MBBR is exceptional when it comes to factors such as convenience, efficiency and flexibility.
This article will closely examine the MBBR process, explaining how it works, how it compares to other techniques and how various industries apply it.
WHAT IS BIOLOGICAL WASTEWATER TREATMENT?
Before explaining the ins and outs of MBBR, it’s helpful to understand the general category this type of wastewater treatment falls into. MBBR is a biological process, as opposed to a chemical or mechanical one. Here’s a technical breakdown of what characterizes a biological process.
Biological processes for treating water use small organisms like bacteria or nematodes to aid in decomposing waste. Consider all the organic matter that is present in wastewater. Biological processes take advantage of natural cellular processes to decompose this waste.
Introducing specific microorganisms into the wastewater allows nature to take its course as these microorganisms break down and consume the waste they contact. In the case of complex waste materials in the water, the microorganisms can turn them into simpler substances, which can then get filtered out through further treatment.
In many cases, biological wastewater treatment the next stage after a primary treatment process has already taken place to remove certain materials. Additional processes may come into play after a biological process, as well. Whether used independently or as part of a more comprehensive water treatment process, biological wastewater treatment processes are effective, eco-friendly and economical.
WHAT IS MBBR WASTEWATER TREATMENT?
Having covered the basics of biological wastewater treatment, it’s time to shift focus to a specific biological treatment method: moving bed biofilm reactor.
Norwegian researchers developed MBBR technology in the late 1980s and early 1990s. The goal of MBBR was to compensate for some of the issues that characterize other biological wastewater treatment methods, and it did so effectively. MBBR combines many of the strengths of biological processes, specifically anactivated sludge process and biofilm media, while eliminating or minimizing the shortcomings that tend to come with biological processes for wastewater treatment.
Because of the many benefits it offers, MBBR has become a popular mode of biological wastewater treatment. MBBR uses plastic carriers covered in biofilm to decompose waste. In addition to being an effective means of removing organic substances, MBBR is also an innovative method for nitrification and denitrification.
As with other biological treatment processes, MBBR is often part of a multi-step system for wastewater treatment, with other processes focused on different aspects of purification. That is why an MBBR process flow diagram will often include other steps, such as grit removal and disinfection. Individual plants can customize the MBBR process itself and their overall wastewater treatment regimen to properly address their purification needs.
HOW DOES MBBR WASTEWATER TREATMENT WORK?
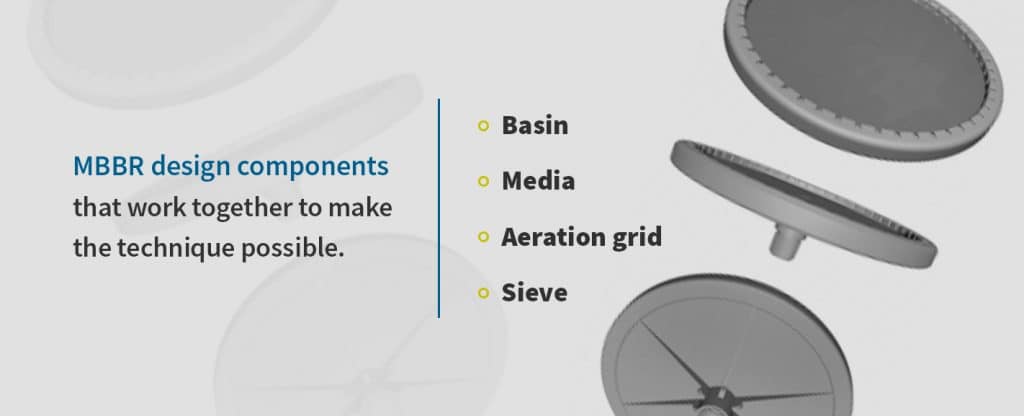
Here is a more detailed breakdown of how the MBBR process works. One helpful way to understand this process is to consider the different MBBR design components that work together to make this technique possible.
