When selecting fluid system valves, the type of hydraulic valve chosen can make a critical difference in the consistent operation and service life of that equipment. Changes in flow and pressure in one part of the system can have grave consequences for downstream equipment. Ongoing pressure fluctuation can increase component wear and drastically shorten pump life.
Guided piston valves have unique flow and stability characteristics that provide reliable performance without chatter. Understanding the relative advantages of guided piston valves will ensure long pump and system equipment life.
Understanding Valve Types
The terms pressure safety valve and pressure relief valve are often used interchangeably. On the face, they both perform the same function–let off pressure when a system becomes over pressurized–but when and how they function is very different.
A standard pressure safety valve is most often used on systems to meet ASME SEC VIII requirements for safety. It is actuated by inlet static pressure and characterized by rapid opening or popping action.
A safety valve opens only in the event of a system failure. Pressure in the line is allowed to build until the valve reaches the set point. Then the valve opens fully, to reduce the pressure as quickly as possible. This tight shut-off safety valve meets ASME’s basic requirements, and protects people, equipment, and facilities from catastrophic overpressures, but does little to protect downstream equipment from ongoing transient pressures.
In contrast, a pressure relief valve is intended to control pressure in a system, ideally preventing systems from reaching the extreme pressures that would activate a pressure safety valve. While a pressure safety valve has two operating settings: totally closed or fully open, a pressure relief valve modulates, opening in proportion to the increase in system pressure.
The relief valve doesn’t open fully in response to increased pressure; it opens gradually, until the system returns to a preset pressure level. When the set pressure is reached without blowdown, the valve closes again. A pressure relief valve maintains consistent system pressure, reducing strain on downstream equipment. As pressure and friction build inside a pump, temperature rises, creating vapor that can lead to cavitation which eats away at the impeller and casing. Increased temperatures also compromise the integrity of mechanical seals and bushings. This leads to cracking and scoring and causes the seal’s elastomers to burn up. Over time, this component damage puts the pump at risk for failure.
In short, a pressure safety valve is a last resort failsafe, a pressure relief valve is a best practice safeguard–a “work-horse” valve to control constant line pressure.
Relief Valve Operation
There are a number of pressure relief valve types available-some of the most common are spring activated ball, poppet, and guided piston valves. They all operate in the same basic way, fluctuating on a spring to maintain the set pressure:
- The system pressure reaches a predetermined set limit (cracking pressure), the relief valve will open to divert some of the liquid flow away from the process.
- As pressure on the system increases, the valve will continue to open further, allowing more flow to be diverted.
- As the fluid is diverted, the pressure on the system will stop rising, maintaining a set pressure to the downstream flow.
- As upstream pressure decreases, the valve will gradually close, shutting fully when pressure reaches a few psi below the set pressure.
Because of the relative drawbacks of ball and poppet valves–most notably their noisier operation, flow limitations and unsuitability for continuous duty operation–guided piston valves are generally considered the superior relief valve option. The remainder of this paper will focus on the benefits and selection of guided piston valves.
In guided piston valves, the opening and closing action described above is operated by a spring loaded piston, which is self-modulating. It functions consistently, and modulates, at any degree of opening and closing. This self-modulation is pressure actuated and self-powered; it does not require any external sensing or control systems for operation.
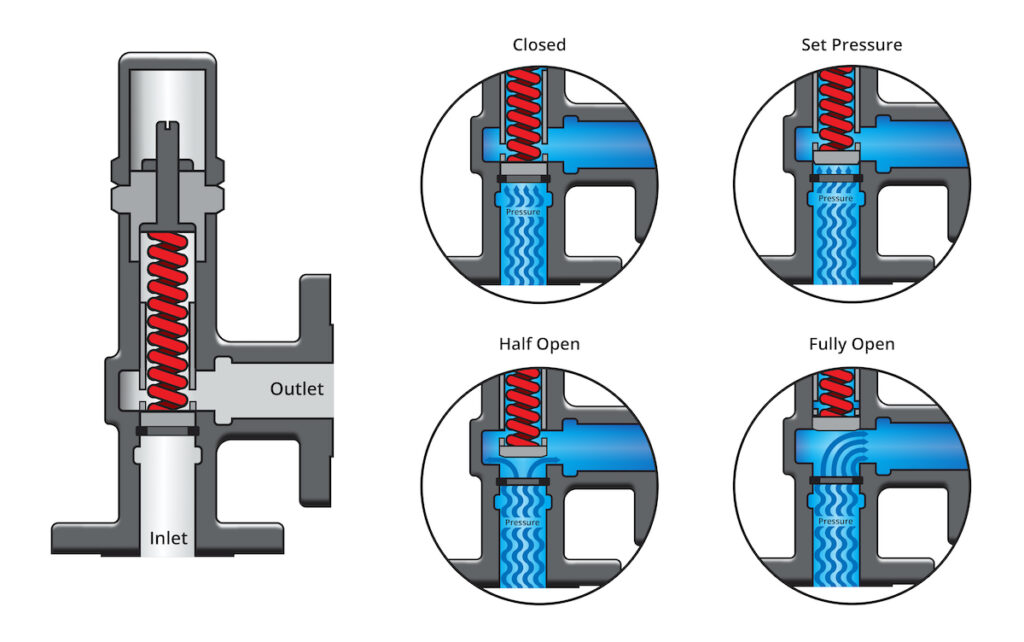
Designed to operate reliably at pressures as low as 3 PSI and as high as 1000 PSI, guided piston valves reduce velocities through all but the controlling interface of the valve, thereby minimizing system power loss, preventing equipment damage and costly system shut down. The valves provide a constant pressure unaffected by transient pressure surges, providing smooth and reliable line pressure.
