Monitoring production processes by installing a wide range of sensors including flow, level, temperature, and pressure is common and crucial to be competitive. Although there are many reasons why plant managers decide to install monitoring devices in their process, environmental and regulatory reasons dominate one side of the spectrum, whereas quality, process control and monitoring govern the other.
And if that’s not enough, the marketplace offers many level technologies to choose from. Thus, making the right choice can present many challenges as to what the right technology is if there is not a basic understanding of the principle of operation and what to look for when deciding for a level sensor that best serves the application needs.
A plant can apply several level technologies to conform to external requirements to provide accurate data for wastewater and sewage discharge, as well as meet internal criteria for monitoring the use of raw materials, keeping track of stored additives or maintaining a consistent quality.
Ultrasonic technology has many applications in a processing plant. It is praised for its versatility, accuracy, and reliability. However, as with any process instrumentation for level or flow measurement, understanding the technology is essential for achieving measurement objectives and avoiding misapplying the technology.
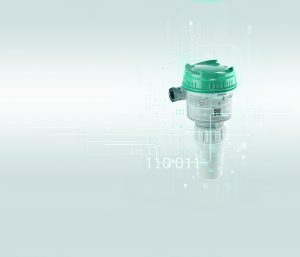
Measuring and controlling the level in storage vessels and sumps and monitoring the flow in open channels helps managing your process more efficiently. Furthermore, continual data collection offers the potential for process optimization, i.e. evaluating historical trends that show excess demand of materials that don’t correspond to expected usage. Simply put, with flow measurement, you know how much material is incoming, outflowing or both. With automated level measurement, you know how much material or feedstock is in your inventory continuously or at any given time. Thereby avoiding shortages, material spills and the associated fines.
Choosing the best technology to measure any application depends on many factors. These include, but are not limited to, characteristics of the material to be measured, geometry and characteristics of the container, process conditions, environmental conditions, as well as customer needs regarding cost, maintenance, and accuracy.
Ultrasonic technology basics
Sound can be used as a measurement tool because there is a measurable time lapse between sound generation and the sound being “heard”. By monitoring this time difference, and interpreting the data, it can be converted into useful information. For non-contacting level technology, this is known as the time of flight principle. What this means is that the signal from the ultrasonic device signal travels through air and obtains a measurement off the material being measured without contacting it. To perform this task, three components are required: a transducer and a transmitter, or processor, and a medium to carry the sound.
The processor is required to calculate the time lapse between the transmitted and the received signal. This time is used to determine the distance from the transducer to the material surface from which all other process values can be derived: level, space, volume or flow.
Factors affecting ultrasonic measurement
There are a few factors that affect ultrasonic technology. The most common factors are temperature, pressure and volatiles (substances that readily vaporize, thereby affecting how the ultrasonic signal propagates in the medium). Temperature changes affect the velocity of sound, and the variations in temperature require compensation to calculate accurate measurement. These temperatures variations however are easily monitored by modern ultrasonic transducers by means of an integral temperature sensor. The transmitter or level controller makes speed of sound compensations based on the temperature sensor data.
The speed of sound is also affected by pressure. However, ultrasonic transmitters and transducers are to be installed in vented or non-pressurized vessels. More can be said about is if reference is made to Boyle’s Law for ideal gases. But it suffices to state that if a level measurement in a pressurized or a vessel under vacuum is needed, that radar technology needs to be considered instead.
Besides the factors mentioned above, signal attenuation takes place with any level instrument regardless of the technology. High concentrations of dust, humidity, steam, and the location where the instrument is installed can contribute to some signal loss. In general, there is still enough signal power left under these conditions and the experienced attenuation often does not preclude getting a valid measurement. Under extreme cases, a more powerful transducer is generally the answer to address these types of conditions. Not only a larger transducer has more power, but in general, larger transducers have a narrow beam signal spread. This naturally minimizes side interference from tank walls, seams, ladders and other obstructions; thus, the effect of signal degradation is reduced.
As it pertains to the location of the transducer, it is important that nothing obstructs the signal path. A transducer must be able to “see” the material being measured. Since the ultrasonic pulse radiates in a conical fashion from the face of the transducer, obstructions need to be kept out of the signal path to reduce the chance of false signals being interpreted as the material level. An exception to this is agitator blades used for mixing materials in tanks or vessels. Advanced transmitters have algorithms that help discern reflections from active mixers and the surface of the feedstock or material.
Ultrasonic instrumentation
As mentioned above, ultrasonic level and flow measurement instrumentation requires three components, one to generate the sound and receive the signal (transducer), one to interpret the data (the transmitter or processor), and a medium to propagate the sound.
