systems is limited and there is a strong trend towards replacing them with automatic systems, which can achieve higher risk reduction factors, shorter response times, and a reduced workload for operators. In bulk liquid storage tanks, automatic OPS typically consist of a level sensor, a logic solver, and a final control element in the form of actuated valve technology.
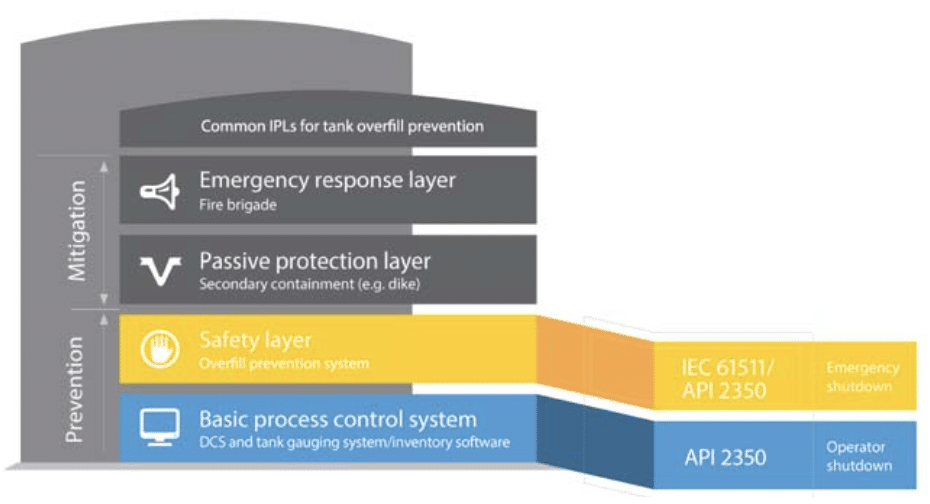
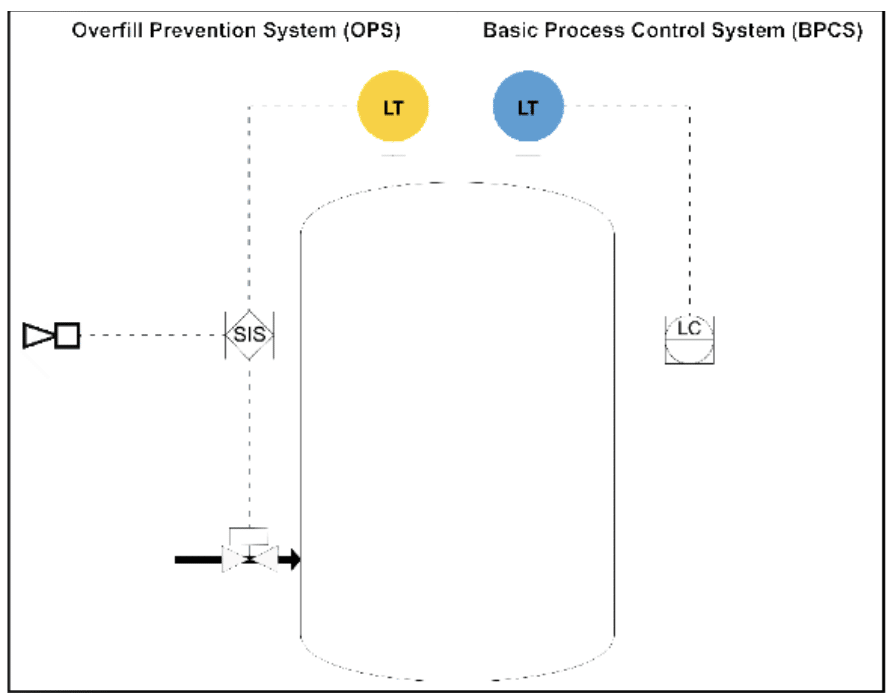
Level switches
Level switches have historically been the technology of choice for the OPS sensor. This type of sensor has a lower initial purchasing cost than continuous level measurement technology, but it does not provide any online measurement, and it is therefore virtually impossible to know whether it is functioning correctly or not. Level switches consequently require frequent on-tank proof-tests. This not only increases the safety risk to workers who need to work at height to perform the tests but is also a labor-intensive procedure that results in tank (and possibly also process) downtime. These are some of the key reasons why the industry is rapidly transitioning from level switches to continuous level gauges in the OPS.
