With leakage-free and durable canned motor pumps, HERMETIC-Pumpen GmbH offers a comprehensive pump concept that has several advantages over other pumping technologies in high-temperature applications. The self-cooled and externally cooled series up to API685 including different motors for high temperatures and heat exchanger variants as well as suitable measurement and control technology offer system operators a pump solution perfectly matching their application. The secondary containment and other design features ensure safe and continuous system operation with low life cycle costs.
Heat is one of the most important parameters in process engineering. Many chemical processes can only take place at high and defined temperatures. The centrifugal pump takes on two important tasks: Firstly, it transports the heat safely and efficiently to the process engineering consumers, and secondly, it conducts the pumping within the high-temperature process chain.
Providing the process heat for consumers
An indirect supply of heat using heat transfer fluids is required for the exact setting or situational adjustment of the required temperature levels. A circulating heat transfer medium is used for heat transfer between the heater and the heat consumer. A circulation pump keeps the circulation going.
For temperatures up to 200°C, water is usually used as a heat transfer medium due to the high specific heat capacity of water and the low environmental impact. Due to the strong increase in vapor pressure at temperatures above 200°C, organic heat transfer fluids are used above this temperature instead of water. However, these fluids are not always harmless as many of them are not environmentally safe. They can also pose a major hazard potential, for example, when the flashpoint of the medium is below the operating temperature and an ignitable mixture develops during leaks. The elevated temperatures require careful selection and installation of the equipment used for the heating circuit. Hermetically sealed pumps are considered the safest.
Demanding conveying task within the process chain
When pumping the process liquid within the process chain, the pump is often confronted with difficult operating conditions: elevated temperatures may be accompanied by high pressure that can reach several hundred bar. A high solidification point of the liquid may also cause problems in meeting the pumping requirements requiring a specific, often costly, heating solution for the pump. The presence of solids such as catalysts may pose a serious challenge to the mechanical seal used in standard chemical pumps.
Challenges in hot applications: Forces and moments on pump nozzles
In high-temperature applications, pump technology must overcome demanding mechanical challenges. The elevated temperatures cause thermal expansion of the pump housing. The piping acting on the pump nozzles can develop strong forces and moments. For temperatures up to +320°C, standard chemical pumps are usually used (with mechanical seals and foot mounted on the base plate) separated from the conventional motor by a thermal barrier. If compensators are not used – as is often the case – at temperatures above +320°C, the forces and moments of the piping system are transferred directly to the pump nozzles. This may lead to distortion and even deformation of the pump housing. On the one hand, these forces must be absorbed by a correspondingly strong housing. On the other hand, the temperature-induced expansion of the pump housing can be distributed evenly upwards and downwards by using centerline-mounted support (pump feet) as stipulated by API685. For temperatures above +320 °C and up to max. +450 °C, a hermetically sealed pump concept based on API685 is therefore often the better solution.
Thermal break barrier, mechanical seal, coupling
A challenge of standard chemical pumps is the thermal barrier required between pump and motor. At high temperatures, large dimensions are often necessary in this case compared to hermetically sealed pumps. Another advantage of hermetically sealed designs is the elimination of leakage issues at the shaft passage. Canned motor pumps offer additional protection: thanks to their secondary containment, no pumped liquid escapes to the outside even when the stator can (lining) is destroyed. The omission of mechanical seals susceptible to wear and failure ensures increased process reliability, especially in chemical reactions with catalysts. The integral and compact monobloc design eliminates the need for shaft alignment. This eliminates the need for mechanical couplings, coupling protection and often complex base plate constructions. The pump and motor are continuously aligned preventing vibration due to thermal expansion and the associated damage to bearings.
Canned motor pumps for high-temperature applications
Often designed for extreme conditions, canned motor pumps are used when liquids and gases with extreme temperatures and potential hazards are pumped. These completely enclosed centrifugal pumps in monobloc design are driven by a canned motor thanks to a common shaft using electromagnetic principles. A partial flow is used to cool the motor and lubricate the two identical hydrodynamic slide bearings. After flowing through the gap between rotor and stator, the partial flow is fed back through the hollow shaft to the pressure side of the impeller. For high-temperature applications, HERMETIC offers two distinctive designs: canned motor pumps with externally cooled motors and canned motor pumps with adequate internally cooled motors.
