“There’s so much value in it,” says Harry Davies at Hopes Ash Farm, near Ross-on-Wye, “so now, and looking ahead to the future, we must look at how to get the best out of it.” After achieving a BSc (Hons) Agriculture degree at Harper Adams University that included his dissertation about stripping nutrients out of slurry, it is no wonder that the enterprising 23-year-old is keen to implement solutions and dig deep to find more answers.
The core of the Davies’ fifth-generation family business remains its 130-head dairy herd, but with beef, sheep, poultry, arable and 100kW of solar, there’s a very bold tick in the box of diversification as Harry, with input from Dad (Rob), and Grandad (Bryan) determinedly push forward with sustainable solutions.
Latest addition to future-proofing the Davies’ business is a new Anaerobic Digestion (AD) plant. Not that Harry wants to deter any dairy farm from making the same investment, but his experience so far shows that getting a biogas plant up and running never seems to be straightforward!
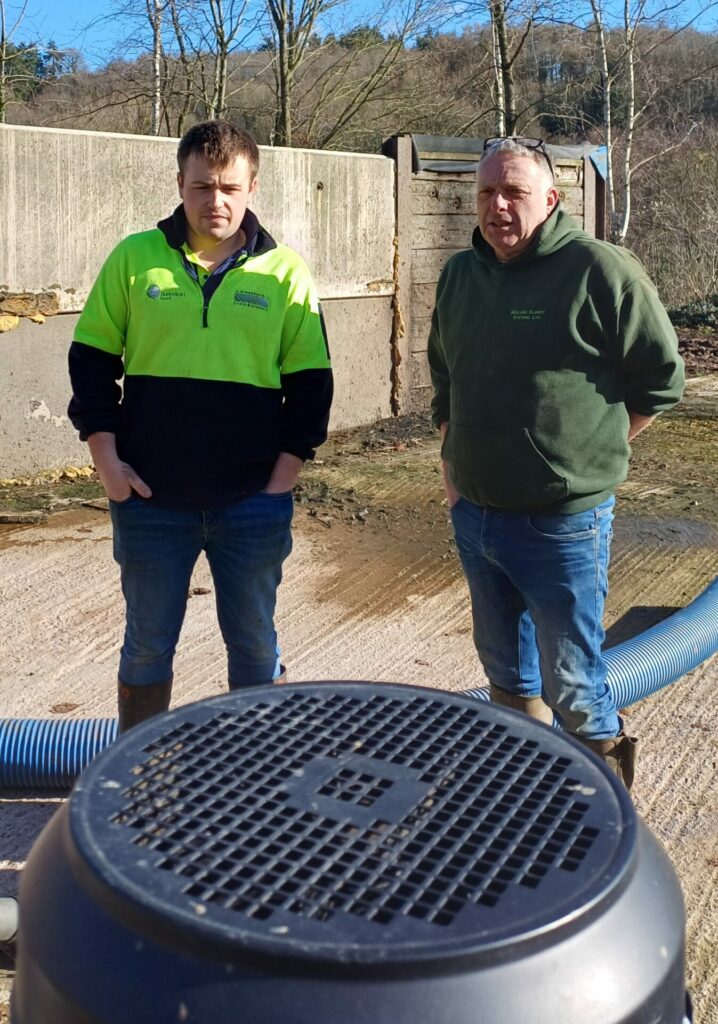
“I never thought it would be simple,” he said, “but the benefits we’re already seeing make all the effort very worth it. I might have given you a slightly different answer when we were trying to deal with the pipework, planning issues, pumping and road closures! For all of the complexities and nurturing of the biological process, the biggest challenge initially was how to transfer slurry from one side of the road to the other.”
‘The long-term well-being of the farm’
With robotically-milked cows (who bed on dried, recycled paper crumble), an automated scraper system, and a standard slurry pump all ticking along nicely, one could be forgiven for sitting back and admiring the view, but for Harry, all those slurry nutrients just had to be captured for the long-term well-being of the farm; not to mention his passion for the agricultural sector to not just survive, but prosper.