Radar gauges
The dominant level measurement technology for the ATG in bulk liquid storage tanks has for a long time been non-contacting radar. Radar has inherent properties that make it a more suitable choice in tank gauging applications than point-level sensors and less sophisticated continuous level gauges such as servo, or float and tape. The most important properties of well-designed radar gauges are reliability, availability, and safety. Since no regular maintenance or recalibration is required, the availability is close to 100 percent during a device’s long lifespan. If the radar gauge is appropriately designed for safety purposes, the reliability and safety provided is of the highest possible grade, with up to SIL 3 level in a single device.
Radar gauges have been proven to work excellently on virtually all liquids stored in atmospheric tanks, as well as on liquefied gases in refrigerated tanks, including cryogenic tanks. In addition, radar tank gauging has been used successfully on liquefied petroleum gas (LPG) tanks since the early 1980s and is today used on thousands of pressurized tanks worldwide.
Diverse and identical separation
Although radar is often the preferred measurement technology, there is a common belief that industry standards require the technology used for the OPS to be different to the technology used for the ATG sensor. This is typically referred to as “diverse separation” or “diverse redundancy.” However, technology diversification is not a requirement of either IEC 61511 or API 2350.
IEC 61511 refers to the ATG system as a BPCS (basic process control system) and the OPS as an SIS (safety instrumented system). The standard states: “Separation between the SIS and BPCS may use identical or diverse separation. Identical separation would mean using the same technology for both the BPCS and SIS whereas diverse separation would mean using different technologies from the same or different manufacturer.
“Compared with identical separation, which helps against random failures, diverse separation offers the additional benefit of reducing the probability of systematic faults affecting multiple channels at the same time and/or from the same cause and hence reduces correlated failure of multiple channels.
“Identical separation between the SIS and BPCS may have some advantages in design and maintenance because it reduces the likelihood of maintenance errors. This is particularly the case if diverse devices are to be selected which have not been used before within the user’s organization.”
In other words, diverse and identical separation are both valid options, but they provide different benefits. It can be argued, though, that diverse separation introduces extra complexity and increases the likelihood of human error, as personnel need to learn about installing, configuring, and proof-testing two different technologies rather than just one. By some estimates, 75 percent of accidents in industry are traceable to organizational and human factors, so anything that can be done to reduce the likelihood of human error is vital in preventing safety incidents.
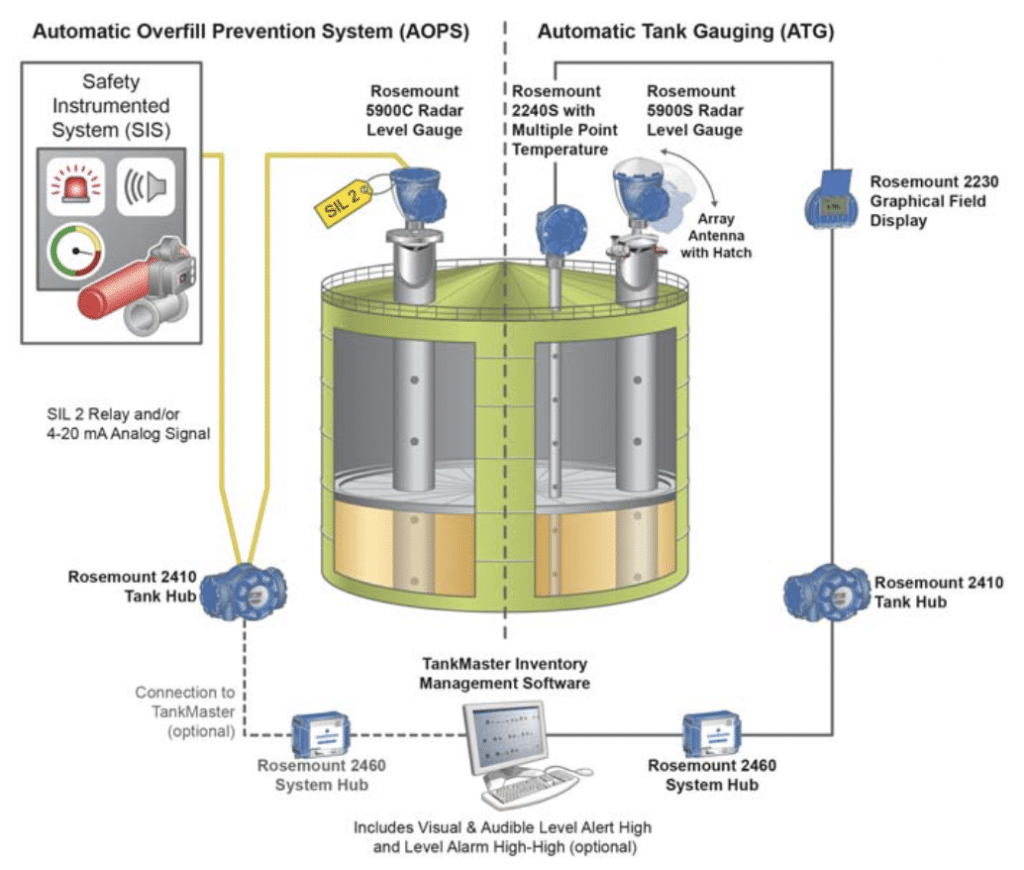
LPG and LNG tanks