The transducer
Today’s level measurement transducers are constructed with advanced material compounds for use in a wide range of applications and chemicals. Level measurement requires only one transducer unless a differential level measurement is required. The latter application requires a controller capable of driving two transducers. When taken a measurement, the transducer first serves as a transmitter by firing ultrasonic pulses into the air space between sensor and target. The signal travels to the target and then is reflected to the transducer. The transducer then acts as a receiver and the sonic energy is converted back into an electrical signal. One key feature of this electro-mechanical energy is that it causes the transducer face to vibrate. This gives the transducer a self-cleaning property that helps reduce the effects of condensation and buildup on the transducer face, thereby minimizing cleaning and maintenance for proper operation.
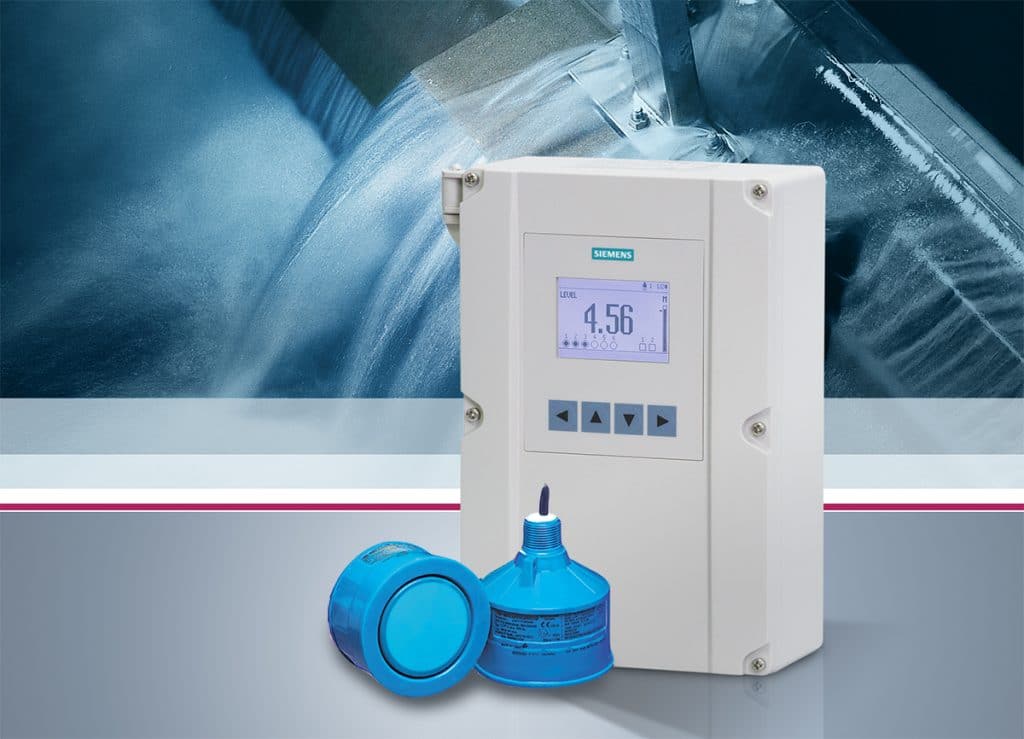
The processor
Today’s ultrasonic transmitters and controllers are microprocessors-based systems and as the echoes or signals are received by the transducer, they are digitized and stored as echo profiles by the in the main electronics. The processor analyzes the profiles using software algorithms, it extracts one signal from the profile as the most probable to be the target signal and then converts the time differential between the transmitted and received signal into usable information. The microprocessor does this by applying software filtering techniques that remove unwanted acoustical and electrical noise from the signal profile. Electrical noise is commonly present in industrial environments due to variable frequency drives used with motors. This digital process significantly improves the received data and hence, the accuracy, reliability, and overall performance of the ultrasonic device.