Canned motor pumps with externally cooled motors
In this concept, the pump and canned motor are separated from each other by a short intermediate piece for thermal decoupling. This prevents the transfer of heat from the pump to the motor. A long, narrow annular gap equalises the pressure between the hydraulics and the rotor chamber. An auxiliary impeller is installed in the motor that circulates the fluid of the same type in the rotor chamber through an external cooler arranged around the motor or mounted separately. The thermal loss from the motor is absorbed by a coolant. This creates two delivery circuits with different temperature levels. The operating circuit can be approved for temperatures up to +480 °C, while the pumped liquid of the secondary cooling / lubricating circuit has significantly lower temperatures of +60 °C to +80 °C. The motor winding can therefore be designed using the durable insulation class H (H-180 winding, up to 180 °C). As a result of the pressure equalisation in the annular gap of the thermal barrier, there is virtually no fluid exchange between the two temperature levels. By using a separate cooling circuit, it is not necessary to cool the motor part flow from the high operating temperature level to a value permissible for normal canned motors and return it to the delivery flow. This would cause excessive energy loss. This cooler variant or layout can be used with single and multi-stage canned motor pumps. Depending on the use and application, this version is equipped with a plate or tubular heat exchanger. If no cooling water is available, air coolers of diverse designs can also be used. Available are simple honeycomb coolers with fans that are arranged above the unit and attached to the base plate. For larger pump outputs, separately installed system dry-air coolers with axial fans are used.
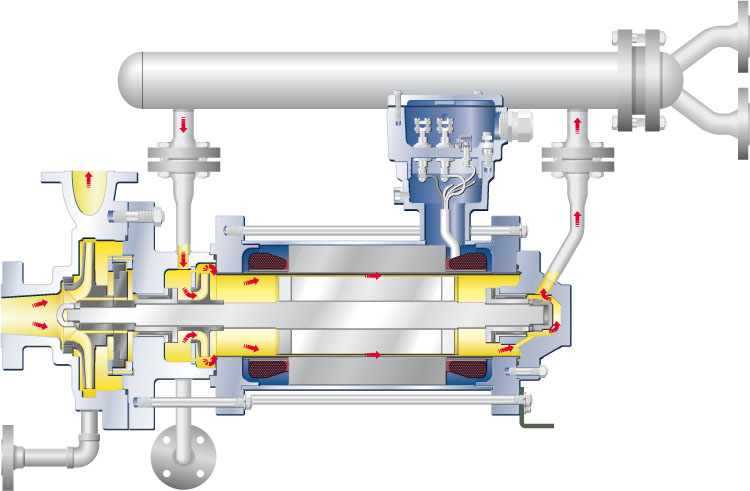
Canned motor pumps with self-cooled internally cooled motors
If not enough or no cooling liquid of sufficient quality is available for motor cooling, another design must be used. For pumped media of various types, it is also necessary to heat the pumped medium both in the pump and in the canned motor before start-up. The temperatures required in this case are usually in a range that exceeds the maximum permissible temperature for the aforementioned insulation class H. This is where the canned motors with the special winding of insulation class C (C-220 winding, C-400 winding) are used. With the so-called “high-temperature motors”, various pumping operations in the high-temperature range can be easily solved. Silicone ceramic is used as the insulation material applying suitable measures to prevent the copper wire from oxidizing. Windings of this type can manage constant temperatures of +450°C in the winding ends. This allows economic motor loads up to +400°C (temperature of the pumped medium). Fins arranged centrally on the motor housing improves heat dissipation through natural convection in self-cooled canned motors.
The performance range of the HERMETIC pump portfolio
As a specialist for canned motor pumps, HERMETIC-Pumpen GmbH offers various series that are suitable for high-temperature applications. The portfolio includes self-cooled pumps for liquid gases, boiling media, and condensates, externally cooled pumps for hot organic heat transfer oils, and heating bath liquids including design variants according to API685. The performance range covers fluid temperatures up to +480°C, system pressures up to 120MPa, and power ratings up to 690kW. The rotor lining, one of HERMETIC’s core competencies, is manufactured using the extrusion process and, as a nickel-based alloy, is an essential part of the highly efficient canned motor. In the flameproof encapsulated version, the canned motor complies with the explosion protection according to Directive 2014 / 34 / EU.