- Basin: The MBBR process takes place in a basin, also known as a reactor or as an aeration tank. The size of this receptacle depends on the filtration needs of a particular plant. Influent enters this basin for treatment, and may enter a second basin for further MBBR processing or for another type of water treatment process. MBBR aeration tanks are open at the top, exposing the water to the open air, which makes this an aerobic process of filtration.
- Media: The basin is full of thousands of small plastic chips, called media or carriers. These media may occupy as much as 50 to 70% of the tank. Their design maximizes the surface area they provide for biofilm to grow on them. Many carriers resemble rotelle, or wheel-shaped, pasta. They mimic the density of water, allowing them to mix throughout the fluid, rather than floating or sinking.
- Aeration grid: Another thing that helps the media move effectively throughout the tank is an aeration grid. This device is essentially a fan located at the bottom of the reactor tank. The aeration grid helps keep carriers on the move so they can come into contact with all the waste present and efficiently decompose it, and it introduces more oxygen into the tank.
- Sieve: When picturing the MBBR system described thus far, one might wonder how the media stay in the tank, rather than escaping through the exit. That would be a problem if it weren’t for a sieve attached to the tank. The mesh material allows water to pass through, but keeps the plastic carriers inside the basin.
With an appreciation of the components that make MBBR possible, it’s straightforward to understand how this process works. The microorganisms attached to the media in the tank consume waste in the water, leaving it cleaner and safer for reuse or disposal. The type of microorganisms introduced into the tank will depend on what type of waste needs to get eliminated.
As previously mentioned, MBBR doesn’t just work to consume general waste. It also plays a role in nitrification and denitrification. Nitrification is the process of ammonium converting into nitrate, and denitrification occurs when oxygen gets metabolized and nitrate turns into nitrogen gas. Because these are both biological processes, MBBR is an excellent way of facilitating them.
Again, the goals of the MBBR process will dictate the types of microorganisms introduced. In the case of denitrification, for instance, it is best to use denitrifiers such as Pseudomonas, Paracoccus or Alcaligenes.
In any case that requires a biological process to improve the quality of wastewater, MBBR is a valuable method to consider.
WHAT ARE THE ADVANTAGES OF MBBR WASTEWATER TREATMENT?
Using moving bed biofilm reactors over other, traditional wastewater treatment processes can be a strategic move for many industries, since MBBR comes with a host of exceptional qualities.
- Compact: MBBR is an excellent option for facilities with space constraints, since it typically has a much smaller footprint than other systems. An MBBR aeration tank can effectively treat the same amount of water as a much larger tank used for a more traditional process. Primarily, it offers this benefit due to the maximized surface area the media provide for biofilm growth.
- Simple: Another practical advantage of MBBR is that it is a relatively straightforward process. MBBR allows nature to take its course, which minimizes the role of the operator. It is worth noting that operators must be knowledgeable about the process so they can ensure everything is working properly at the molecular level. However, the process itself does not require very many steps.
- Low maintenance: MBBR is also known for being a low-maintenance process. Maintenance tasks like backwashing that an operator would have to perform in other cases are typically unnecessary with MBBR. This system is largely self-moderating, so users can trust it to operate effectively without the need for demanding, ongoing maintenance.
- Flexible: MBBR is naturally able to adjust as needed to varying loads and changes in the influent, since the microorganisms on the carriers respond to changes. It allows MBBR systems to resist shock loading or a sudden spike in pH levels. A 2014 study of MBBR demonstrated the system’s ability to remain highly stable when faced with organic, hydraulic and salt shock loadings and to quickly return to normal.
- Efficient: One of the most significant advantages of MBBR is its impressive level of efficiency. An MBBR system can work much more quickly than alternative methods to treat the water. The hydraulic retention time (HRT) for BOD and nitrogen removal with an MBBR is around three to four hours. The continuously moving media and the sheer amount of biofilm make this low HRT possible.