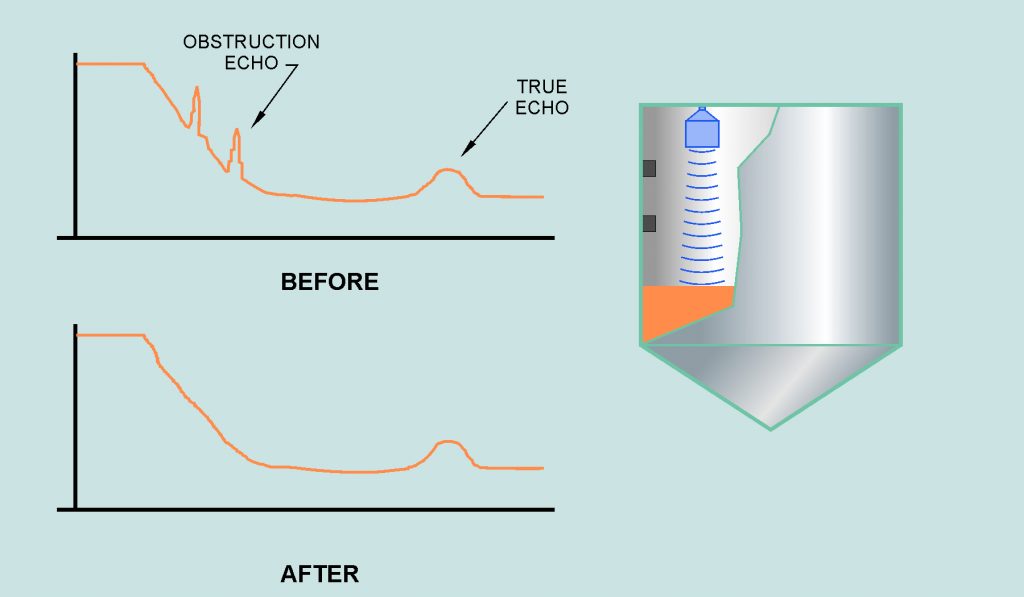
Understanding the application is key
To obtain a reliable level or flow measurement, understanding the application pays good dividends performance wise. Specific factors need to be considered no matter what the application involves. Start with what type of measurement is required: level, volume, differential level or flow. Consider the chemical compatibility with the wetted parts, the pressure (is it a vented vessel?) and temperature of the process. Determine the dimensions and shape of the tank, internal obstructions, and the details about process connections (height and width of standpipe if any). For example, a narrow and tall vessel may require a transducer with a long range and a narrow beam signal to avoid detecting hanging or protruding objects in a tank, pit or sump. Thus, when selecting a transducer, the most important criteria are the application’s range and chemical compatibility and maximum process temperature. Additional considerations include whether the device is located inside a building in a controlled climate or outdoors in harsh weather conditions. If the transducers are subject to blazing sun such like in an open channel flow application, a sun shield for the transducer is advisable. The idea here is to make sure the integral temperature sensor monitors the surrounding air temperature of the application (to compensate for the speed of sound) and not its elevated temperature due to the exposure to direct heat from the sun.
For the most part, these considerations apply to many instruments regardless if the technology is ultrasonics, radar, capacitance or guided wave radar. To simplify matters, ultrasonic technology is well suited for a wide range of level and flow applications in the industrial and environmental market. Therefore, is more practical to determine where this technology can be challenged. Thus, if the application at hand contains solvents (vapors due to volatiles) or lots of dust or temperatures below -40F or above 200F or if the vessel is pressurized or there is not a medium for signal propagation (vacuum) or it is a long range (beyond 50 ft), then other technologies are more appropriate such as radar or possible guided wave radar (with extreme caution in long range applications).
Major benefit is versatility
There are many factors that need to be taken into account when assessing which measurement technology is the right one for a given application. External as well as internal factors should all be taken into account before making an educated choice. Ultrasonic technology is versatile, for use in many applications in a processing plant. Its applicability is diverse as long as the few limitations mentioned above are recognized. Advanced ultrasonic processors integrated with the plant control system allow operators to remotely manage pumps and other aspects of plant operation from the comfort of a central control room. Level instrumentation offers a reliable technology that has proven itself over decades across many industries and applications. Due to nature of the electro-mechanical transducer, its inherent self-cleaning capabilities makes this technology low maintenance. Understanding ultrasonic technology and understanding the right fit for the application is key to successful use of this cost-effective measurement technology. Furthermore, automation efforts by means of instrumentation eliminates the uncertainty associated with manual process. Having a hold on what inventory levels are at all times and how much is flowing from point A to point B is a good recipe for process improvement and money saving endeavors.
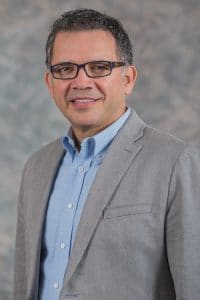
Herman Coello is the Level Marketing Manager for Siemens Industry, Inc. Based in Arlington, Texas, Herman is responsible for business development and marketing of radar, guided wave radar and ultrasonic level instruments. His experience with level instrumentation spans over 25 years. Herman has been heavily involved with radar and ultrasonic level technologies training customers, sales representatives and marketing Siemens radar transmitters and ultrasonic and transmitters and controllers that serve the oil and gas, food and beverage, water and waste water, chemical, power, cement, aggregate, and mining industries. (Phone: +1 (817- 412-9667) Email: herman.coello@siemens.com