The misconception about the need for technology diversification has been most prevalent in applications involving pressurized LPG tanks and cryogenic tanks. A common design requirement is that these tanks must be equipped with one or more tank gauges, where at least one of them serves as a high-level detection device. In some instances, there is a prerequisite that the tank gauging function and the high-level detection shall be of different technologies.
The reasoning behind this demand for technology diversification is often a vague fear that radar level gauges under some undefined circumstances will not work in pressurized tanks with high gas density in the vapor space. This idea is often encouraged by suppliers of mechanical tank gauges, for obvious reasons. However, such fear of gas influence on radar signals is unfounded. Radar is today used on more than 8,000 LPG and LNG tanks worldwide with excellent results and proven track records.
A good indication of the reliability of radar is the fact that during nearly 40 years of service on pressurized tanks, no Emerson radar installation has experienced any safety or reliability related problems due to vapor or high gas density in such tanks. The specially developed LPG radar antenna from Emerson is made to accurately detect tank levels at large gauging distances (>60 m) and at very low dielectric constants of the liquid (< 1.4). It should be noted that Emerson is one of the few suppliers that can accurately gauge liquefied gases with low dielectric constants. Most other suppliers suggest using servo, since they have no suitable radar solution for liquefied gases.
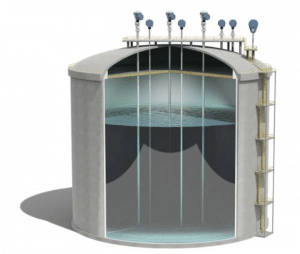
Using radar for both ATG and OPS
Due to the high accuracy and reliability of the latest radar devices, new installations often install two radar gauges to provide both level and independent overfill prevention measurements. Adding a mechanical level gauge for safety purposes can in fact make the system less reliable, as a mechanical system has failure modes that are not detected and can therefore provide incorrect information.
IEC 61511 states: “If identical separation is used, extra care should be taken when determining the required Safety Integrity Level (SIL), and relevant safety data of the sensor should be reviewed thoroughly. If diverse separation is used, extra consideration must be given to operational procedures of the plant. Training of staff in matters relating to installation, maintenance, proof-testing or similar activities that involve handling and configuring the sensor must be extensive and properly documented in order to minimize risk of human errors.”
This means that it is important to have proper safety certification for the safety instruments. When this is in place, the system will be safe when using identical technologies, while the use of different technologies will add to complexity, training requirements and costs.
Two-in-one technology
Although many new installations use two radar level gauges for the ATG and OPS, some existing tanks have practical limitations that make safety upgrades with two separate level gauges cost-prohibitive. These include instances where no additional tank opening is available, and where modifications would require the tank to be taken out of service and result in additional costs.