Other Guided Piston Valve Advantages
Guided piston valves operate effectively with all types of liquids in the full range of viscosities, including hydraulic oils, water, solvents and chemicals. For equipment destined for outdoor use temperature can play a significant role, as engine oil and hydraulic fluids thicken appreciably on cold days, and become less viscous on warm days. Oxidation, moisture, and ordinary wear can also contribute to significant changes in viscosity over time. The guided piston valve’s immunity to viscosity makes it an ideal choice for many applications.
When designing fluid systems, there is always a tradeoff between function and size, making the most of available space. A hallmark of the guided piston valve is providing large flows without excessive bulk. Furthermore, as guided piston valves can be mounted in any position,
without affecting performance, they can easily be worked into systems where space permits, enabling more compact equipment footprints. The availability of NPT, flange, socket weld, and SAE threaded connection types further increases the range of installation possibilities.
As mentioned above, unlike other direct acting relief valves, guided piston valves are less responsive to transient pressure surges, thereby eliminating the tendency to pound, squeal or chatter. Quiet, stable, efficient performance is assured in both load regulation and system protection applications. Guided piston valves can significantly reduce equipment noise pollution.
Use Case: Protecting Pump from Deadheading
In the diagram shown below, a typical process using either a centrifugal or positive displacement pump has a manual shutoff installed after the pump in the line leading to the loading zone. When the loading operation closes this valve without warning, considerable pressure builds in the line leading back to the pump, creating strain on the pump and risk for deadheading.
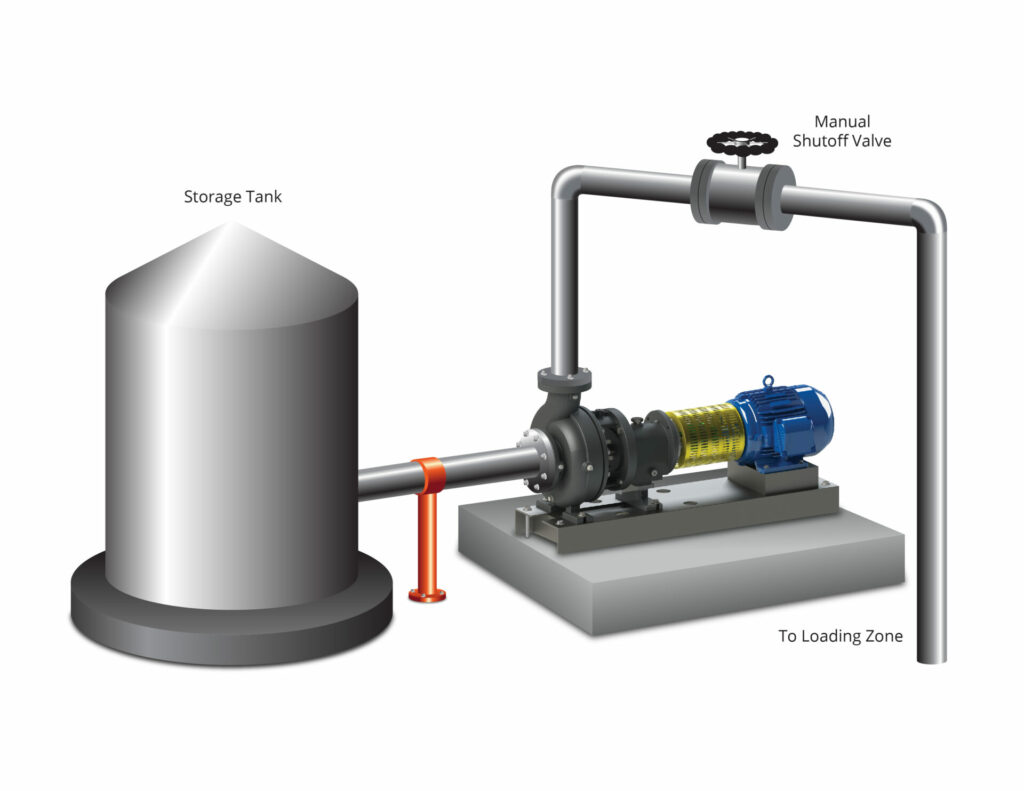
The solution is to add a pressure relief valve to protect the pump. A new recycle line with a pressure relief valve is installed between the pump and the manual shutoff valve. When the manual shutoff valve is closed and pressure begins to build, the guided piston valve activates automatically, diverting flow back to the tank and relieving pressure on the line to the pump. When the shutoff valve is reopened, and the pressure on the line returns to normal, the pressure relief valve returns to the closed position automatically.