From the underground slurry reception pit (approximately 120m3), the existing pump had no issues, but it wouldn’t have had enough pressure to send it more than 200m over the road to the farm’s new AD plant. So, the Davies family sought advice from their long-standing dealer, Midland Slurry Systems (MSS), who had previously supplied the scraper system. Their recommendation was a long-shaft chopper pump from Landia, which they’d installed on numerous farms, as Giles Russell, Director at MSS, explains:
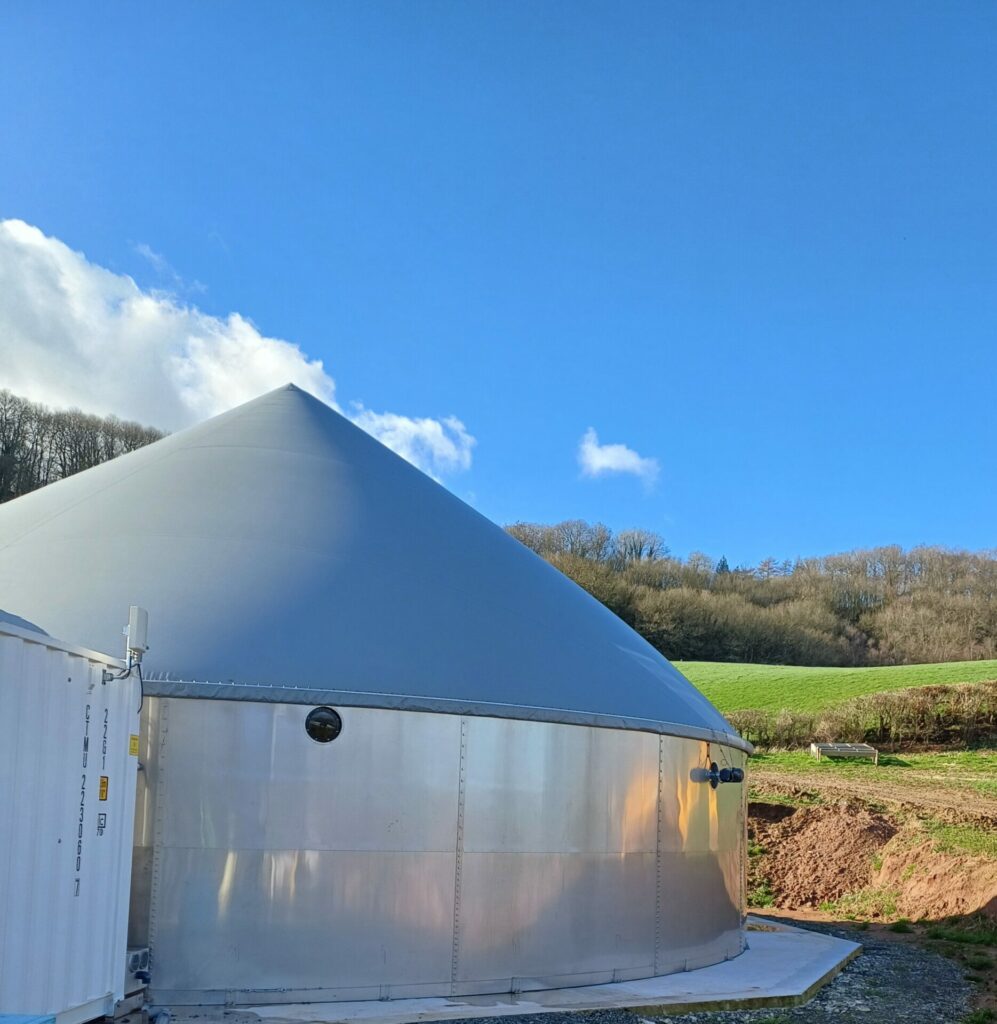
“This would be the furthest distance we’d asked a Landia pump to move slurry, but we were confident. In over 20 years, we’ve never had to take a Landia pump out of commission; they’re fully repairable, but the pressure was well and truly on. This was our largest value job of the year, including getting all the pipework installed under the road and making sure that the installation was bob-on for Hopes Ash Farm.”