HOW DOES MBBR COMPARE TO OTHER BIOLOGICAL PROCESSES?
Having discussed biological processes of wastewater treatment, and the distinctive advantages of MBBR, it’s still beneficial to note how MBBR compares to other biological processes. Many plant operators or consulting engineers who are interested in MBBR are currently using other biological processes in their treatment of wastewater, so it’s helpful to make some direct comparisons.
There are many types of biological wastewater treatment processes, but two of the most popular modes of aerobic biological wastewater treatment are activated sludge and trickling filter.
ACTIVATED SLUDGE PROCESS VS. MBBR
The activated sludge process (ASP) shares some similarities with MBBR. With this traditional process, wastewater enters an aeration tank that contains high levels of oxygen. This oxygen aids in the process of microbial growth and decomposition of organic waste. The water then moves onto a settling tank, where the remaining waste in the water will separate from the water, leaving it cleaner.
The activated sludge process is a tried-and-true method for biological wastewater treatment. However, research has shown that, under optimal conditions, MBBR can more effectively remove chemical oxygen demand and can more effectively handle organic loading compared to ASP. MBBR takes advantage of the same strengths ASP provides and offers additional benefits that make it superior technology.
TRICKLING FILTER PROCESS VS. MBBR
Another popular treatment is the trickling filter process. This process uses a bed of material, such as gravel, rocks, ceramic or plastic, to hold onto microorganisms in water as it passes over the layer of material. These microorganisms will create a biofilm over time that will then decompose organic matter contained in wastewater. Periodically infusing oxygen into the water can make the environment more aerobic.
This process cannot compete with MBBR when it comes to efficiency or ease of operation. In the case of trickling filter processes, a skilled operator must closely monitor the process. Clogs are a common issue with this process, but they rarely happen in the case of MBBR.
INDUSTRIAL APPLICATIONS OF AN MBBR SYSTEM
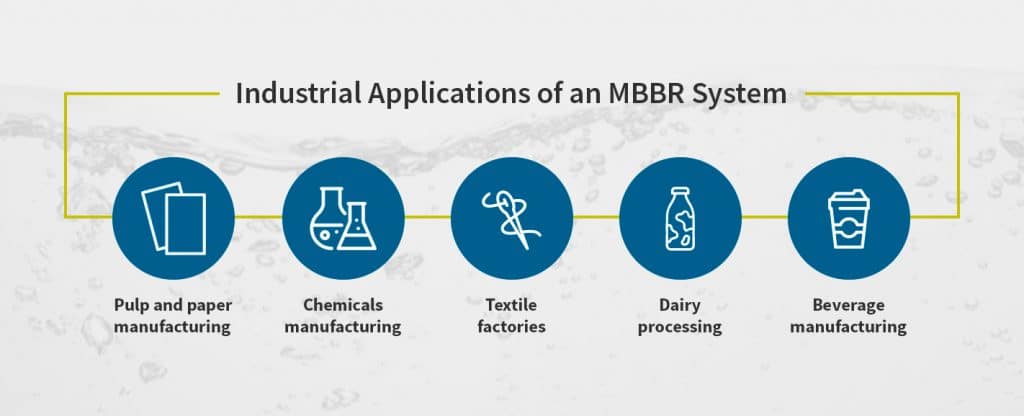
MBBR has nearly limitless industrial applications. Any industry that needs to treat wastewater can benefit from MBBR. Many of these industries have effluent treatment plans (ETP) that use less convenient or less effective processes. The following represent a few examples of MBBR systems in industrial contexts.
- Pulp and paper manufacturing: The pulp and paper industry places high demands on water. Around 85% of this is process water, which means paper factories produce a great deal of contaminated wastewater that requires on-site treatment. MBBR has proven itself to be an effective means of treating this wastewater.