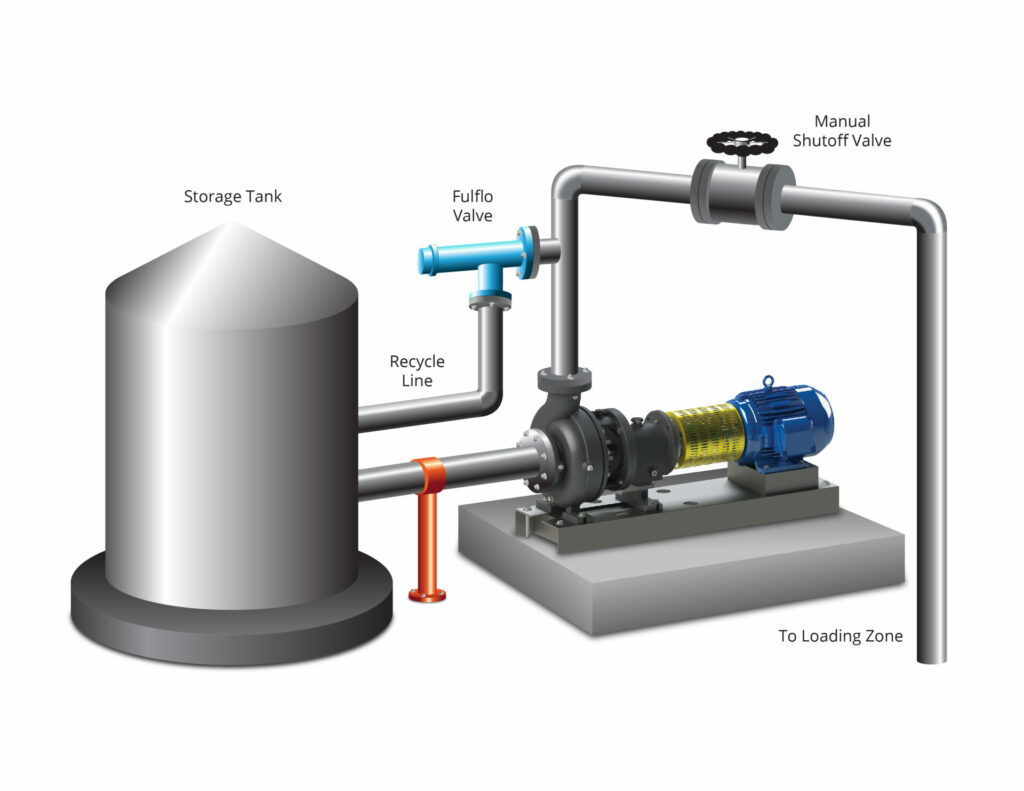
As this is a guided piston relief valve, the orientation of the valve does not impact the valve operation or set pressure. It can be mounted upright, sideways, or even upside down-however space permits. This is a unique characteristic of the guided piston valve and provides a lot of design flexibility in retrofitting problem processes.
Conclusion
While pressure safety valves provide basic protection from catastrophic pressure spikes, pressure relief valves help control the pressure variations that are often a normal part of most process operations that result in undue stress on pumps. Properly regulating pressure with pressure guided piston relief valves protect downstream pumps and systems from ongoing damage, preventing failure, process downtime and the associated repair and operational costs.