The new 6” pipework successfully linked into the new AD plant, taking in slurry sent from the 15kW Landia long-shaft pump, which runs four times per day. From the AD plant (maintained at 43 degrees), the processed slurry is then mixed in a 30m3 pit before being pumped up to the screw-press separator (also supplied by Midland Slurry Systems, together with a control panel for all the equipment by the 290m3 AD plant). As the important nutrient-rich solids are collected in the bunker beneath, the separated liquid goes into a 10,000-litre above-ground tank, before being pumped via a 4” pipe back under the road to the main slurry store.
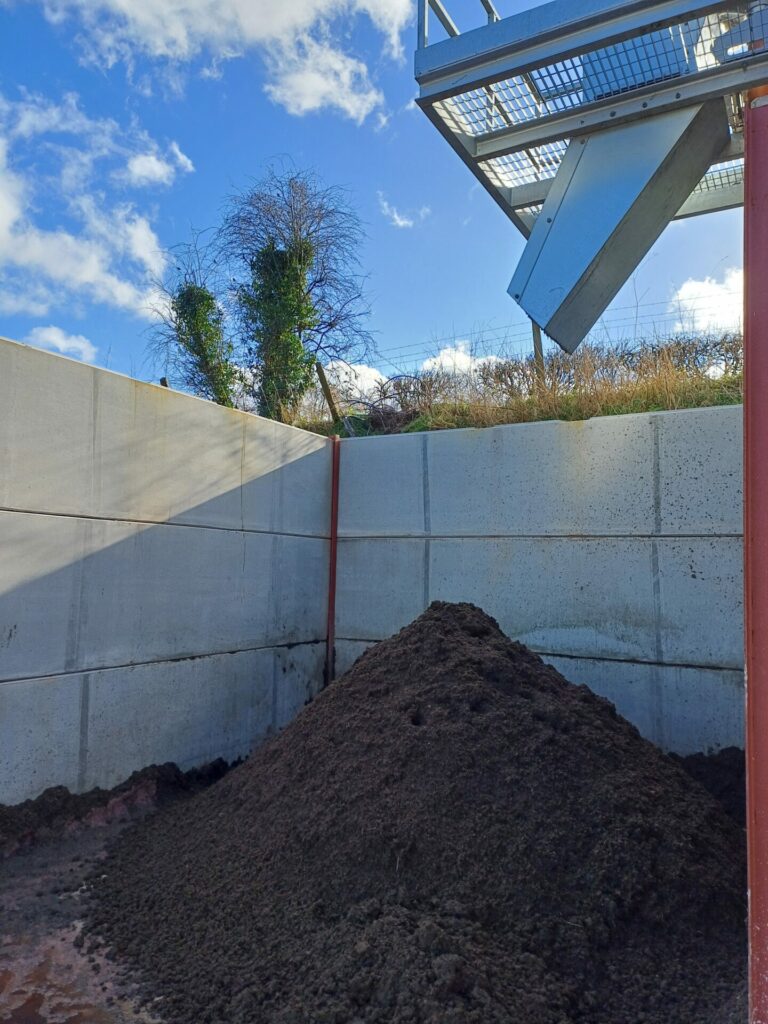
“Everything is joined up and working away, fully automated, from the moment it falls out of a cow,” continued Harry Davies, “but, the challenge is to now fine-tune the whole system to make it as efficient as possible, though the weather can take some of that out of our control. We had a few initial foaming problems with the AD plant, but that’s now sorted.
“Another learning curve is the very fine line of managing the thickness of the slurry, especially when rainfall can affect the viscosity. On the one hand, we want to keep it as liquid as possible, but then the thicker the slurry, the greater the calorific value. The Landia long-shaft pump can run from just 100 seconds to up to 5000 seconds, depending on the thickness of the slurry, but at 15kW, with a 22kW AD plant, we obviously want to minimise the run-time.
“I know some farmers who are paying 50p per kWh for their electricity, whereas the numbers add up here with it only costing 30p per kWh from our new AD plant. Plus, we have solar, which makes us pretty much self-sufficient in renewable electricity.