One solution to this problem is the non-contacting RosemountTM 5900S 2-in-1 Radar Level Gauge, which was developed by Emerson upon request from end users. This device consists of two separate and independent electrical units and a common antenna. When connected with its cables separated in different cable trays and with separate power sources, a single level gauge can be used for both ATG and separate OPS sensor measurements. The most obvious benefit of this configuration is that it requires only a single tank opening. This allows for cost-efficient safety upgrades of existing tanks by replacing a single existing ATG or OPS sensor with two continuous level measurements with a minimum of tank modifications. Often, a radar level gauge with 2-in-1 technology fits the antenna of earlier generations of Emerson devices and therefore requires no tank modifications at all.
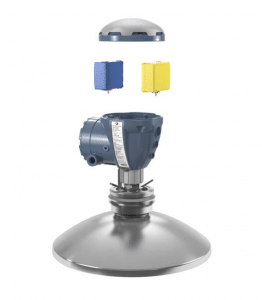
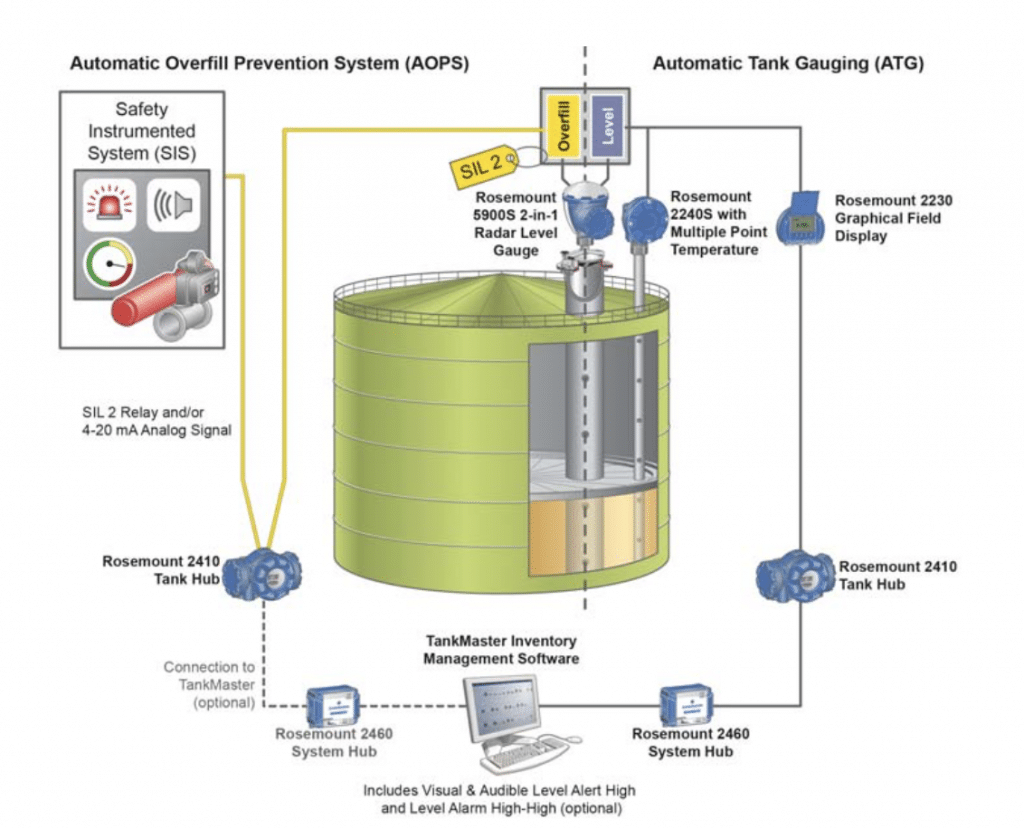
Safety certification
An essential consideration when selecting components for use in a safety system is to ensure that they have the correct safety certification. A safety device should be inspected and tested by a third-party assessor that delivers correct failure data.
Third-party assessor Exida® has verified that the Rosemount 5900S 2-in-1 fulfills the requirements of IEC 61511 to be used simultaneously as an ATG and SIL 2 OPS sensor.
Maintenance and proof-testing
A further consideration when selecting components for a safety system is that the system must be maintained and proof-tested throughout its operational lifespan.
