One of the largest hurdles met in the introduction of new technology is typically cost, whether it be direct monetary cost, or indirect costs like loss of efficiency, retooling costs and training costs for operators. When new, more efficient technology is available, the decision to make a change should be simple, and should never need be impacted by excessive switching costs.
The globe valve, the most common control valve option found in the oil & gas, petrochemical, and refining markets, has largely dominated the $10 billion control valve market for several decades. With countless options in regard to size, trim, automation and other factors, the cost for a globe valve can range anywhere from several hundred dollars to more than a hundred thousand dollars for an individual unit.
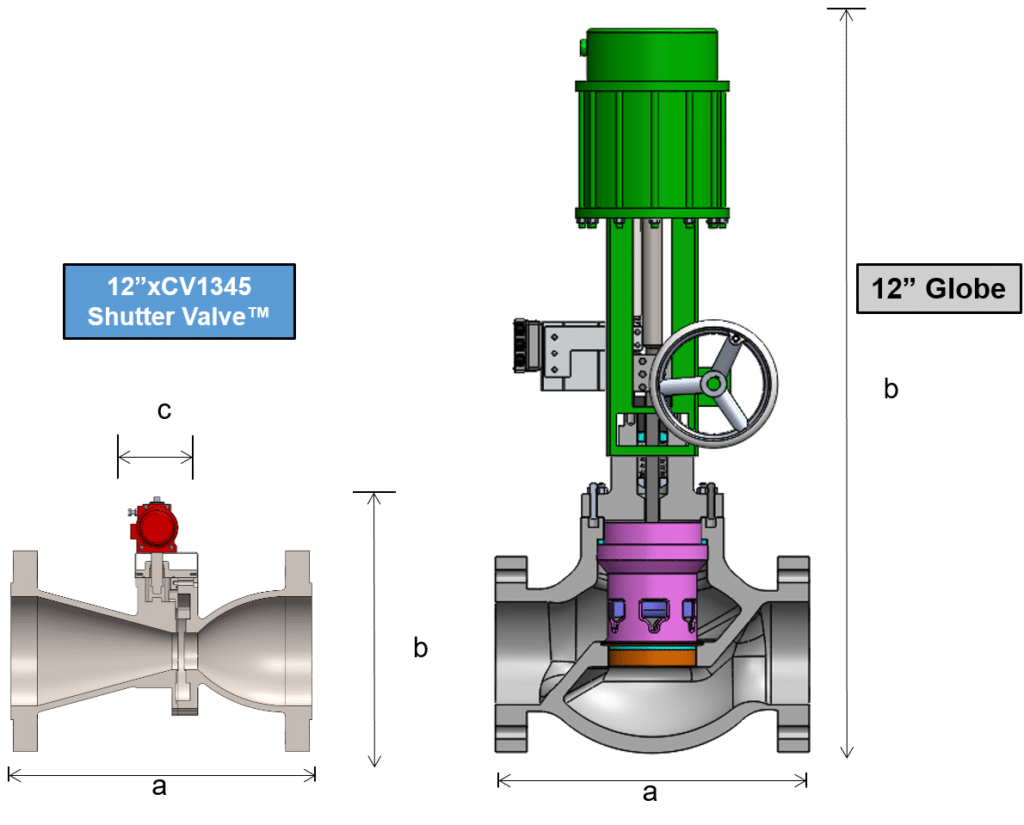
The cost of purchasing and installing hundreds or even thousands of globe valves for a specific project can become very costly for customers, which is why Clarke Valve has engineered their unique Dilating Disk™ as a solution for expensive or emissions sensitive control valve applications.
Dilating Disk™ offers precise flow control at about 20% to 50% of the size, weight, and cost of a globe valve. This valve, designed also to meet the face-to-face dimensions of standard globe valves, has been found to be compatible in carrying out the same functions as their larger, more costly predecessors.
According to ISA 75.08 and ASME B16.10 standards, there are many different defined face-to-face dimensions that exist for control valves. These standards offered Clarke Valve with the opportunity to perfectly match the existing face-to-face dimensions of globe valves, allowing the Dilating Disk™ to minimize customer switching costs by requiring no existing piping to be modified when being installed. Clarke Valve engineered the Dilating Disk™ to be the ideal plug-and-play globe valve replacement, making it easy to service and re-assemble when needed. Once installed, little to no training is required for operators or technicians to maintain these valves. This simple plug-and-play feature makes it easy for customers to upgrade to the Dilating Disk™ with little to no cost when switching out their existing valves.
Due to its unique geometric mechanical design, the Dilating Disk™ can be up to 80% smaller than standard globe valves without compromising the desired flow characteristics. Clarke Valve created the Dilating Disk™ with Aerospace design principles, incorporating unique integral flanged connections between the valve body and each pipe face. The flange design mirrors that of a rocket nozzle, maximizing valve performance and achieving the desired fluid effects necessary for each application.
The Dilating Disk’s straight, tapered upstream nozzle and globe-shaped downstream nozzle (Figure 1, below) delivers a centralized flow stream and minimal corrosion, which dramatically increases the life of the valve body and adjacent piping. This allows each Dilating Disk™ to be rebuilt several times before the valve body requires replacement, significantly lowering the total cost of ownership for the customer.
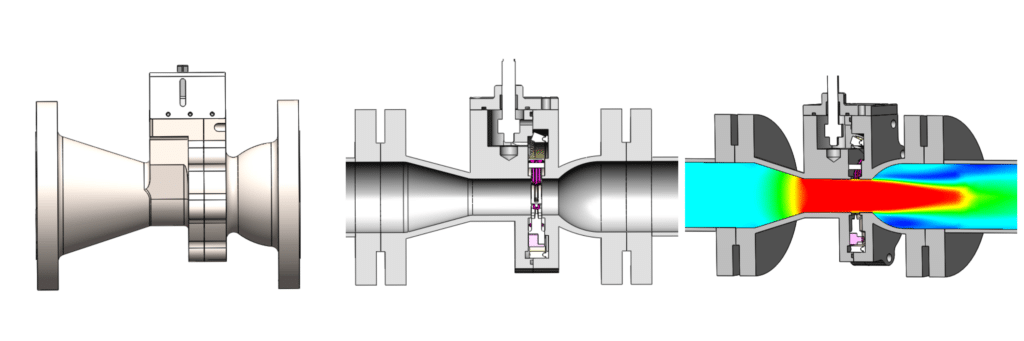
Figure 1: The Dilating Disk™ matches the face-to-face dimensions of globe valves, while the compact body allows asymmetrical upstream and downstream integral flange connections (left). Seen in cross-section (center), the upstream reducer is tapered in a conical design, while the downstream connection is more convex. The resulting flow pattern (right) at 100% open shows that the highest velocity process fluid is traveling down the center of the pipe (red), reducing the potential for erosion of the downstream pipe wall.
In addition to being lighter, smaller, and less expensive than the globe valve, the Dilating Disk™ is also more environmentally friendly than globe valves. The Dilating Disk™ is ISO 15848 and API 641 certified to reduce fugitive stem emissions by 98%, ensuring that not only are oil and gas producers and process manufacturers able to easily upgrade to the Dilating Disk™ with little or no switching costs, but also allowing them to nearly eliminate their emissions.
The Dilating Disk™ is available to be installed in piping from ¼” to 12”, with each valve designed and built with the customer’s specific application in mind.