Therefore, it is the method of choice when it comes to measuring precious and hazardous media under the most challenging process conditions and in the harshest environments. FLEXIM’s clamp-on ultrasonic flowmeter systems, FLUXUS, is therefore found throughout the entire value chain of the Oil & Gas industry, from the well to consumers, both in liquid and gas flow applications. Furthermore, thanks to a specially designed transducer mounting system, FLEXIM’s patented WaveInjector, it is even possible to measure flow at temperatures below the boiling point of LNG, i.e. -161 °C.
Measuring from the safe side
Measuring from the outside of the pipe means measuring from the safe side. Installation and commissioning of an ultrasonic flowmeter does not require opening of the pipe and therefore the availability of the plant is unaffected. Since the transducers do not come in direct contact with the medium, they are not subject to wear and tear. This external measurement works independently of pressure changes in the pipe and does not cause any pressure loss or risk of leakage. An additional advantage of the acoustic measurement lies in its extreme dynamic range, independent of the flow direction: ultrasonic flow measurement is inherently bidirectional and active even at very low flow conditions.
But the application range of the non-invasive technology is not limited to mere flow measurements. Its analytical capabilities make it particularly suited for measuring tasks within the hydrocarbon processing industry.
Clamp-on ultrasonic measurement
Similarly to most ultrasonic clamp-on flow meters used in industrial applications, FLEXIM’s flowmeters, FLUXUS, operate according to the transit-time principle. The transit-time method exploits the fact that the transmission speed of an ultrasonic signal depends on the flow velocity of the carrier medium. Comparable to a swimmer swimming against the current, an ultrasonic signal moves slower against the flow direction of the medium as compared to traveling with the flow direction. For measurement of flows, two ultrasonic pulses are sent through the medium, one in the direction of the flow, and a second one against it. The transducers are alternatively working as emitter and receiver. The transit time of the ultrasonic signal propagating in the flow direction is lower than the transit time of the signal propagating against flow direction. The transit-time difference Δt is measured, allowing for the determination of the average flow velocity of the medium along the propagation paths of the ultrasonic signals.
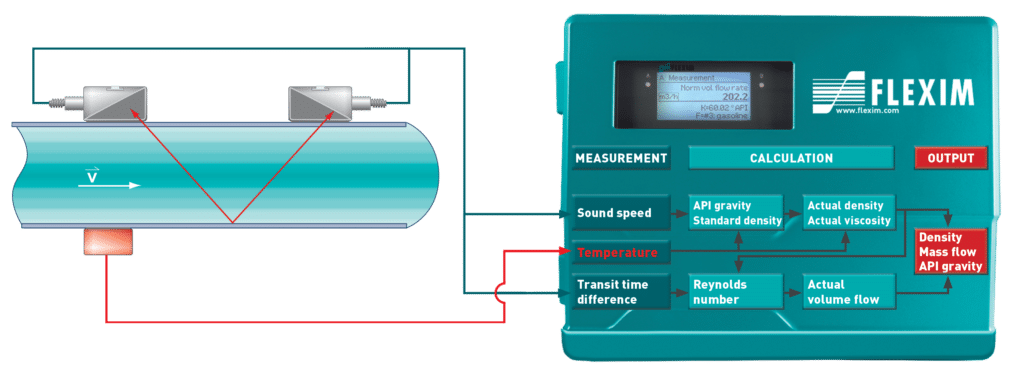
Exactly the same arrangement of clamp-on ultrasonic transducers mounted onto the outside of a pipe allows the meter to also determine the acoustic velocity in the medium. This depends on the density – and therefore also on the temperature – of the medium and is a substance-specific quantity.
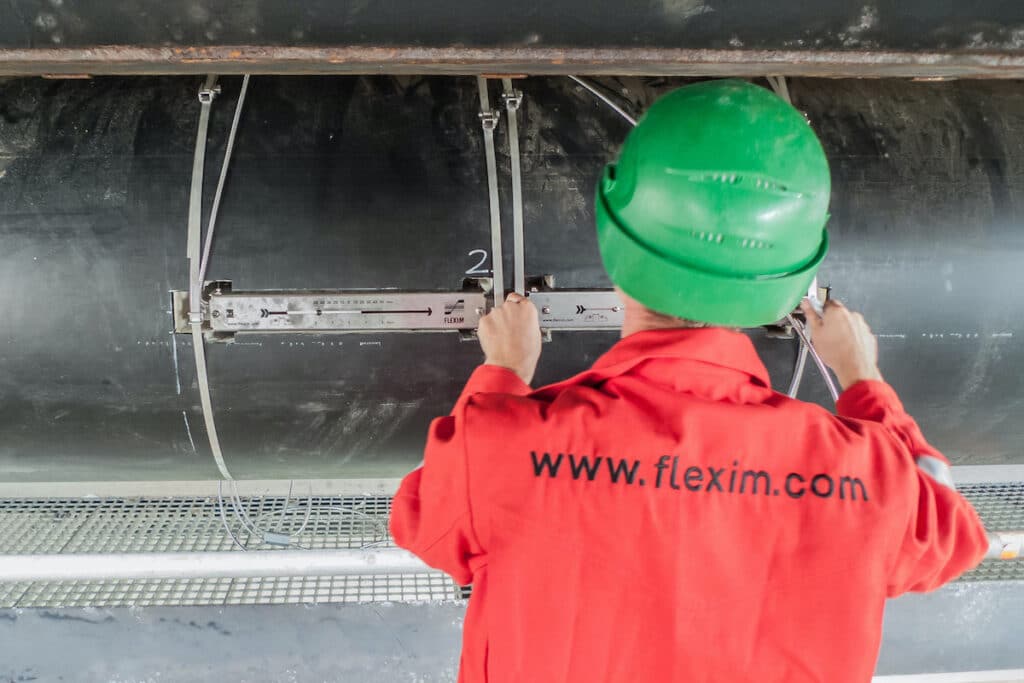
A measuring system for the hydrocarbon industry
With its FLUXUS H721, FLEXIM has developed an ultrasonic flow measurement system specifically for the needs of the hydrocarbon industry. It combines highly precise non-invasive measurement of volume flow and sound speed with sophisticated calculation features. The transmitter’s internal HPI computer calculates API gravity, operational density, density at base conditions and kinematic viscosity. Temperature and pressure compensation according to industry standards such as ASTM1250, GPA TP25 and D4311 allows for precise standard volume flow measurement of liquid hydrocarbons. The FLUXUS H721 is equipped with a database for a wide range of applications from light hydrocarbons to crude oils and refined products to heavy hydrocarbons. Application-specific configuration is easily accomplished via an editable table on the transmitter with liquid names and specific properties (density, API).