- Chemicals manufacturing: Manufacturing chemicals produces a high quantity of wastewater containing organic pollutants. This wastewater requires treatment before it can get reused or released into the natural waterways. MBBR is an excellent option for chemical manufacturing plants to consider as part of their ETP.
- Textile factories: Textile factories must have ETPs, since they produce wastewater that needs purification. MBBR is an excellent option for textile factories. It can remove dyes and other pollutants effectively and is compact enough to be manageable for small facilities.
- Dairy processing: Processing dairy products such as milk, cheese and yogurt creates a large volume of effluent containing biochemical oxygen demand (BOD), among other types of waste. MBBR is a valuable wastewater treatment option for the dairy industry, since it’s exceptionally efficient.
- Beverage manufacturing: Water is a primary ingredient in most beverages, but beverage factories also use water to processes such as cooling and cleaning. These processes result in wastewater that needs treating. MBBR is especially well-equipped to keep up with the high volume demand for water treatment in this industry.
A vast array of industries need to treat wastewater, so examples of MBBR’s industrial applications abound. Across many different industries, plant operators and consulting engineers have discovered firsthand how valuable MBBR can be as part of their ETP.
TAKE ADVANTAGE OF CUTTING-EDGE AERATION TECHNOLOGY WITH SSI AERATION, INC.
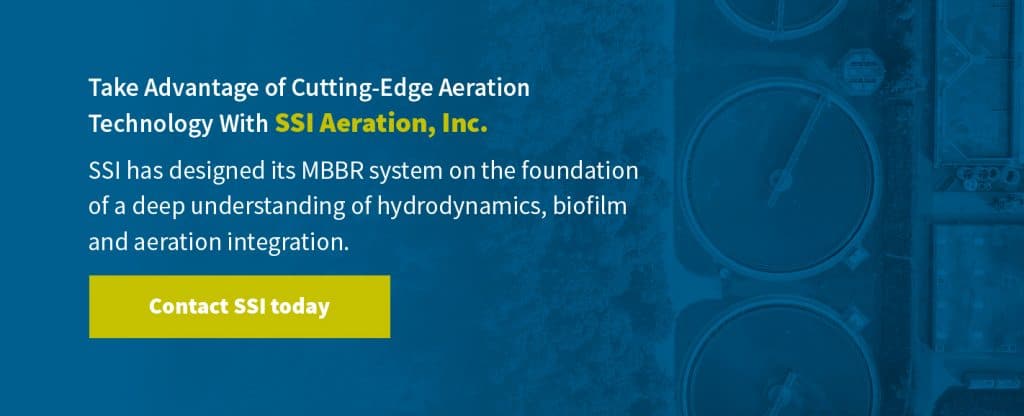
Moving bed biofilm reactor technology has made waves for the way it combines the strengths of preexisting biological wastewater treatment processes and improves upon these processes to offer a simple, low-maintenance process that responds effectively to fluctuations and efficiently treats wastewater — all within a compact system.
To take advantage of this cutting-edge technology, consider the EEVolved MBBR from SSI Aeration, Inc. SSI are trailblazers in the field of wastewater treatment, with a reputation for excellence. SSI has designed its MBBR system on the foundation of a deep understanding of hydrodynamics, biofilm and aeration integration. There are no one-size-fits-all solutions with SSI. Users of the EEVolved MBBR can customize it to meet their facility’s needs. Those interested in learning more about this system and its costs can get a free MBBR quote from SSI today.
SSI’s representatives are also available to answer any remaining questions potential customers have about this process or other wastewater treatment processes of interest. Contact SSI today to learn more about the revolutionary benefits of MBBR.
AUTHOR
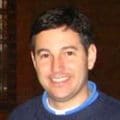
Tom Frankel
Mr. Frankel co-founded SSI in 1995 with experience in design and distribution of engineered systems. He is in charge of sales, marketing and operations in the company. Mr. Frankel holds multiple US patents related to diffusers. He is a graduate of Washington University in St. Louis.