Recognising the nutrient values and applying them appropriately
“Our aim wasn’t to export energy, but there’s a 30kW export limit anyway, due to restrictions on the grid. Typical politicians, unable to look into the future, so their underinvestment impacts on us, and I’m sure many other farms who’ve made investments and are trying to do the right thing with renewables. This also includes our efforts here with the purchase of the separator; adding value by putting most of the phosphorus in the solid, where it is needed, and most of the nitrogen in the liquid. In our part of Herefordshire, we have fragile, sandy, hungry soil, so we need organic matter to bind it together. We don’t want it to end up in the brook, so again, a very careful balancing act, maintaining organic manures, but recognising the nutrient values and applying them appropriately. Exporting the solid creates some lively debate between, me, my Dad and Grandad (!), but I’d just say that it’s all part of our very carefully considered nutrient plan!
‘Biogas is a learning curve. One size doesn’t fit all’’
He added: “Working with some suppliers in biogas is also a learning curve. Despite what some say, one size doesn’t fit all. A rigid approach does not work, whereas with Midland Slurry Systems, they did what they said they were going to do, and did it when they said they would. If only all suppliers were like that! Just before Christmas, we had a small, non-critical issue that I told Giles about. He said he’d be there between Christmas Day and New Year to sort it out. I said: ‘Giles, for goodness’ sake, I don’t want to be in the bloody slurry pit over Christmas, and I certainly don’t want you in there either, so, ‘Merry Christmas’, but now, please…… go away!!!!
“We’ve already come a long, long way with our AD plant, which we knew made total sense to include as part of our business. Looking ahead, we also need to learn how to best harness the heat from it.
“Dealer back up is vital with this investment, and we have exactly that with Midland Slurry Systems. There’s never any waiting time for spares, and since installation, the Landia pumps and mixers (five in total) just keep on working, with no issues whatsoever. Solid support and long-lasting, reliable equipment play a significant part in helping us create ‘a new known’ with real stability moving forward.”
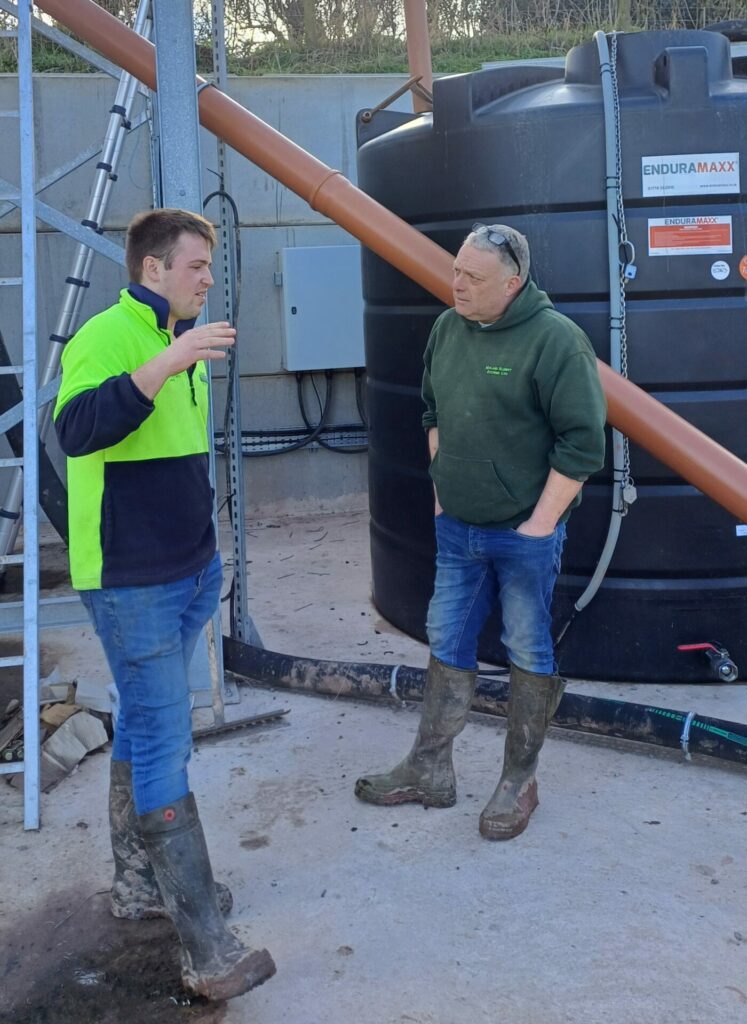