Their existing metal-seated valve design had to be improved and even replaced, and for good reasons. Their valves had only a single isolation design, and exposed the risk of leakage due to the number of potential leak paths they contained.
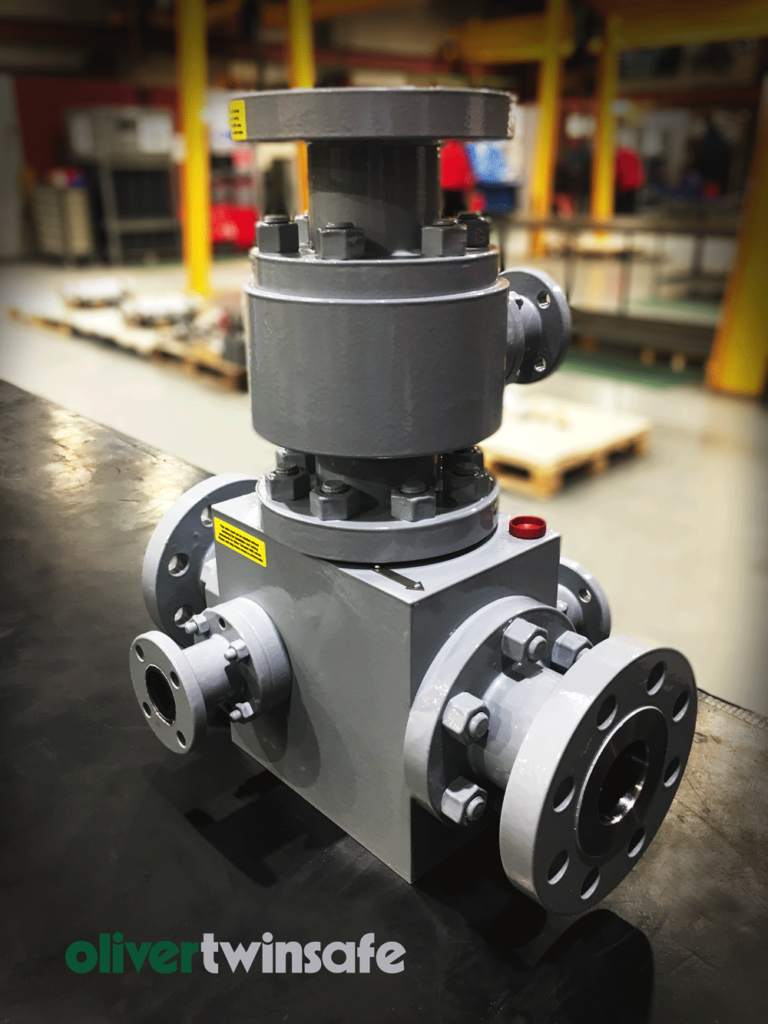
The perfect solution would be for the valve design to have far fewer leak paths, metal-seating with zero-seat leakage, and a compact design that reduces overall space and weight.
Fast forward a few weeks and the engineering team at Oliver Twinsafe custom-designed a 2” / 300lb Double Block and Bleed (DBB) valve supplied complete with actuators and utilization of all ball valve operation. The team took onboard all of the technical requirements, used existing and proven valve technology and materials to create the perfect solution to this problem. It’s often said, that when engineers creatively let off steam, it usually results in some of the most amazing solutions, and this has been no exception.
On completion of initial trials, the 2” DBB valves are to be installed on other UK and overseas processing plants.