Unlike the previous applications discussed in the Magnetrol® blog series on the steam generation cycle, level control for the water treatment process is not necessarily about efficiency, but rather, accuracy, reliability and safety, while providing proper inventory management to ensure chemical and makeup water supply meets demand.
In this post, the focus is on the chemical component of the makeup water treatment since it presents difficulties for level technologies that may work perfectly on non-chemical applications related to the water treatment process or those with limited variations in the contents of the vessel’s vapor space. Although important measurements such as ammonia, acid, caustic and other chemical storage tanks are not difficult level applications by any stretch, small nuances in how the vessels are monitored relative to level technology can have a dramatic effect on the day-to-day practicality and reliability of the type of instrument(s) used.
Additionally, there are safety considerations when replenishing chemicals as well as short and long-term maintenance costs, which can be addressed simultaneously with inventory monitoring by implementing a few simple, cost-effective modifications to the instrumentation package.
Level Measurement Challenges and Considerations
Chemical storage, demineralization and water header tanks come in a variety of shapes and sizes, usually horizontal or vertical vessels six to ten feet in diameter/height, with the ammonia storage and demineralizer tanks being the largest. It is not uncommon to see some type of level transmitter (ultrasonic being the most prevalent) installed to provide level indication to the control room with a local display at the base of the tank, either in series with the 4–20 mA transmitter output or repeated from the control room. The signal to the control room tracks inventory, acts as a high alarm for overfill protection and establishes the resupply interval. The local display facilitates monitoring the offload of chemicals from the supplier’s truck.
Accuracy, reliability and visibility in dynamic vessel environments and operational scenarios are a level technology’s best attributes when addressing chemical storage applications. Cost is always an upfront consideration on these seemingly less complicated measurements. Nonetheless, performance in these two areas can have a measurable impact on the “real” cost of ownership for a plant.
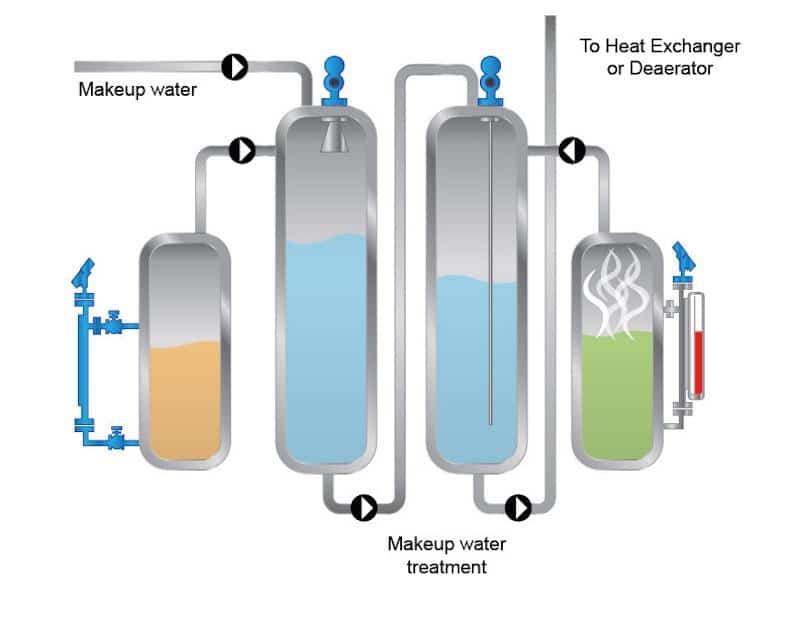
Level Measurement Solutions
Any number of level technologies can and have been used to address chemical storage. Adhering to the principles of minimizing the number of variables (e.g., vulnerability to process dynamics, calibration, hardware complexity, etc.) that can affect a technology’s ability to perform as intended is a key step in reducing the total cost of ownership.
Guided wave (contact) radar, as well as its through-air (non-contact) radar counterpart, excels in these areas. Magnetic level indicators (MLI) operating in conjunction with either type of radar technology or coupled with a magnetostrictive level transmitter offer redundancy and technology diversity while enhancing visibility for improved safety during resupply operations. There is also the added benefit of redundancy when verifying the primary transmitter’s performance during periodic inspections on scheduled outages or while troubleshooting.
This does not imply non-contact ultrasonic level transmitters or other technologies are not up to the task. Simply put, radar is indifferent to the changes in the contents of the vapor space of these vessels occurring throughout the course of the day. Oftentimes, these changes affect a technology causing what can be referred to as nuisance alarms, e.g., intermittent signal loss or when the level indication becomes erratic only to recover about the time a technician arrives on the scene. These types of issues are difficult to isolate due to their intermittent nature and the fact they cannot be linked to an installation, configuration or hardware anomaly.
Accuracy, reliability and visibility in dynamic vessel environments and operational scenarios are a level technology’s best attributes when addressing chemical storage applications. MAGNETROL’s guided wave radar transmitter, the Eclipse® Model 706, excels at providing accurate readings even in vapor-heavy and high-temperature settings.
As simple as some of these level applications appear, there is no shortage of instances where they contribute disproportionately to the commissioning and maintenance budgets simply because they cannot accommodate the full breadth of the application dynamics.
Opting for a technology-centric versus a one-size-fits- all approach to applications throughout the water treatment process reduces both short- and long-term cost of ownership. This allows for the implementation and realization of the cost benefit of entry-level technologies for less strenuous applications, while minimizing cost on those with variations in the vapor space (e.g., steam, chemical composition, excessive condensation, etc.), all of which can wreck havoc on an instrument’s performance as well as a plant’s maintenance budget.