They can be found in overfill protection as well as demand and empty indicators in process or storage vessels as well as in leakage monitoring and interface detection and can be used in all tank types and shapes, regardless of whether the vessels are metallic or non-metallic. Due to their high sensitivity, their compactness and the variety of booms, they are particularly suitable for the different process requirements of the feed industry. The well-known animal feed manufacturer Sano – Moderne Tierernährung GmbH, who is active in Germany as well as worldwide, implemented the Capanivo® capacitive level detector from UWT GmbH within its mixing tanks at the Grafenwald site in Lower Bavaria. Especially for pasty, liquid and viscous media, the capacitive probe proved to be the optimal solution for the user due to its exact surface detection and active build-up compensation.
Precise media detection with adherent raw materials

In animal feed production, similar production processes take place at virtually all production sites, such as within the mixer. An important step here is the mixing of flour or pellets with liquid raw materials such as molasses, vinasse, oils, fat or choline. The Capacitive sensors offer optimum support for the detection of filling levels in material handling processes due to their high compatibility for different process containers. The material to be inspected can have a completely different nature depending on the processing stage and can impose different requirements on the measuring technique to be used.

Since 1976, Sano has been producing milk replacers, mineral feeds and special products (such as silage agents) for cattle and pigs with clever feeding concepts and is now represented in more than 35 countries of the world. With regard to animal welfare and animal health, particular importance is attached to the use of high-quality raw materials and state-of-the-art production technology. For the innovative equipment of the level monitoring in the mixing tanks at the production site Grafenwald, the plant operator selected one of the compact capacitive measuring techniques of UWT GmbH for the material to be controlled.
After 40 years of experience and more than 1 million successfully solved applications in the area of bulk material measurement, UWT GmbH also provides smart solutions with a new capacitive sensor series in applications for liquid measurement. The devices are equipped with potted electronics and work with the innovative Inverse Frequency Shift” technology. They have a robust, certified design and offer smart solutions for all liquids, pastes and foams. Through the variation of versions with cable, rope as well as rod and tube extensions, the sensors can be easily adjusted to the respective vessel conditions and can also be used for interface detection in liquids.
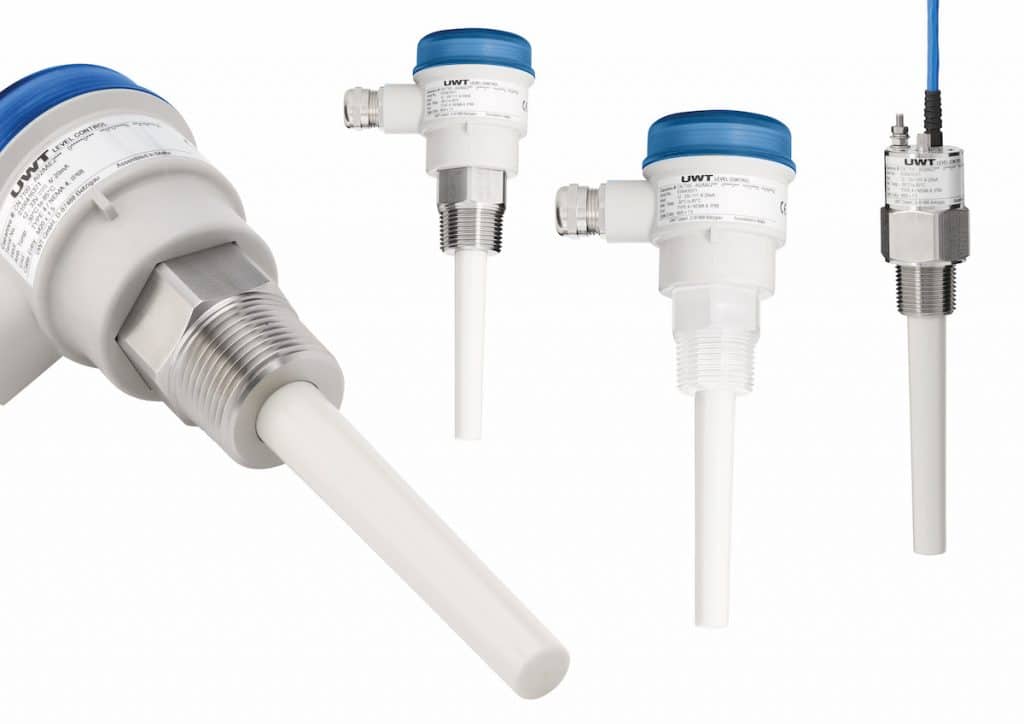
The integral version of the capacitive Capanivo® CN 7100 limit sensor has been installed in the mixers of Sano – Moderne Tierernährung GmbH. When touched by a medium, the sensor reacts to the change in capacitance on the probe arm, whereby a signal output is then switched.
The universally applicable two-wire switch is particularly suitable for limited space conditions due to its unique compact design. Besides the version with connection cable, a housing version and a complete plastic version are also available. The CN 7100 guarantees a safe flow of media within the mixer despite vibrations and the fact that some of the liquids are viscous and adherent, which is compensated by the integrated tip sensitivity”.
With its reliable media detection and short reaction time, it helps to ensure the correct mixing proportion of the individual components, the homogeneous distribution and also the lasting quality of the end product. About 50-100 kg of liquid components of the most different liquid media are added to about 3 tons of solid content, in the mixers. These are injected into the mixing container within one minute by a special injection device. For this purpose, the various liquids are injected from storage tanks or mobile containers (GRP), with a pressure of up to 5 bar, into the mixing container via a distributor attached to the mixer. The Capanivo® CN 7100 level switch installed in the distributor ensures both that the liquid intended by the control system is present in the distributor (= media detection) and at the same time that it is available in sufficient quantity, thus guaranteeing the correct and quantitative supply to the various formulations.

A particular challenge of the plant is that only one distribution device is attached to the mixer. This is fed with the different liquids one after the other, pressure is built up and from there the liquids are then distributed to injection lines and pumped into the mixer at different points. The design of the sensor used implies food-conforming materials and is universally applicable. It detects all liquids with the highest degree of safety even if the previous liquid still adheres in one layer to the sensor and inside the distribution device and is only rinsed out by the subsequent liquid. All these requirements are meet by the UWT Capanivo® CN 7100.