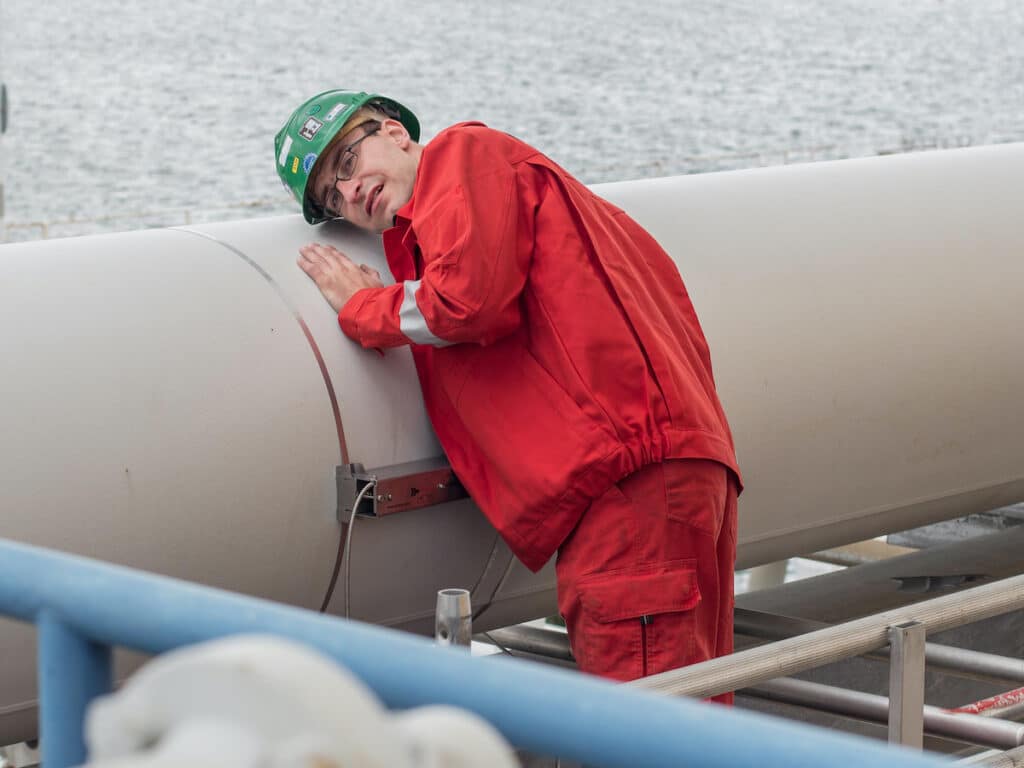
Conclusion
FLEXIM’s non-invasive ultrasonic measuring technology delivers convincing solutions to effectively increase operational safety while maximising availability and efficiency in handling hydrocarbons. When safety is paramount and downtime is not an option, the best way is to measure from the outside of the pipe.
Advanced analytical capabilities
- Identification of hydrocarbon products from the outside of the pipe
- Clear detection of interfaces between changing media
- Determination of API gravity and calculation of density and kinematic viscosity according to industry standards
- Non-invasive measurement of operational volume flow rate, flow velocity, standard volumetric flow rate and mass flow rate
Reliability
- No direct contact with the medium equals no wear and tear
- Accurate measurement over a wide range of pipe sizes and process conditions
- Ability to measure bidirectional flow (loading and unloading operations)
- SIL2-certified product variants available
Full Plant Availability
- No process interruption during installation & commissioning
- Easily retrofittable to existing plant layout, no need for piping modifications
Overall Cost Reduction
- Reduce plant energy consumption – due to zero pressure drop when compared with wetted instrumentation
- No need for wetted alloys
- Zero maintenance