The latest level switches, guided wave radar, and non-contacting radar devices offer significant advantages over older, mechanical technologies through their powerful built-in diagnostics. Monitoring the health of devices in this way ensures they will perform correctly in the event of an overfill. A further advantage of these new devices is the fact that they can be remotely proof-tested. The proof-testing procedure can be initiated from the control room or maintenance room without any need to change the liquid level in the tank and they can therefore be completed within a few minutes. This increases worker safety and efficiency, reduces tank and process downtime, and reduces maintenance costs compared with the traditional proof-testing procedures used by mechanical point-level sensors and less sophisticated continuous level gauges.
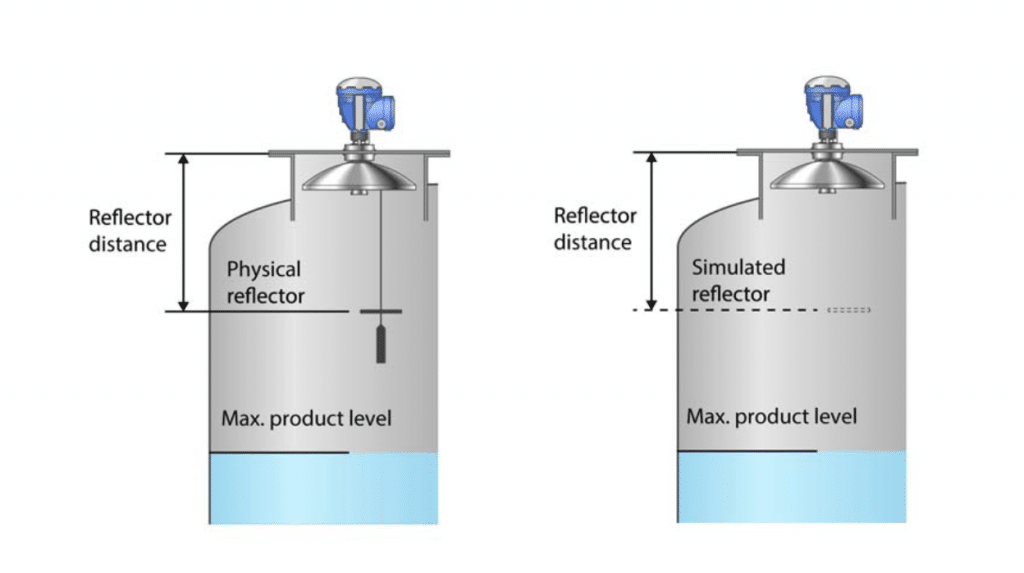
Conclusion
When selecting level measurement technology for use in ATG and OPS on large storage tanks, technology diversification is not a requirement. Mixing technologies may even make the system less safe. It is more important to select reliable safety equipment with proper safety certification, minimal maintenance requirements, and remote proof-testing capability.
Automation suppliers offering a broad range of level measurement solutions are able to guide users on correct technology selection, installation and implementation.
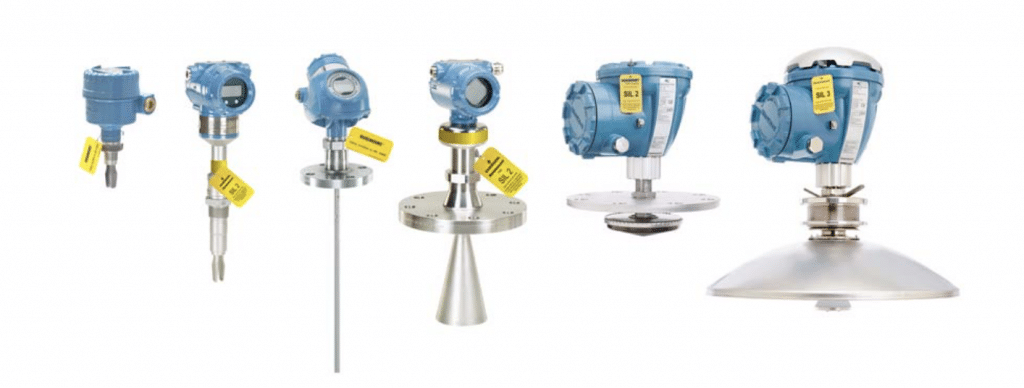